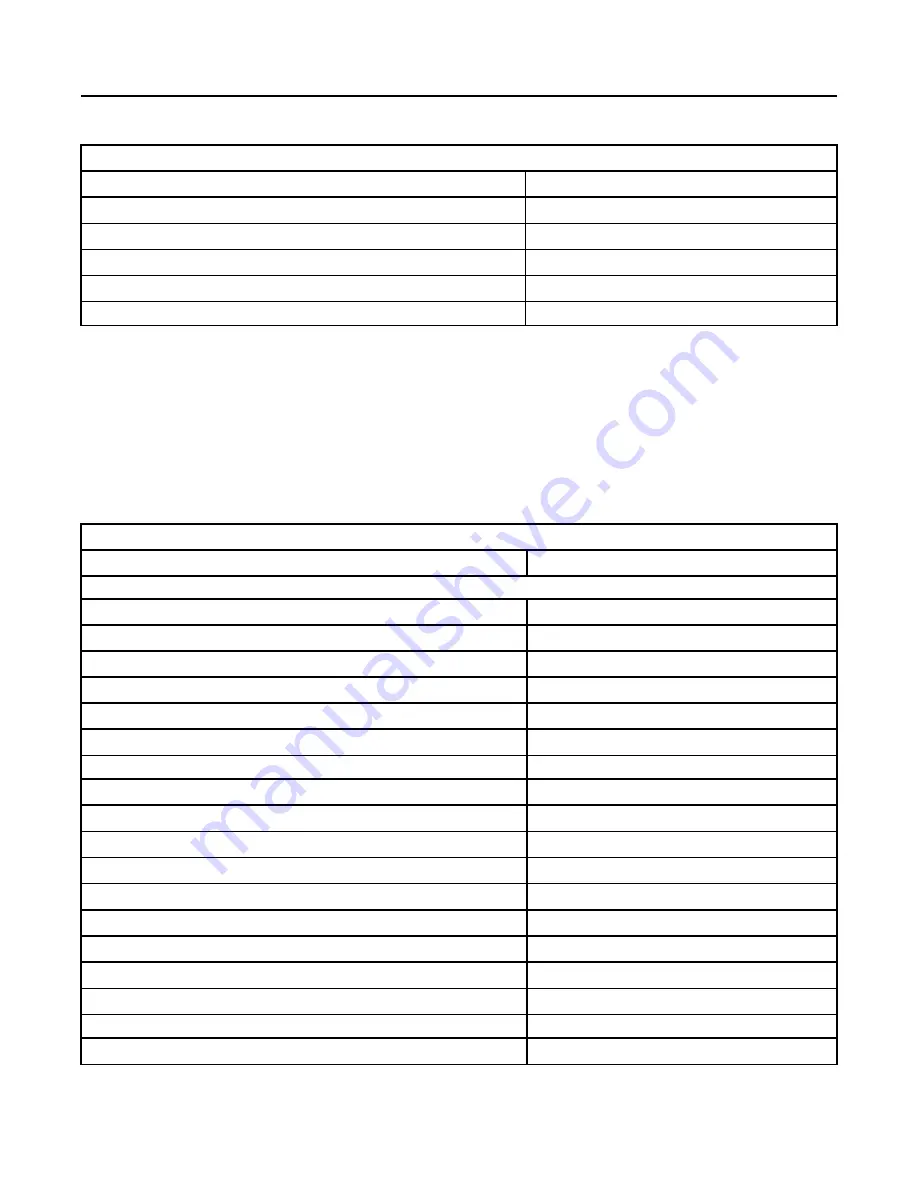
Table 2
System Configuration Parameters
Configuration Parameters
Record
Engine Serial Number
Rating
Full Load Setting
Full Torque Setting
ECM Software Release Date
Customer Specified Parameters
Customer specified parameters allow the engine to
be configured to the exact needs of the application.
The electronic service tool is required to alter the
customer configuration parameters.
Customer parameters may be changed repeatedly as
operational requirements change.
Table 3
Customer Specified Parameters
Specified Parameters
Record
Top Engine Limit
1900 rpm
Low Idle Speed
600 rpm
Top Engine Limit
2090 rpm
Engine Acceleration Rate
2000 rpm/s
Engine Speed Decelerating Ramp Rate
2000rpm/s
Ether Start Aid Configuration
Not Installed
Crankcase Pressure Sensor Installation Status
Not Installed
Ambient Air Temperature Sensor Installation Status
Not Installed
Engine Idle Shutdown Enable Status
Disabled
Engine Idle Shutdown Delay Time
5.0 min
Engine Idle Shutdown Ambient Temperature Override Enable Status
Disabled or Not Installed
Delayed Engine Shutdown Enable Status
Disabled
Delayed Engine Shutdown Maximum Time
7.0 min
Engine Performance Run Out Control Configuration
Not Installed
Engine Governor Mode Override Switch Installation Status
Not Installed
Transmission Default Torque Limit Reset
Not Reset
Air Filter Restriction Switch Installation Status
Not Installed
Air Filter Restriction Switch Configuration
Normally Open
(continued)
36
M0109073