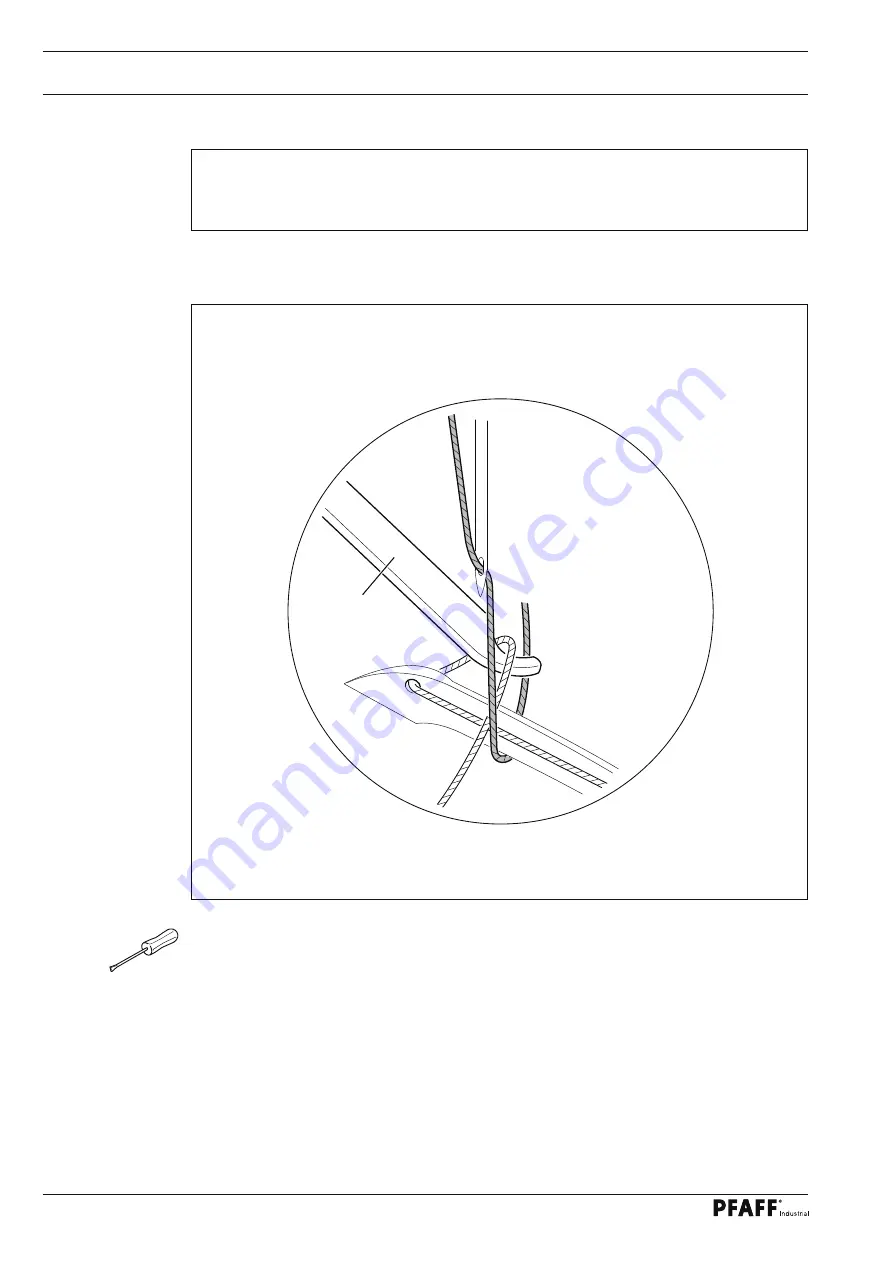
32
Adjustment
●
Thread the machine, place fabric under the presser foot and lower the presser foot.
●
Turn the balance wheel in sewing direction with depressed reverse-feed control, and
check the compliance with the
requirement
.
●
If required, readjust the spreader settings.
1
.05.25
Functional sewing test
(only for machines with -911/..)
Requirement
As seen in feed direction, the spreader
1
should reliably pick up the rear part of the need-
le thread loop and the looper thread.
Fig. 1 - 25
1