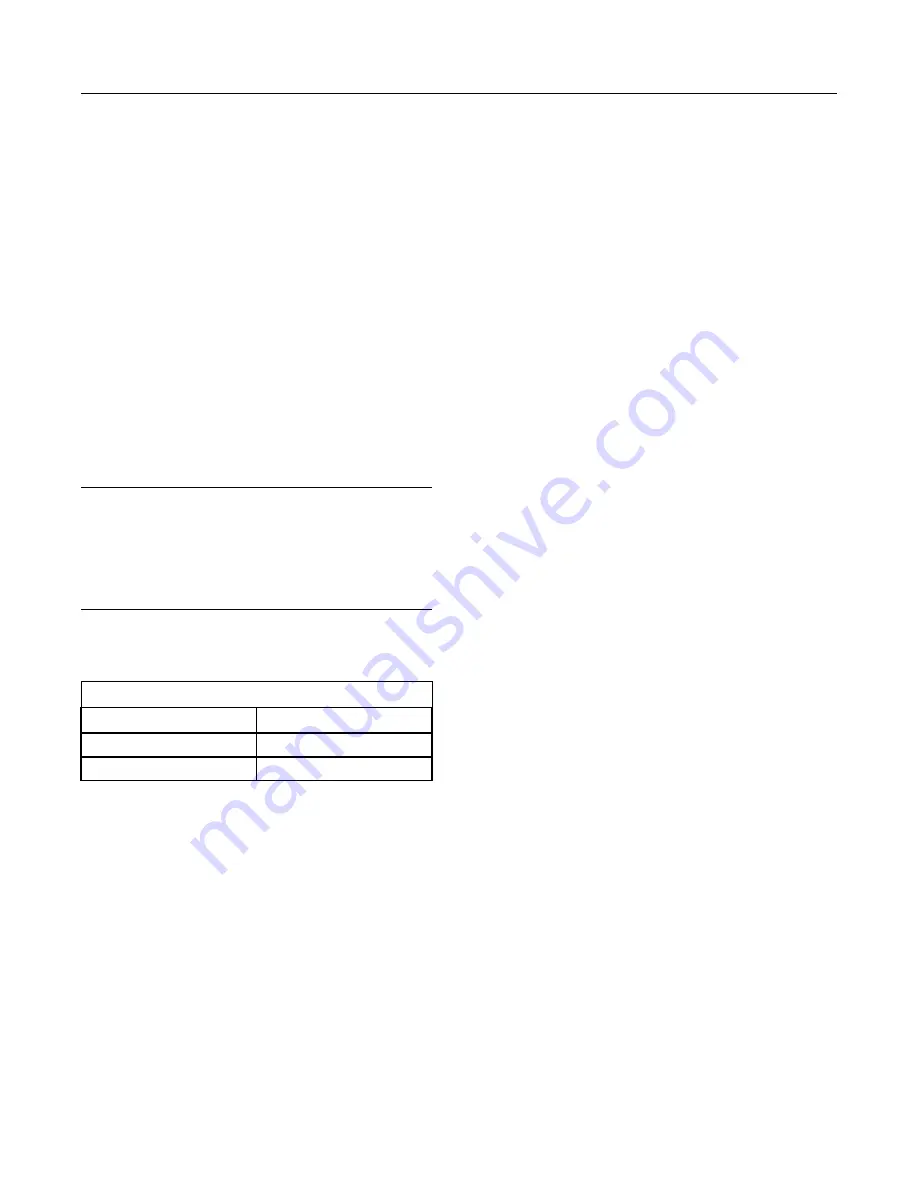
(Table 13, contd)
(3)
The level of sulfur is governed by emissions legislations, national, regional, or local regulations can require a fuel with a specific sulfur limit.
The sulfur content of the fuel and the fuel quality must comply with all existing local regulations for emissions. LSD fuel with less than 0.035
percent (≤ 350 ppm (mg/kg)) sulfur is strongly recommended for use in these engine models. Diesel fuel with more than 0.035 percent (≥ 350
ppm (mg/kg)) sulfur can be used only where allowed by legislation. Fuel sulfur levels affect exhaust emissions. High sulfur fuels also increase
the potential for corrosion of internal components. Fuel sulfur levels above 0.035% may significantly shorten the oil change interval. For addi-
tional information, refer to Operation and Maintenance Manual, “Fluid Recommendations (Lubricant Information)”.
