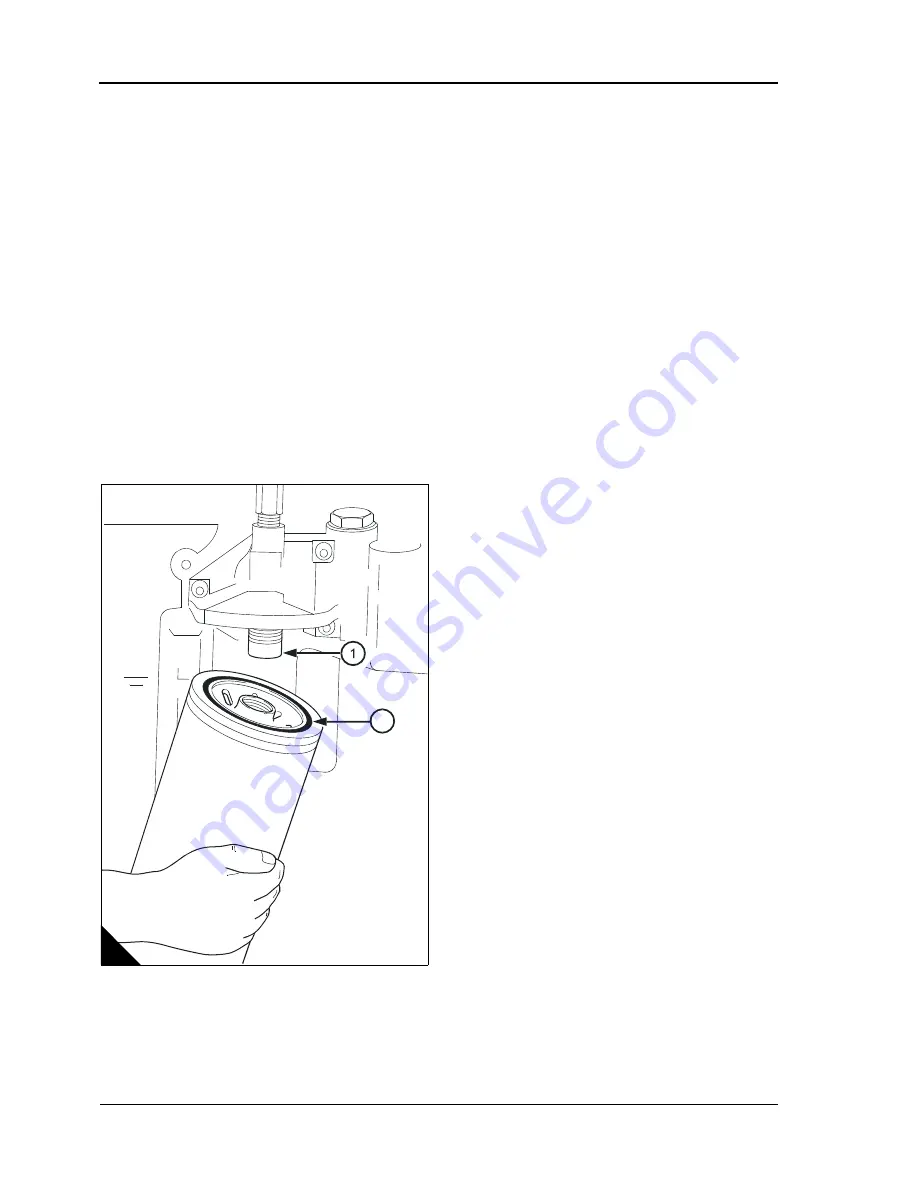
4
26
User’s Handbook, TPD 1352E, issue 4
1300 Series EDi Models WK to WS
How to renew the canister of the lubricating oil filter
1
Put a tray under the filter to retain spilt lubricating oil.
2
Clean thoroughly the outside surfaces of the filter assembly.
3
Use a strap wrench or similar tool to loosen the filter canister. Remove and discard the canister. Ensure that
the adaptor (A1) is secure in the filter head.
Warning! Discard the used canister and lubricating oil in a safe place and in accordance with local regulations.
4
Clean inside the filter head
5
Lubricate the seal (A2) on top of the canister with clean engine lubricating oil.
6
Fill the new filter canister with clean engine lubricating oil. Fit the new canister and tighten by hand until the
seal contacts the filter head. Tighten the canister a further
1
/
2
to
3
/
4
of a turn by hand only. Do not use a strap
wrench.
7
Ensure that there is lubricating oil in the sump.
8
Turn the start key to the "ON" position and start the engine.
Note:
The engine will not start and operate until oil pressure is obtained. Oil pressure is indicated when the
warning light is extinguished or by a reading on the gauge.
When the engine starts check for leakage from the filter. Stop the engine. After 15 minutes check the oil level
on the dipstick and, if necessary, put more lubricating oil of an approved grade into the sump.
Caution: Do not fill the sump past the "FULL" mark on the dipstick.
2
A
W014
Summary of Contents for WK 1300 Series EDi
Page 1: ...TPD1352E Issue 4 November 2011 User s Handbook 1300 Series EDi WK WL WM WN WP WQ WR WS...
Page 11: ...1 User s Handbook TPD 1352E issue 4 7 1300 Series EDi Models WK to WS A W002 B PW250 1 1 1 C...
Page 13: ...1 User s Handbook TPD 1352E issue 4 9 1300 Series EDi Models WK to WS...
Page 14: ...This page is intentionally blank...