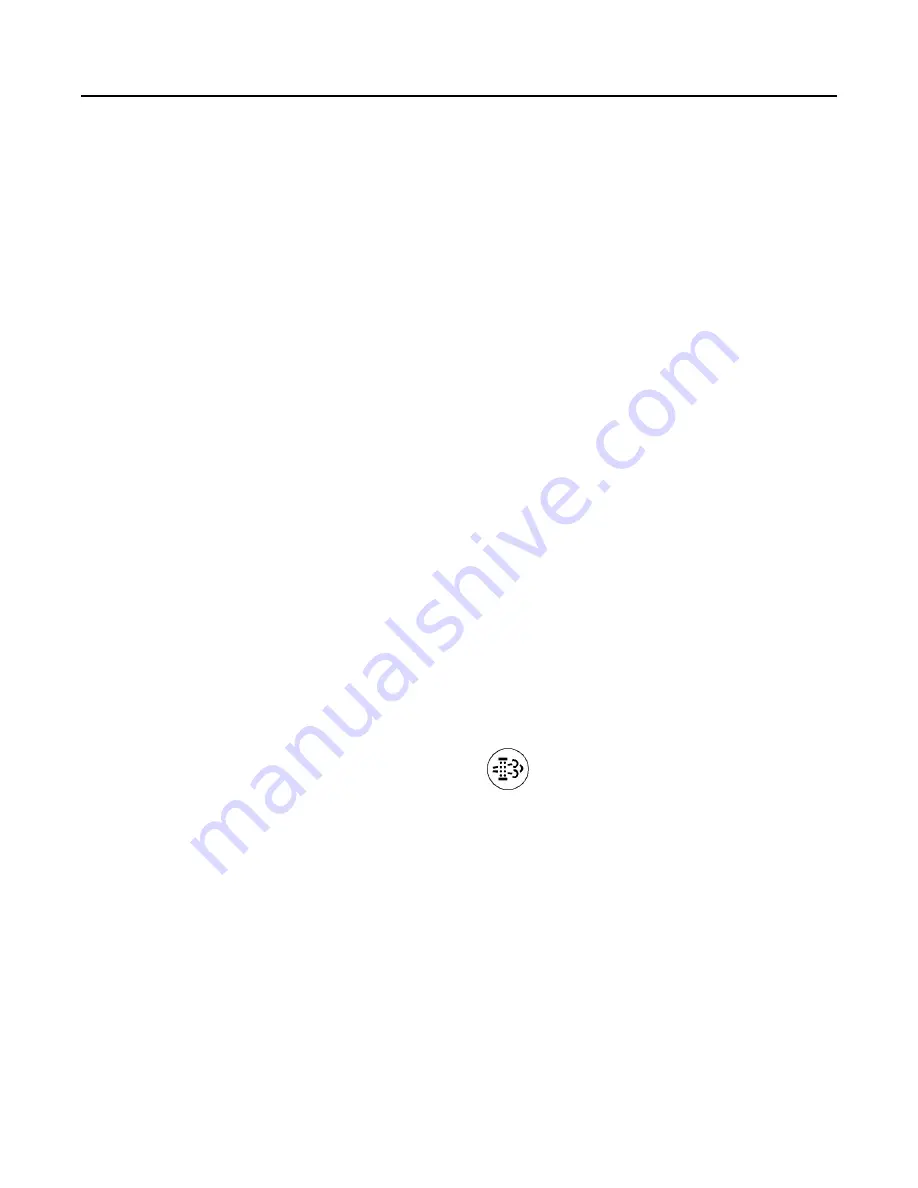
Engine Operation
i07290374
Engine
Operation
Proper
operation
and
maintenance
are
key
factors
in
obtaining
the
maximum
life
and
economy
of
the
engine.
If
the
directions
in
the
Operation
and
Maintenance
Manual
are
followed,
costs
can
be
minimized
and
engine
service
life
can
be
maximized.
The
time
that
is
needed
for
the
engine
to
reach
normal
operating
temperature
can
be
less
than
the
time
needed
for
a
walk-around
inspection
of
the
engine.
