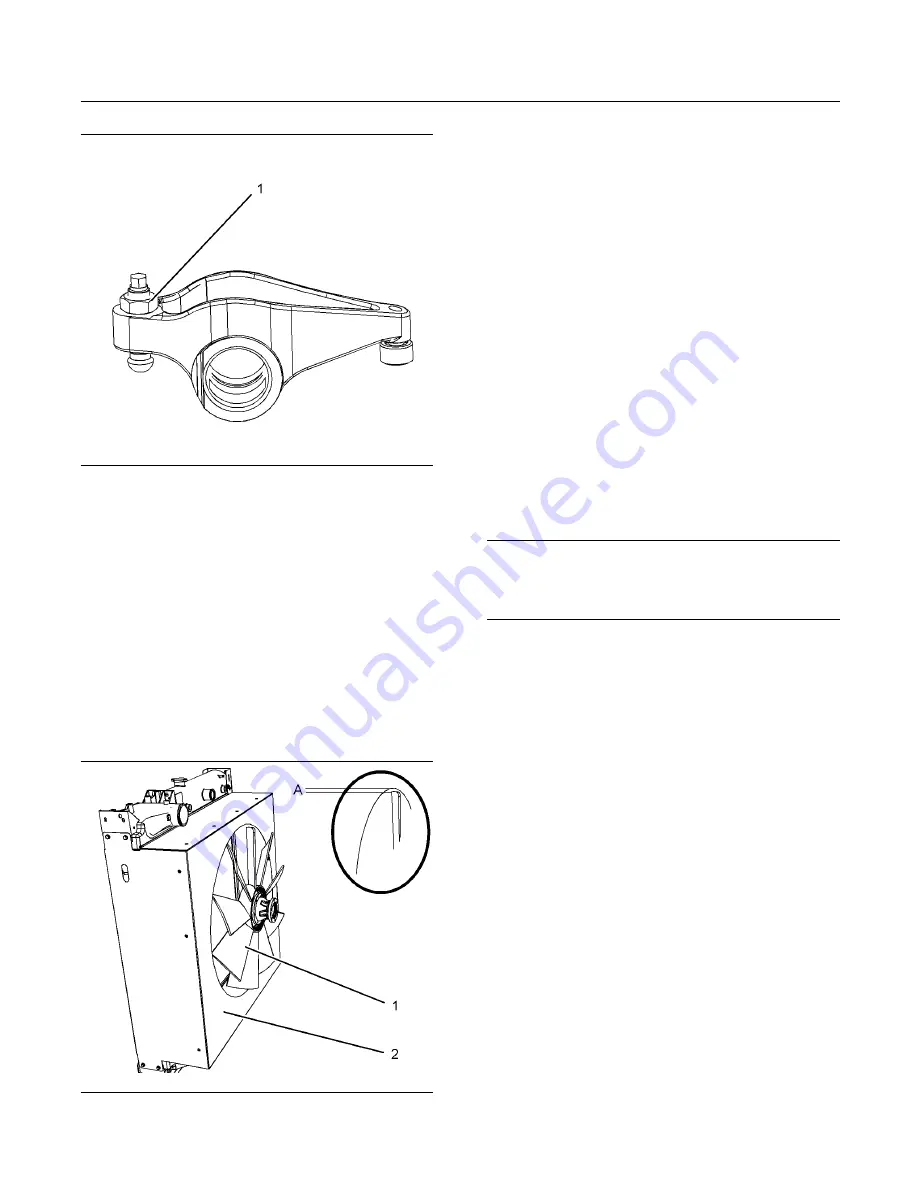
78
SEBU8455
Maintenance Section
Fan Clearance - Check
g02793699
Illustration 52
Typical example
The adjuster screw (1) must be torque to 27 N·m
(20 lb ft). After tightening the adjuster screw the valve
lash must be checked again.
Install the valve mechanism cover. For more
information refer to System Operation Testing and
Adjusting, “Engine Valve Lash -Inspect/Adjust”.
i04633518
Fan Clearance - Check
g02778616
Illustration 53
Typical example
Ensure that the engine is stopped. Ensure that the
battery disconnect switch is in the OFF position.
Ensure that the cooling system is full. The clearance
between the cover (2) and the fan (1) will require
checking. The gap (A) between the cover and the
edge of the fan blade must be checked in
fi
ve equally
spaced positions.
Adjustment of the cover will change the clearance
gap between the cover and the edge of the fan
blade. Ensure that the cover is centralized to
the fan. The clearance (A) must be 21 ± 2 mm
(0.82677 ± 0.07874 inch).
i04272833
Fuel System - Prime
Ensure that all adjustments and repairs are performed
by authorized personnel that have had the correct
training.
NOTICE
Do not crank the engine continuously for more than
30 seconds. Allow the starting motor to cool for two
minutes before cranking the engine again.
If air enters the fuel system, the air must be purged
from the fuel system before the engine can be
started. Air can enter the fuel system when the
following events occur:
•
The fuel tank is empty or the fuel tank has been
partially drained.
•
The low-pressure fuel lines are disconnected.
•
A leak exists in the low-pressure fuel system.
•
The fuel
fi
lter has been replaced.
If you inspect the engine in operation, always use
the proper inspection procedure in order to avoid
a
fl
uid penetration hazard. Refer to Operation and
Maintenance Manual, “General hazard Information”.