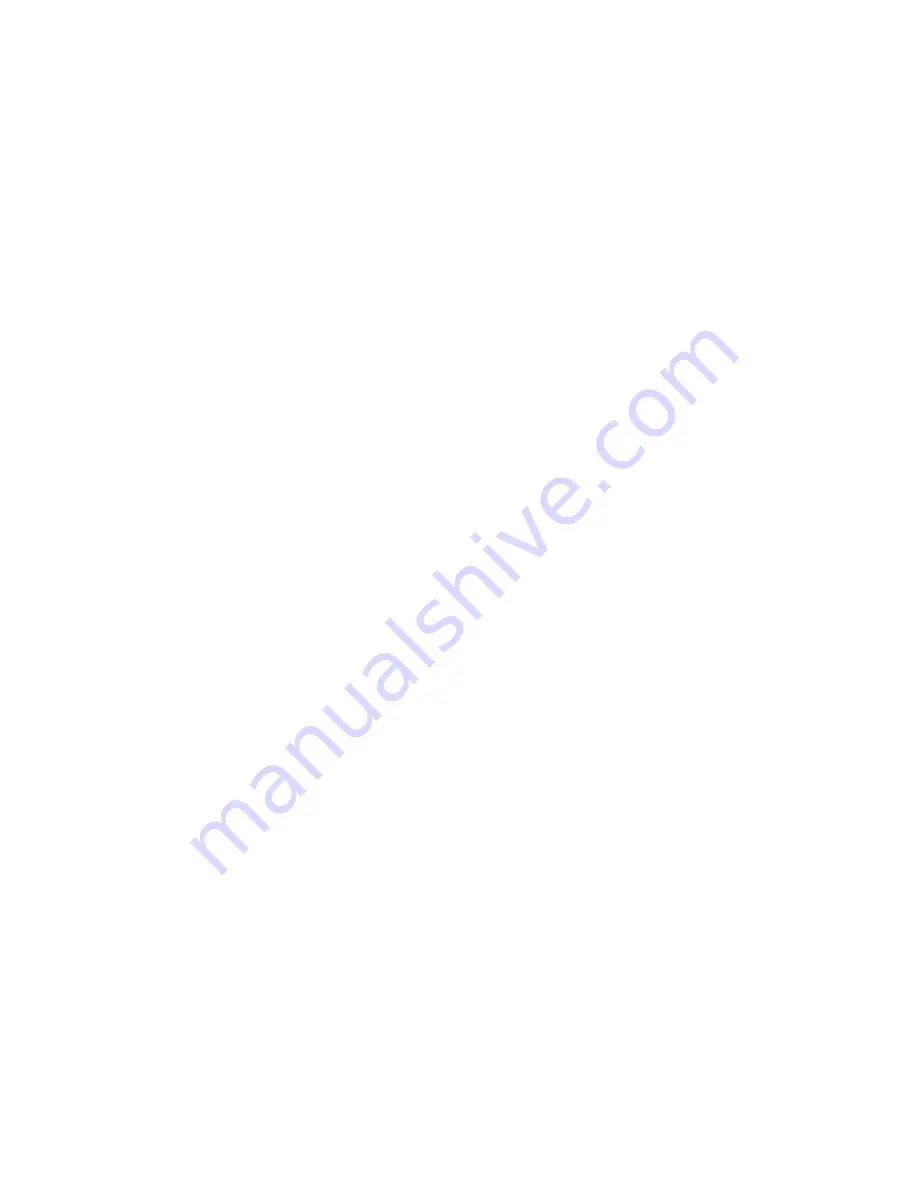
Handle assembly
Position trigger (25) in its slot in the handle body and align the holes in each part.
Drift or press home the trigger pin (26). Check the throttle lever is free to move easily.
Grip the handle body (24) in a vice protected with leather or copper covered vice jaws.
Lubricate and insert throttle pin (32) into position reduced diameter out of the hole.
Replace the throttle ball (27) and throttle spring (28) and retain in place with throttle valve plug (29), apply
Loctite 243 to the threads of the plug and screw home fully.
If the air inlet (30) has been removed, refit it into the handle body using Loctite 243 and screw home fully.
Replace the quick release coupling (31).
Main assembly
Firmly grip the cylinder assembly vertically across the flats, in a vice protected with leather or copper
covered vice jaws.
Check for correct location of the valve ring (4) valve plate (5) and spacing washer (6).
Carefully lower the handle assembly (23) onto the cylinder and engage the threads. Tighten the handle
down by hand.
Fully tighten the handle using the 1.5 meters long pipe until the lock pin (7) can be replaced in position –
thread to the outside.
Slide the muffler (9) down the cylinder until the muffler retaining lip engages with the groove in the
cylinder. Replace the retaining clip (10) in its groove in the cylinder (SK9 models only).
Assembly of the fronthead – Screw retainer models
Replace the sealing ring (8) in its groove in the cylinder.
Inspect the chisel buffer (13) for wear and replace if necessary, by sliding a new buffer into the retainer.
Screw the retainer onto the cylinder assembly.
Assembly of the fronthead – Latch retainer models
Grease the latch plunger (22) and plunger spring (21) and insert them into position in the fronthead (15).
Locate the latch lever (20) with the holes in the fronthead and press or drift into place the fronthead spring
pins (18,19).
Check the operation of the latch.
Slide the fronthead (15) onto the end of the cylinder and align the bolt hole with the groove machined in
the cylinder.
Fit fronthead screw (16) and secure with fronthead nut (17) tighten
to 90 Nm (66.4 lbs.ft) torque.
Assembly checks
Following service or repair the pickhammer should be checked for correct operation before being sent
back to the job site.
Fit the correct size accessory into the pickhammer and connect to an airline. Using low pressure 2 bar
(30psi) check to ensure the pickhammer is free of air leaks around the inlet connection and also that the
pickhammer does not automatically start to operate without the trigger being depressed.
Increase the air pressure to 6 bar (90psi) and run the tool in short bursts to check the tools starts and
stops cleanly and without hesitation.
Pickhammer
operating frequency should be as given in the specification table at the end of this manual.
Summary of Contents for SK 9-5
Page 8: ......