After
the
engine
is
started
and
after
the
engine
reaches
normal
operating
temperature,
the
engine
can
be
operated
at
the
rated
rpm.
The
engine
will
reach
normal
operating
temperature
faster
when
the
engine
is
at
rated
speed.
The
engine
will
reach
normal
operating
temperature
faster
when
the
engine
is
at
low-power
demand.
This
procedure
is
more
effective
than
idling
the
engine
at
no
load.
The
engine
should
reach
operating
temperature
in
a
few
minutes.
Gauge
readings
should
be
observed
and
the
data
should
be
recorded
frequently
while
the
engine
is
operating.
Comparing
the
data
over
time
will
help
to
determine
normal
readings
for
each
gauge.
Comparing
data
over
time
will
also
help
detect
abnormal
operating
developments.
Significant
changes
in
the
readings
should
be
investigated.
Engines
rated
for
constant
speed
use
are
allowed
to
complete
a
starting
sequence,
an
operation
at
a
single
constant
speed,
and
a
shutdown
sequence.
Every
time
the
engine
is
run,
each
of
these
operations
should
occur
only
once.
The
starting
sequence
and
shutdown
sequence
can
include
a
short
period
of
operation
at
the
low
idle
speed
for
purposes
of
warming
up
and
cooling
down
the
engine
or
driven
equipment.
The
emissions
type
approval
is
not
valid
for
operation
of
a
constant
speed
engine
in
a
manner
different
from
that
described
above.
Emissions
regulations
require
that
the
value
of
the
carbon
dioxide
(CO
2
)
emissions
be
reported
to
the
end
user.
For
this
engine,
696
g/kWh
was
determined
to
be
the
CO
2
value
determined
during
the
EU
type-
approval
process
and
recorded
in
EU
type-approval
certificate.
This
CO
2
measurement
results
from
testing
over
a
fixed
test
cycle
under
laboratory
conditions
a
(parent)
engine
representative
of
the
engine
type
(engine
family)
and
shall
not
imply
or
express
any
guarantee
of
the
performance
of
a
particular
engine.
i08769092
Diesel
Particulate
Filter
Regeneration
Regeneration
Regeneration
is
the
process
of
increasing
exhaust
temperatures
to
remove
soot
from
the
DPF.
Regeneration
also
reduces
hydrocarbons
across
the
DOC
and
the
DPF,
reduce
sulfur
from
SCR,
and
remove
DEF
deposits
from
the
DEF
injector.
The
DPF
traps
both
soot
and
ash.
The
ash
is
removed
through
a
manual
cleaning
process.
Refer
to
Operation
and
Maintenance
Manual,
Diesel
Particulate
Filter
-
Clean
for
more
information
on
the
service
of
the
DPF.
The
Electronic
Control
Module
(ECM)
uses
multiple
inputs
from
the
engine
and
the
machine
to
determine
the
best
time
for
regeneration
to
be
performed.
Regenerations
take
place
throughout
the
operating
cycle
of
the
engine
automatically.
Automatic
adjustments
of
engine
speed
may
be
noticed
during
regenerations.
If
regeneration
is
taking
place
and
the
engine
is
taken
to
low
idle,
the
engine
speed
may
remain
elevated
to
maintain
the
regeneration.
Under
certain
operating
conditions,
the
regeneration
may
be
stopped.
The
ECM
will
continue
to
monitor
inputs
to
determine
the
best
time
to
restart
the
regeneration.
If
needed,
the
operator
will
be
notified
via
display
that
action
is
required
to
allow
regeneration.
DPF – This indicator will illuminate to
show that regeneration is required.
Regeneration Triggers
Regeneration may be required for the following
reasons:
Soot:
The DPF will collect soot produced by the
engine. Automatic regeneration will become active to
reduce soot level.
Sulfation Regeneration:
The SCR will have sulfur
build up over time. The ECM will calculate sulfur
buildup and once accumulation hits a threshold, will
trigger regeneration to reduce sulfur.
M0087475-06
61