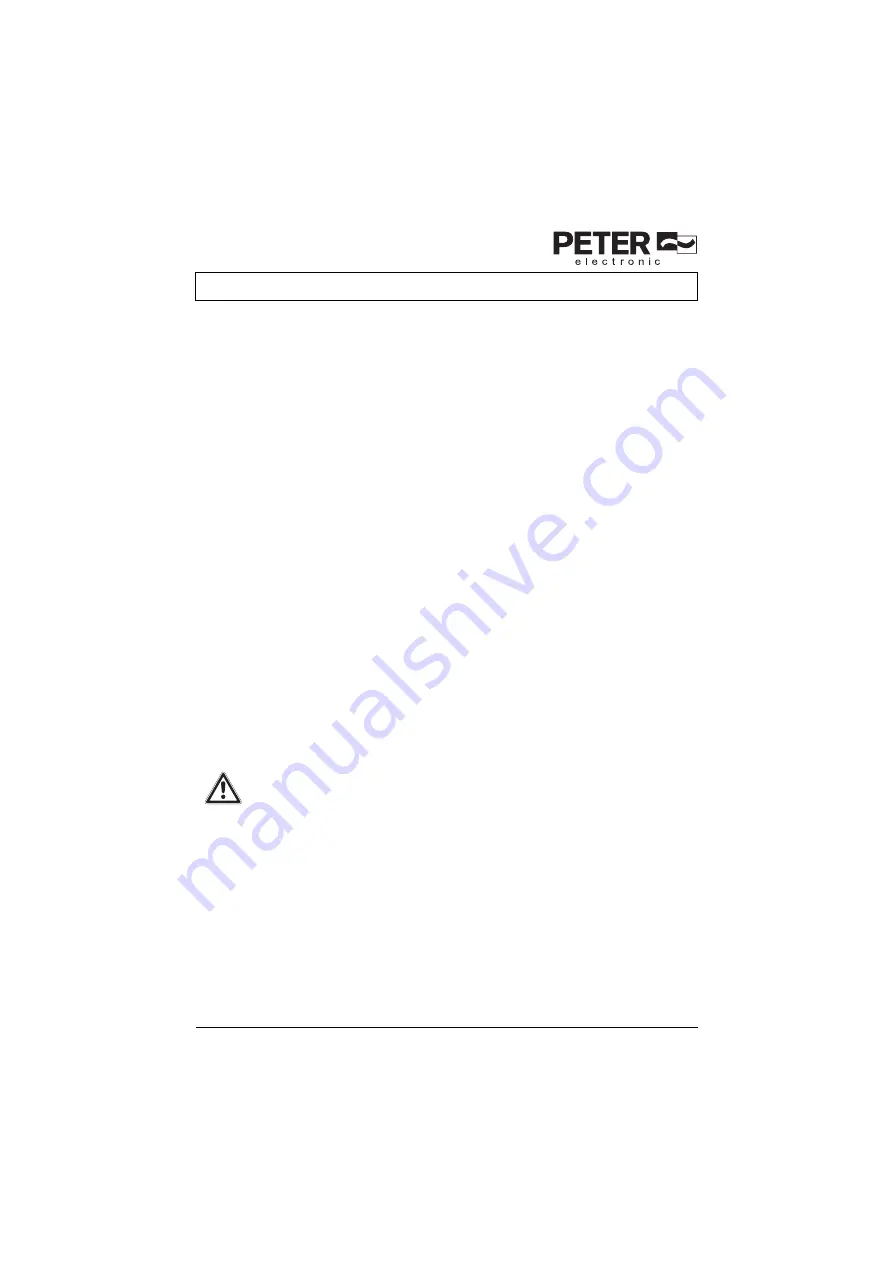
VersiSafe
17
Connect correct auxiliary voltage to terminals A-A2
==>After 1 sec the LEDs „UH“ and „OUT“ light up green and the safety contacts are switched on.
Also the monitoring relay and the semiconductor output „ON“ must be activated.
If standstill is not detected (LED „OUT“ lights yellow), possibly interference is coupled on the
measuring circuit. Adjust U
an
higher or screen the measuring wires.
Start of motor
==>
LED „OUT“ changes colour to yellow. The output relays and the semiconductor output „ON“
switch off. On DC motors the LED „ERR“ starts to flash after 2 s with flash code 2 and the output
„ERR“ comes on.
Stop of motor - run down or DC braking
The speed at which standstill is detected (yellow LED „OUT“ changes to green/green flashing)
can be adjusted on Potentiometer „U
an
“. When the run down is very slow or irregular the time
delay must possibly be increased to avoid switching on and off of the output relays. Possibly this
effect can also be avoided by slightly increasing U
an
. During time delay t
s
the LED „OUT“ flashes
green.
If standstill detection shall only take place at very low speed of the motor, U
an
is set normally to
minimum. By increasing the delay time t
s
a possible pulsing of the output relays can be avoided.
A longer time delay will also guarantee standstill detection only when the motor has already
stopped turning. (especially on motors that generate only a small remanence voltage).
On slow decrease of motor speed it is possible that a simultaneity failure occurs (see failure
monitoring) when the measuring channels reach the tripping values slowly and not within 2.5 sec.
To avoid this failure a single phase connection could be the solution (to make sure that both
inputs get the same signal) or the increase of the setting value U
an
.
If the run down time of the motor is short ts can be set to a minimum (0.2 s). This is suitable in
production systems to shorten machine cycles.
Warning:
It is the responsibility of the user to adjust Uan and ts in a way that standstill
detection and enabling of the safety contacts in the application is only
possible when danger to men and material by the rotating can be excluded.
7.3
Special applications and operation notes
Motors with switched windings
(e.g. star delta starters, reversing circuits, multi speed motors)
With these applications please make sure, that the measuring inputs must be linked via the motor
windings. An open connection will result in broken wire indication and disable the safety contacts.
When connecting the VersiSafe to a 3-phase motor with star delta starter the star contactor must
be energised while the motor is switched off, in order to achieve closed circuits between L1-L2-L3
via the motor windings.
Summary of Contents for VersiSafe
Page 29: ...28 VersiSafe...
Page 30: ......