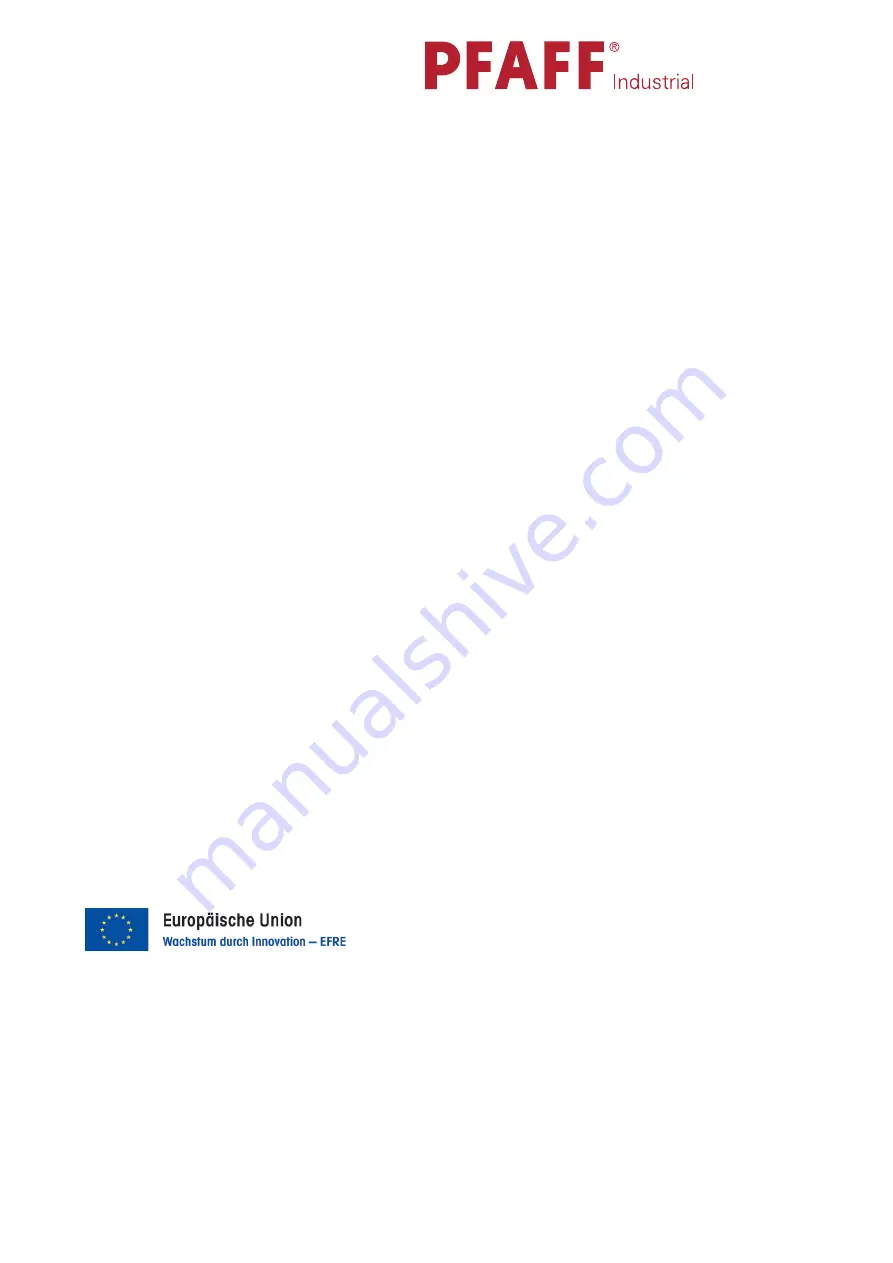
PFAFF Industriesysteme
und Maschinen AG
Hans-Geiger-Str. 12 - IG Nord
D-67661 Kaiserslautern
Phone: +49 - 631 200-0
Fax:
+49 - 631 17202
E-mail: [email protected]
Hotlines:
Technical service:
+49 - 175/2243-101
Application consultance:
+49 - 175/2243-102
Spare-parts hotline:
+49 - 175/2243-103
Printed in Germany
Summary of Contents for 1122-720/02
Page 32: ...Circuit diagrams Version 29 09 04 13 1 13 Schaltpl ne...
Page 33: ...Notes...