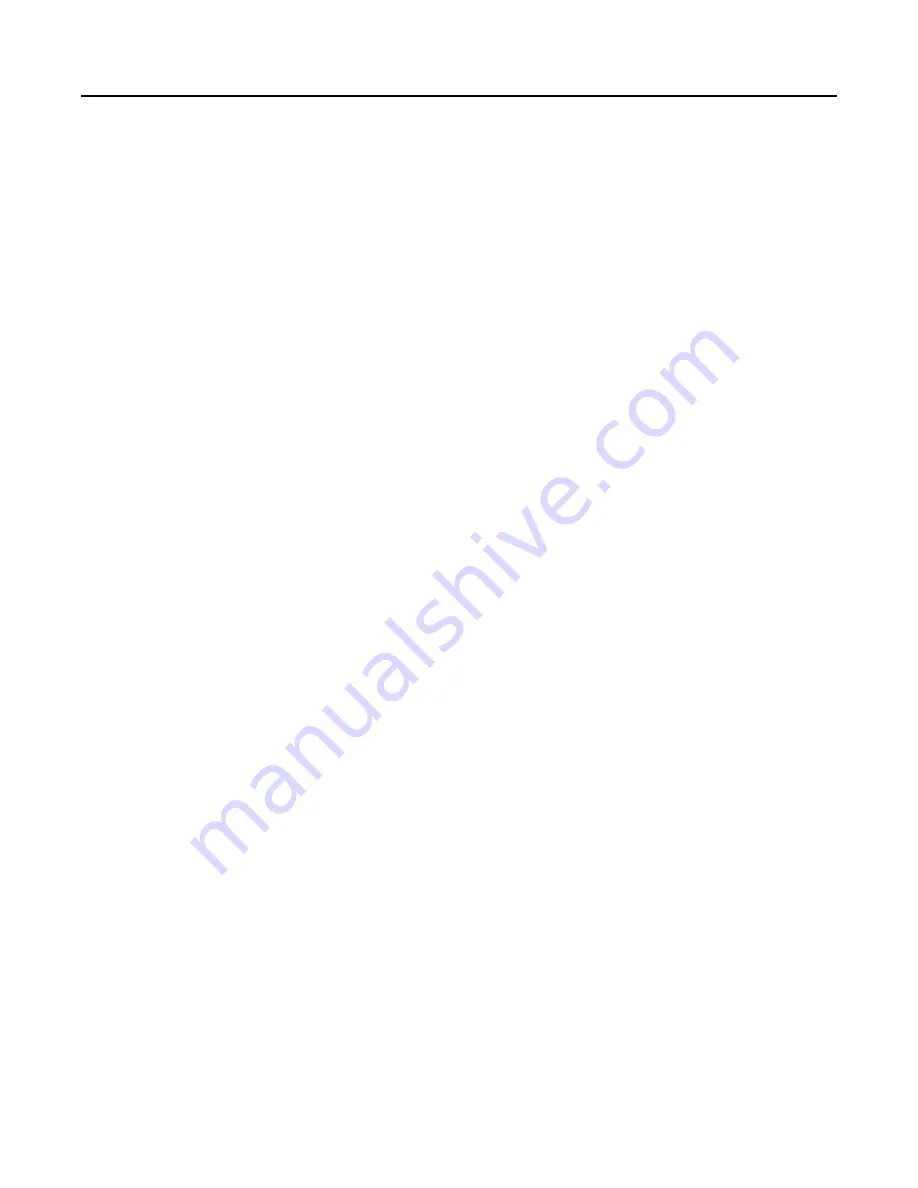
• For jump starting with cables in cold weather, refer
to the Operation and Maintenance Manual,
“Starting with Jump-Start Cables.” for instructions.
Viscosity of the Engine Lubrication
Oil
Correct engine oil viscosity is essential. Oil viscosity
affects lubrication properties and the wear protection
that the oil provides for the engine. Refer to this
Operation and Maintenance Manual, “Fluid
Recommendations” for the recommended viscosity of
oil.
At temperatures below −10° C (14° F) damage to
engine components can occur if the engine is
allowed to operate at high load and speed
immediately after starting.
Recommendations for the Coolant
Provide cooling system protection for the lowest
expected outside temperature. Refer to this
Operation and Maintenance Manual, “Fluid
Recommendations” for the recommended coolant
mixture.
In cold weather, check the coolant often for the
correct glycol concentration to ensure adequate
freeze protection.
Engine Block Heaters
Engine block heaters (if equipped) heat the engine
jacket water that surrounds the combustion
chambers. This heat provides the following functions:
• Starting ability is improved.
• Warm up time is reduced.
An electric block heater can be activated once the
engine is stopped. A block heater can be 110 V DC or
240 V DC. The output can be 600/1000W. Consult
your Perkins dealer or your Perkins distributor for
more information.
Idling the Engine
After starting the engine, the engine speed will be
governed for a maximum period of 30 seconds.
When idling after the engine is started in cold
weather, increase the engine rpm from 1000 rpm to
1200 rpm. This idling will warm up the engine more
quickly. Maintaining an elevated low idle speed for
extended periods will be easier with the installation of
a hand throttle. The engine should not be “raced” to
speed up the warm up process.
Whilst the engine is idling, the application of a light
load (parasitic load) will help in achieving the
minimum operating temperature. The minimum
coolant operating temperature is 80° C (176° F).
Recommendations for Coolant
Warm Up
Warm up an engine that has cooled below normal
operating temperatures due to inactivity. This warm
up should be performed before the engine is returned
to full operation. During operation in very cold
temperature conditions, damage to engine valve
mechanisms can result from engine operation for
short intervals. This damage can happen if the
engine is started and the engine is stopped many
times without being operated to warm up completely.
When the engine is operated below normal operating
temperatures, fuel and oil are not burned completely
in the combustion chamber. This fuel and oil causes
soft carbon deposits to form on the valve stems.
Generally, the deposits do not cause problems and
the deposits are burned off during operation at
normal engine operating temperatures.
When starting and stopping an engine many times
without being operated to warm up completely, the
carbon deposits become thicker. This starting and
stopping can cause the following problems:
• Free operation of the valves is prevented.
• Valves become stuck.
• Pushrods may become bent.
• Other damage to valve train components can
result.
For these reasons, when the engine is started, the
engine must be operated until the coolant
temperature is 80° C (176° F) minimum. Carbon
deposits on the valve stem will be kept at a minimum.
The free operation of the valves and the valve
components will be maintained.
The engine must be warmed thoroughly to keep
other engine parts in better condition. The service life
of the engine will generally be extended. Lubrication
will be improved. There will be less acid and less
sludge in the oil. This condition will provide longer
service life for the engine bearings, the piston rings,
and other parts. However, limit unnecessary idle time
to 10 minutes to reduce wear and unnecessary fuel
consumption.
M0132847
51