(4)
The values of the fuel viscosity are the values as the fuel is delivered to the fuel injection pumps. Fuel should also meet the minimum viscos-
ity requirement and the fuel should meet the maximum viscosity requirements at 40° C (104° F) of either the “ASTM D445” test method,
“ISO 3104” test method or the “GB/T 265” test method. If a fuel with a low viscosity is used, cooling of the fuel may be required to maintain
2.0 cSt or greater viscosity at the fuel injection pump. Fuels with a high viscosity might require fuel heaters to lower the viscosity to 4.5 cSt at
the fuel injection pump.
(5)
Follow the test conditions and procedures for gasoline (motor).
(6)
The lubricity of a fuel is a concern with low sulfur and ultra low sulfur fuel. To determine the lubricity of the fuel, use the “ISO 12156-1” or
“ASTM D6079” High Frequency Reciprocating Rig (HFRR) test. If the lubricity of a fuel does not meet the minimum requirements, consult
your fuel supplier. Do not treat the fuel without consulting the fuel supplier. Some additives are not compatible. These additives can cause
problems in the fuel system.
(7)
Recommended cleanliness level for fuel as dispensed into machine or engine fuel tank is “ISO 18/16/13” or cleaner as per “ISO 4406”. Refer
to the "Contamination Control Recommendations for Fuels" in this chapter.
Note:
The owner and the operator of the engine has
the responsibility of using the fuel that is prescribed
by the China’s Ministry of Environmental Protection
and other appropriate regulatory agencies.
NOTICE
Operating with fuels that do not meet the Perkins rec-
ommendations can cause the following effects: Start-
ing difficulty, poor combustion, deposits in the fuel
injectors, reduced service life of the fuel system, de-
posits in the combustion chamber and reduced serv-
ice life of the engine.
The specifications that are listed in table 14 , are
released as acceptable to use
Table 14
Acceptable Fuel Specification for 1100AA Genset Engines
Fuel Specification
Description
“GB 19147”
Automobile diesel fuel
“GB 252”
General diesel fuels
Diesel Fuel Characteristics
Cetane Number
Cetane number is a measure of the ignition quality of
diesel fuel. Fuel that has a higher cetane number will
give a shorter ignition delay and will produce a better
ignition quality. Cetane numbers are derived for fuels
against proportions of cetane and
heptamethylnonane in the standard CFR engine.
Refer to “ISO 5165” for the test method.
For these engines minimum recommended cetane
number 45. Cetane number affect engine cold start
ability, exhaust emissions, combustion noise, and
altitude performance. Fuel with higher cetane
number is desirable and recommended. Fuel with
higher cetane number is of particular importance for
operations in cold weather and at high altitude.
Viscosity
Viscosity is the property of a liquid of offering
resistance to shear or flow. Viscosity decreases with
increasing temperature. This decrease in viscosity
follows a logarithmic relationship for normal fossil
fuel. The common reference is to kinematic viscosity.
Kinematic viscosity is the quotient of the dynamic
viscosity that is divided by the density. The
determination of kinematic viscosity is normally by
readings from gravity flow viscometers at standard
temperatures. Refer to “ISO 3104” for the test
method.
The viscosity of the fuel is significant because fuel
serves as a lubricant for the fuel system components.
Fuel must have sufficient viscosity to lubricate the
fuel system in both extremely cold temperatures and
extremely hot temperatures. If the kinematic viscosity
of the fuel is lower than 2 cSt at the fuel injection
pump, damage to the fuel injection pump can occur.
This damage can be excessive scuffing and seizure.
Low viscosity may lead to difficult hot restarting,
stalling, and loss of performance. High viscosity may
result in seizure of the pump.
Perkins recommends kinematic viscosities of 2 and
4.5 mm
2
/s that is delivered to the fuel injection pump.
If a fuel with a low viscosity is used, cooling of the
fuel may be required to maintain 2 cSt or greater
viscosity at the fuel injection pump. Fuels with a high
viscosity might require fuel heaters to lower the
viscosity to 4.5 cSt at the fuel injection pump.
Density
Density is the mass of the fuel per unit volume at a
specific temperature. This parameter has a direct
influence on engine performance and a direct
influence on emissions. This influence determines
the heat output from a given injected volume of fuel.
This parameter is quoted in kg/m at 15 °C (59 °F).
Perkins recommends a value of density of 820 kg/m
to 845 kg/m to obtain the correct power output.
Lighter fuels are acceptable but these fuels will not
produce the rated power.
M0106585
43