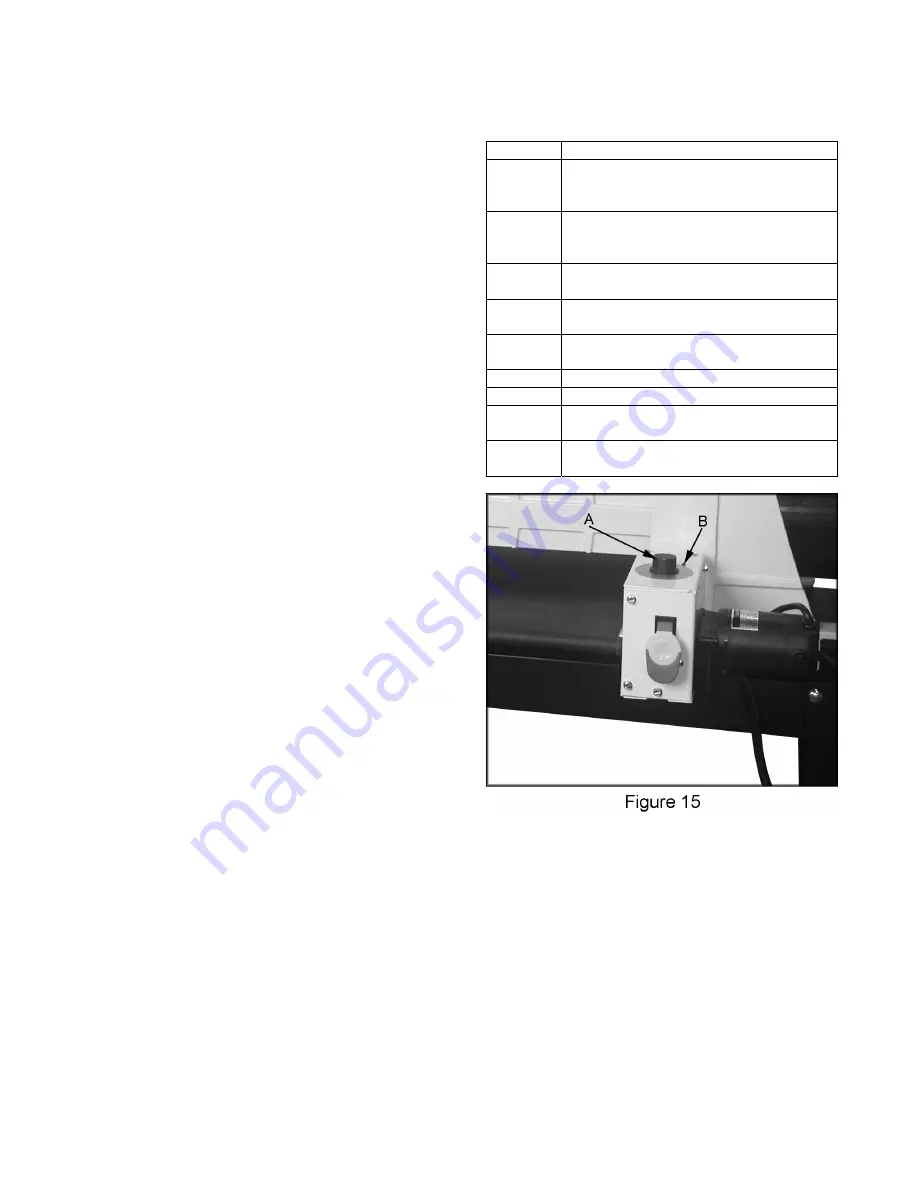
13
Selecting SANDSMART™ Feed Rates
Begin experimenting with the feed rate set at
about 40%-50% of maximum. The best feed
rate will depend on a number of factors,
including type of stock, grit and depth of cut
used, and whether the stock is feed directly in-
line with the conveyor bed or at an angle. If a
“ripple effect” or inconsistent finish is observed,
slow down the feed rate. If the finish is smooth
and consistent and the sander is not
overworking, experiment using a faster feed
rate.
The SandSmart control (A, Fig. 15) continuously
monitors the load on the drum motor, and
automatically regulates the speed of the
conveyor motor to maintain the highest feed rate
without overload. If the load on the drum motor
increases, the SandSmart control will decrease
the conveyor feed rate and will stop the
conveyor under extreme conditions. If the load
on the drum decreases, the SandSmart control
will increase the feed rate but will not increase it
faster than the manual setting on the switch dial.
The best and most consistent finish will be
achieved if the conveyor does not change speed
during operation. When the “red” indicator light
(B, Fig. 15) comes on, the SandSmart control
has detected too great a depth of cut and/or too
fast a feed rate. This change in conveyor speed
may affect the finish surface. If the finish is
affected, make another sanding pass without
changing any settings. If the finish is still
affected, make adjustments by slowing the
conveyor and/or decreasing the depth of cut and
run the stock through again.
Abrasives
The abrasive material you choose will have a
substantial effect on the performance of your
sander. Variations in paper type, weight,
coating, and durability all contribute to achieving
your desired finish. For the best sanding results,
Performax offers premium abrasives that have
been tested and certified for lowest overall cost
and maximum performance. Genuine
Performax abrasives are available in pre-cut
“Ready- to-Wrap” lengths or in the convenient
pre-marked “Ready-to-Cut” box.
Selecting Drum Abrasives
It is important to select the proper grit of
abrasives for the type of sanding being
performed to achieve maximum sanding results.
As with any sanding operation, first begin
sanding with coarser grit, depending on the
roughness of the stock, or the amount of stock
to be removed. Then progressively work toward
finer grits. The chart below shows the general
uses for the various grits. Performax offers strip
rolls in the eight different abrasive grits shown.
Grit Common
Application
24
Grit
Abrasive planing, surfacing rough-
sawn boards, maximum stock
removal, glue removal.
36
Grit Abrasive planing, surfacing rough
sawn boards, maximum stock
removal, glue removal.
50 Grit
60 Grit
Surfacing and dimensioning boards,
truing warped boards
80 Grit
Surfacing,
light
dimensioning,
removing planer ripples.
100 Grit
Light surfacing, removing light planer
ripples.
120 Grit
Light surfacing, minimal stock removal.
150 Grit
Finish sanding, minimal stock removal.
180
Grit Finish sanding only, not for stock
removal.
220
Grit Finish sanding only, not for stock
removal.
Summary of Contents for 649003K
Page 18: ...18 Drum Head Assembly...
Page 21: ...21 Conveyor And Motor Assembly...
Page 23: ...23 Wiring Diagram...