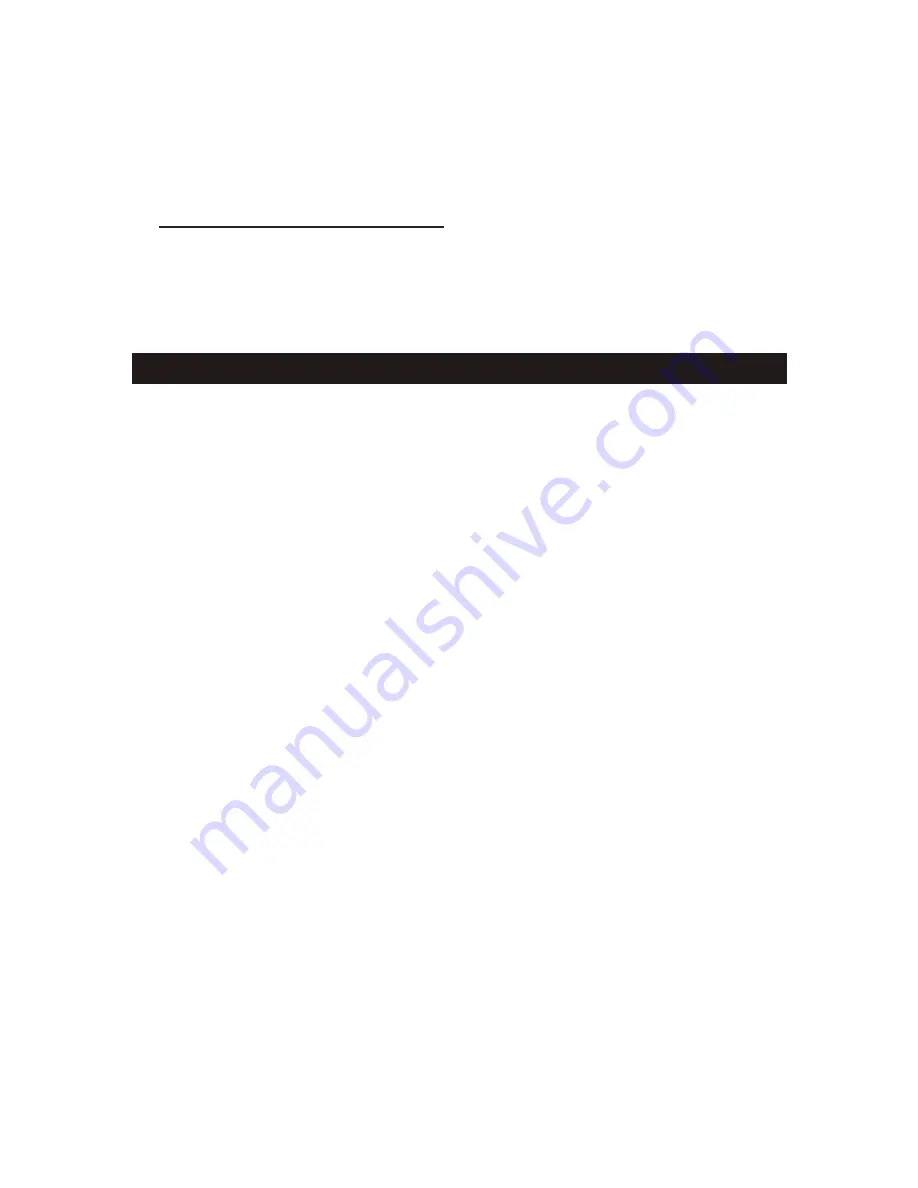
11
TROUBLESHOOTING GUIDE
1.
2.
3.
4.
Before each use
, inspect the general condition of the Inverter Arc Welder. Check
for damaged electrical wiring, loose connections, cracked, burnt, or broken parts,
and any other condition that may affect its safe operation. If abnormal noise or
vibration occurs, have the problem corrected before further use.
Do not use damaged equipment.
Before each use,
clean or, if necessary, replace the electrode.
To clean,
use a shop vacuum cleaner, or use compressed air.
When storing, make sure to store the Inverter Arc Welder in a safe, clean, and
dry location.
The Inverter Arc Welder will not
1.
turn on.
Make sure the power cord is
a.
plugged in.
Make sure the quick plugs are
b.
properly plugged into the quick connectors.
The Inverter Arc Welder is turned
2.
on, but will not strike an arc.
Make sure the electrode is securely
a.
attached to the electrode holder.
Make sure the quick plugs are
b.
properly plugged into the quick connectors.
Make sure the ground clamp is
c.
securely attached to the work piece or metal
table on which the work piece is placed, and that the point of attachment is
clean from rust, paint, or any other material that would insulate the connection.
The Inverter Arc Welder is not
3.
working, and the overload protection light is on.
When the Inverter Arc Welder over
a.
heats it will automatically shut down
temporarily. When this happens
it cools down. As soon as the overload protection light goes off you may
continue welding.
If the welder does not cool down
b.
as described above, check to see if the
fan is operating. If the fan is operating, check the side panel vents to see if
anything is obstructing airflow from the fan. If obstructions exist, remove
them and wait for the welder to cool while observing the overload protection
The current output is unstable and
4.
unable to produce a smooth welding bead.
Make sure the power cord is
a.
light.
properly connected to its electrical outlet.
Make sure the quick plugs are
b.
securely connected to the quick connectors.
Make sure the ground clamp is
c.
securely attached to the work piece or metal
table on which the work piece is placed, and that the point of attachment is
clean from rust, paint, or any other material that would insulate the connection.
stop welding, but leave the welder on until