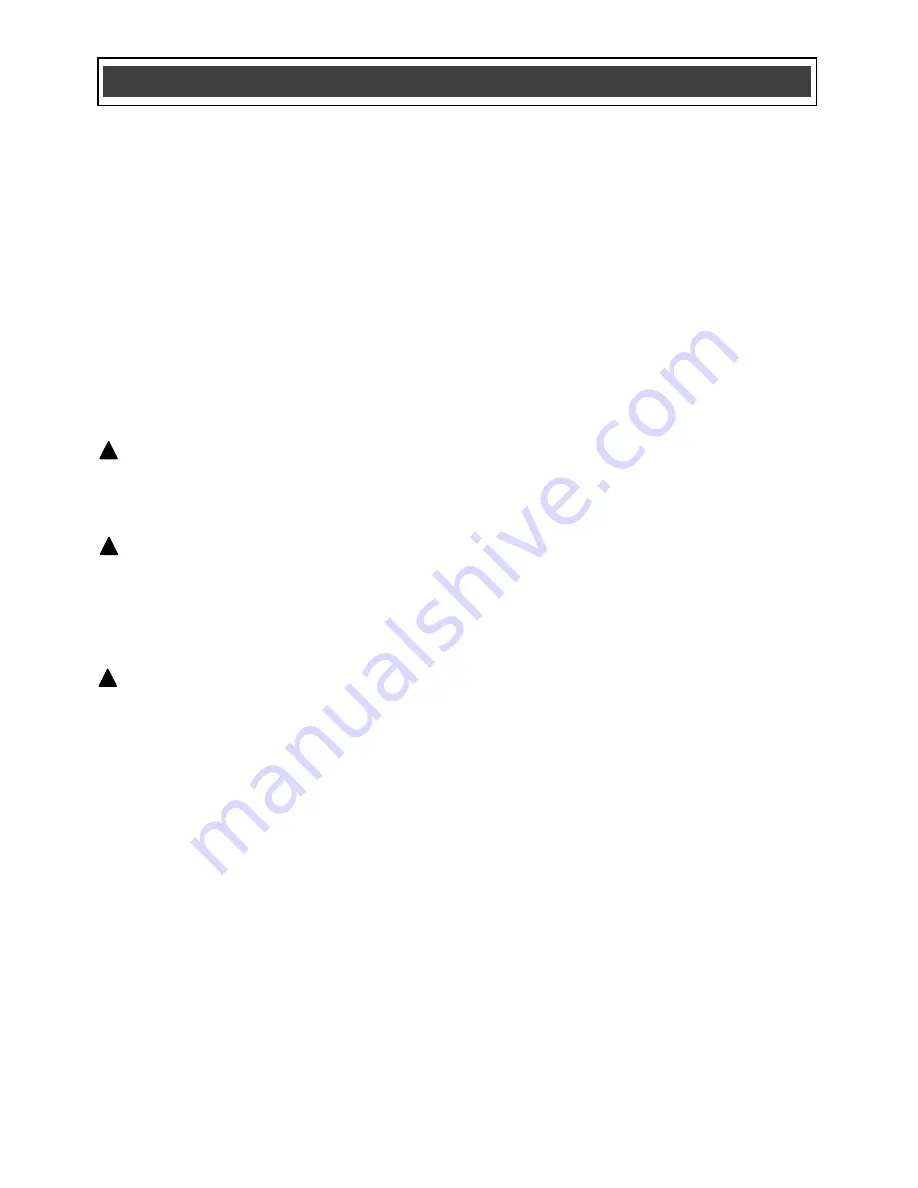
9
ADDITIONAL SPECIFIC SAFETY RULES –
cont’d
When replacing the blade, make sure the
replacement blade is 7 1/4" in diameter and
is rated for at least 5,400 RPM. Installing an
incorrect blade will result in possible injury and
poor cutting action.
After changing a blade or making
adjustments, make sure the blade clamp
screw is securely tightened. Loose blades
and adjustment devices will be violently thrown.
Never touch the blade during or immediately
after use. After use the blade is too hot to be
safely touched with bare hands.
DANGER:
Never use the laser in the
presence of small children. Small children may
stare directly into the laser light beam and cause
serious eye injury.
DANGER:
The laser light beam that is
projected from the front of the laser level can be
dangerous to eyesight. Never allow anyone to
stare directly into the light. Staring directly into
the light beam may result in serious eye
damage.
DANGER
: Always remove the battery when
changing the blade.
SPECIFIC SAFETY RULES
!
!
!
SAVE THESE INSTRUCTIONS FOR REFERENCE
Summary of Contents for 241-0985
Page 18: ...18 EXPLODED VIEW ...