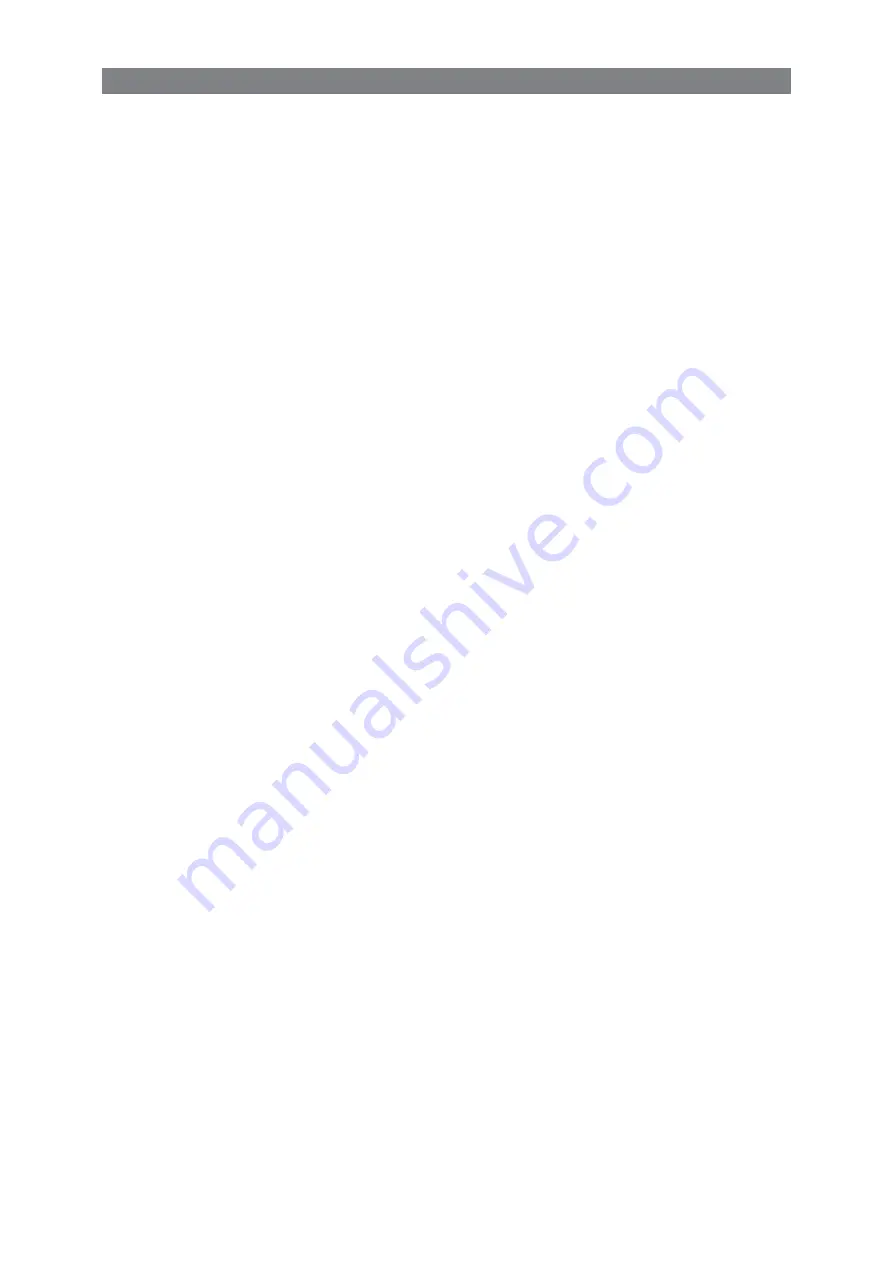
50
Trouble Shooting Guide
Troubleshooting R-net
3.22 System Error
This occurs when the control system detects an error that cannot be ascribed to a specific module.
•
Check all cables and connections.
•
Cycle the voltage.
If the error persists and the system includes third-party modules:
•
Disconnect all modules that do not come from PGDT and cycle the voltage.
If this has dealt with the error:
•
Connect one third-party module at a time and cycle the voltage each time.
•
If the error recurs after one of the voltage cycles, the last module to be connected must be defective.
If the error persists after the checks listed above, the system from PGDT may be defective. Read more
in section 5.
3.23 Gone to Sleep (energy saving mode)
This occurs when the system has not been used for a period that exceeds the Sleep Timer parameter
used for setting the energy saving mode. Each time this occurs it is registered in the system log.
3.24 Charging
This occurs when the control system detects that a charger has been connected to either inhibit contact
1 or inhibit contact 3. Read more about connectors in section 2.3.
The screen for battery charging is displayed when a charger is connected.
Each time this occurs it is registered in the system log.
When using an integral charger:
•
Disconnect the charger from the mains.
When using an external charger:
•
Disconnect the charger from the power wheelchair.
If the error persists after the charger has been disconnected, the joystick module may be defective. Read
more in section 5.
Summary of Contents for STREET
Page 1: ...Street SERVICE MANUAL Power Wheelchair US ...
Page 2: ......
Page 56: ...56 Cabling overview A B C D E F 1 2 3 4 ...
Page 57: ...Cabling overview 57 Cabling overview A B C D E F 5 6 7 8 ...
Page 59: ......
Page 60: ...Order no 205233 US 0 Street ...