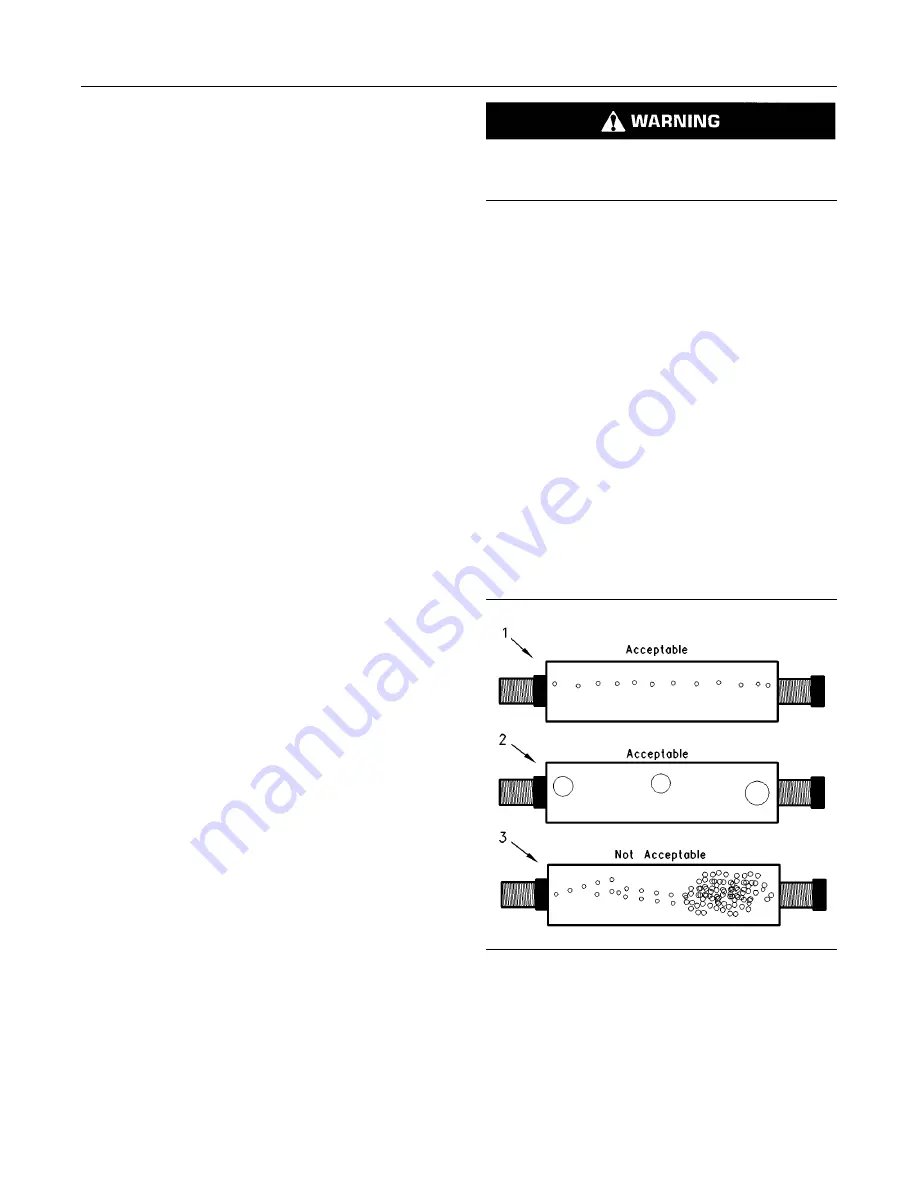
Testing And Adjusting
Section
Fuel System
i05182667
Fuel System - Inspect
Introduction
A problem with the components that send fuel to the
engine can cause low fuel pressure. This can
decrease engine performance. Use the following
procedure to inspect the fuel system.
Check Procedure
1.
Check the fuel level in the fuel tank. Ensure that
the vent in the fuel cap is not filled with dirt.
2.
Check all fuel lines for fuel leakage. The fuel lines
must be free from restrictions and faulty bends.
Verify that the fuel return line is not collapsed.
3.
Inspect the fuel filter for excess contamination. If
necessary, install a new fuel filter. Determine the
source of the contamination. Make the necessary
repairs.
4.
Service the primary fuel filter (if equipped).
5.
Remove any air that may be in the fuel system.
Refer to Testing and Adjusting, “Fuel System -
Prime”.
i02780600
Air
in
Fuel
-
Test
This procedure checks for air in the fuel system. This
procedure also assists in finding the source of the air.
1.
Examine the fuel system for leaks. Ensure that the
fuel line fittings are properly tightened. Check the
fuel level in the fuel tank. Air can enter the fuel
system on the suction side between the fuel
transfer pump and the fuel tank.
Work carefully around an engine that is running.
Engine parts that are hot, or parts that are mov-
ing, can cause personal injury.
2.
Install a suitable fuel flow tube with a visual sight
gauge in the fuel return line. When possible, install
the sight gauge in a straight section of the fuel line
that is at least 304.8 mm (12 inches) long. Do not
install the sight gauge near the following devices
that create turbulence:
• Elbows
• Relief valves
• Check valves
• Connections
Observe the fuel flow during engine cranking. Look
for air bubbles in the fuel. If there is no fuel that is
present in the sight gauge, prime the fuel system.
Refer to Testing and Adjusting, “Fuel System -
Prime” for more information. If the engine starts,
check for air in the fuel at varying engine speeds.
When possible, operate the engine under the
conditions which have been suspect.
Illustration 20
g00578151
(1) A steady stream of small bubbles with a diameter of
approximately 1.60 mm (0.063 inch) is an acceptable amount
of air in the fuel.
(2) Bubbles with a diameter of approximately 6.35 mm (0.250 inch)
are also acceptable if there is two seconds to three seconds
intervals between bubbles.
(3) Excessive air bubbles in the fuel are not acceptable.
22
UENR0617
This document has been printed from SPI2. NOT FOR RESALE.