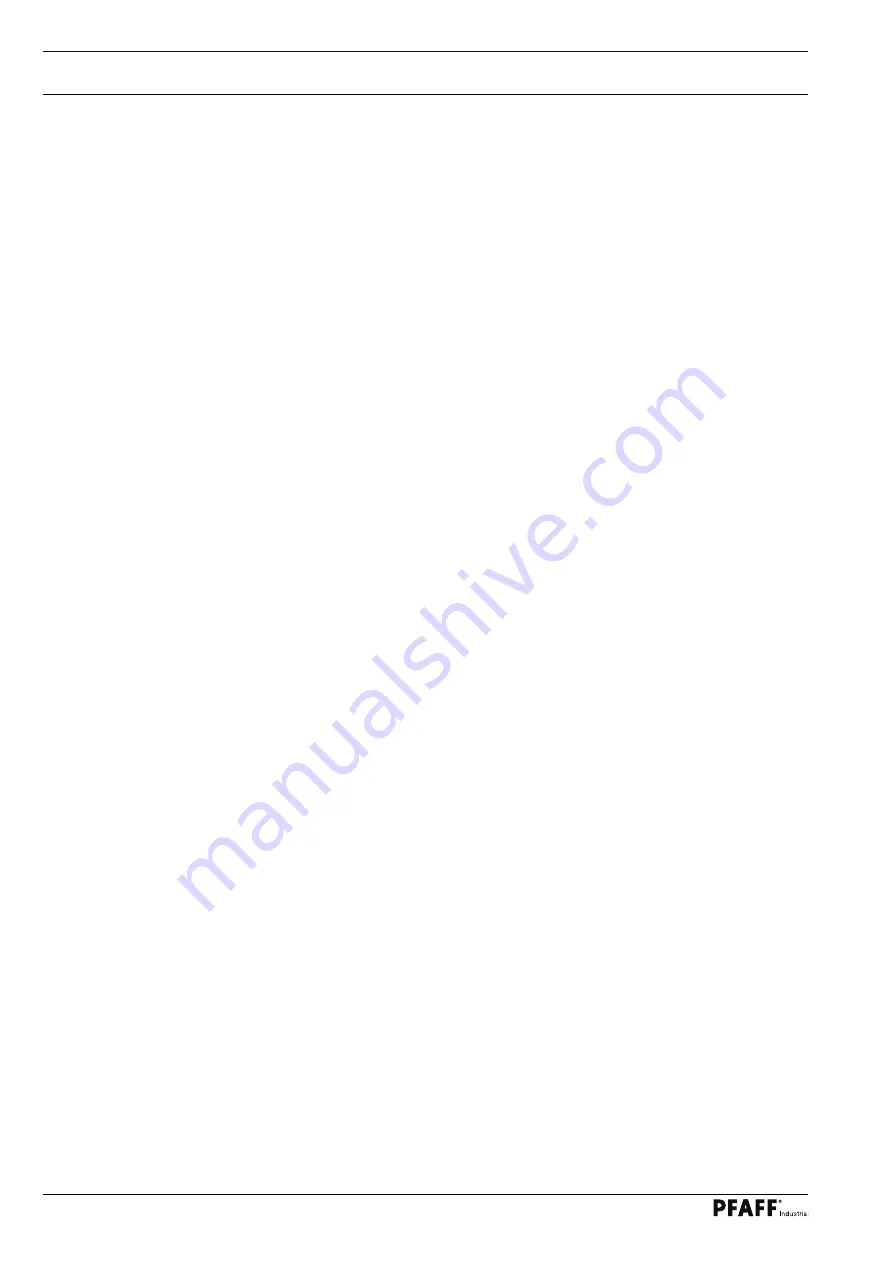
Safety
6
1 Safety
1
.01
Directives
The machine was built in compliance with the European regulations specified in the declara-
tion of conformity and declaration of incorporation.
As a supplement to this instruction manual, please also observe the generally applicable,
legal and other regulations and legislation – also in the country of use – and the valid
environmental protection regulations! Always comply with the locally applicable regulations
of the professional associations and other supervisory authorities!
1
.02
General safety instructions
O
The machine may only be operated after you have become acquainted with the associ-
ated instruction manual and only by operating personnel who have received appropriate
training!
O
Always read the safety instructions and the instruction manual of the motor manufactur-
er before starting up the machine!
O
Always follow the hazard and safety instructions attached to the machine!
O
The machine may only be operated for its intended purpose and only with the associated
safety covers, while adhering to all the relevant safety requirements.
O
The machine must always be disconnected from the power supply by pressing the main
switch or pulling out the mains plug when sewing tools are replaced (such as the needle,
sewing foot, needle plate and bobbin) and when threading, leaving the workstation, or
performing maintenance!
O
The daily maintenance work may only be carried out by suitably qualified personnel!
O
Repairs and special maintenance work may only be carried out by technical staff or peo-
ple with appropriate training!
O
Work on electrical equipment may only be carried out by qualified technical staff!
O
Work on parts and equipment under voltage is not permitted!
O
Exceptions are regulated by the EN 50110 standards.
O
Modifications and changes to the machine may only be made in compliance with all of
the relevant safety requirements!
O
Only those replacement parts approved by us for usage may be used for repairs! We
warn you expressly that spare parts and accessories that are not supplied by us are also
not tested and approved by us.
Fitting or using these products may therefore have negative effects on features which
depend on the machine design. We are not liable for any damage caused by the use of
non-Pfaff parts.