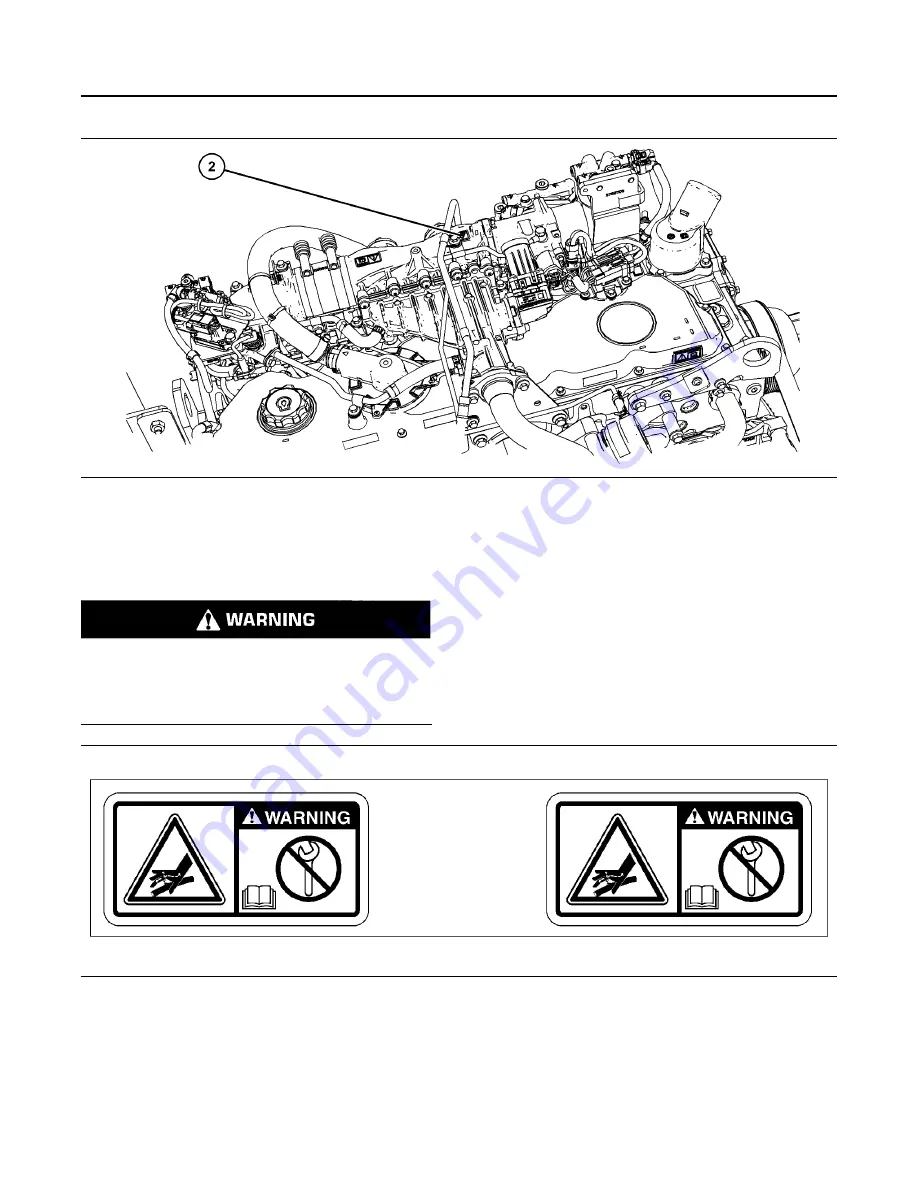
Illustration 4
g06276057
The ether warning label is installed on the intake
manifold, refer to illustration 4 .
Hand (High Pressure) 3
Contact with high pressure fuel may cause fluid
penetration and burn hazards. High pressure fuel
spray may cause a fire hazard. Failure to follow
these inspection, maintenance and service in-
structions may cause personal injury or death.
Illustration 5
g02382677
Typical example
8
M0090743