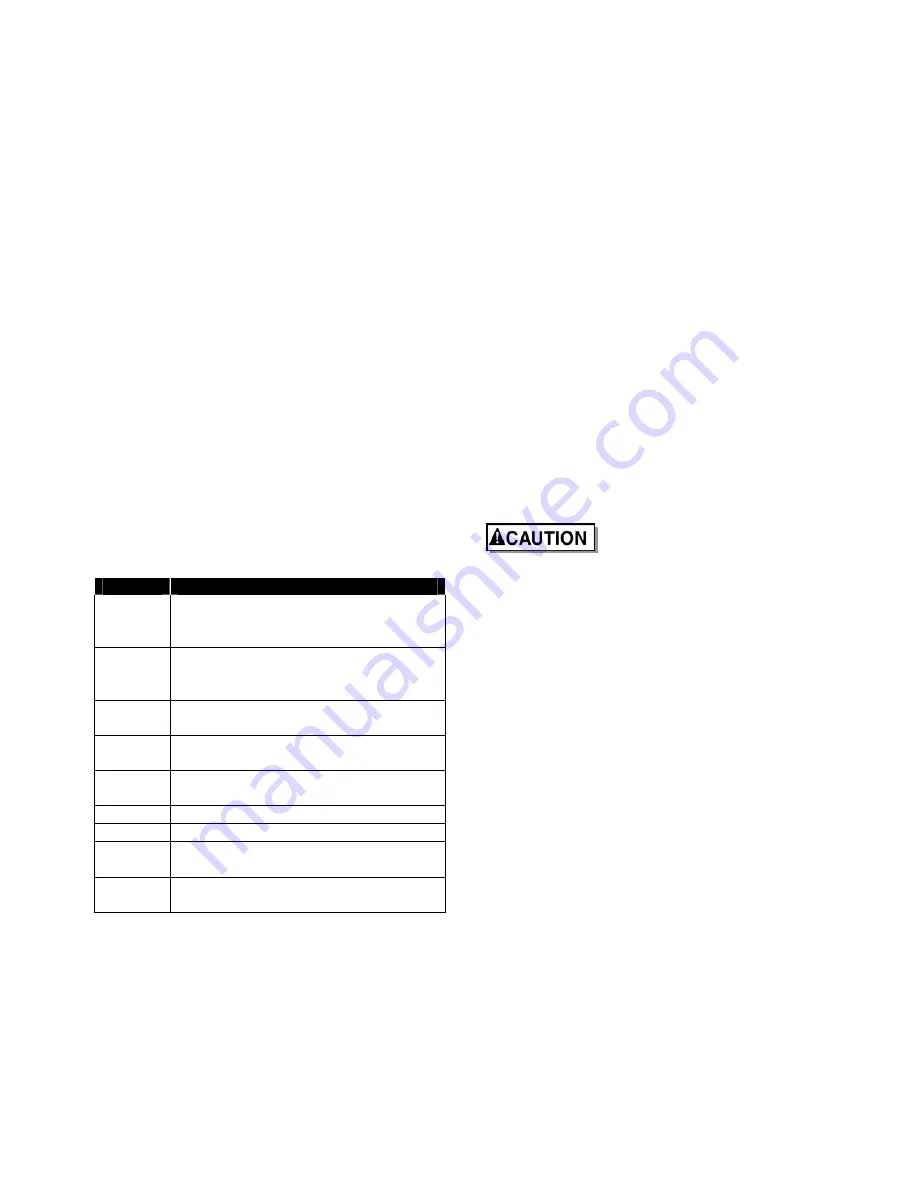
16
Abrasives
The abrasive material you choose will have a
substantial effect on the performance of your
sander. Variations in paper type, weight, coating
and durability all contribute to achieving your
desired finish. For the best sanding results,
Performax offers premium abrasives that have
been tested and certified for lowest overall cost
and maximum performance. Genuine Performax
abrasives are available in pre-cut “Ready- to-
Wrap” lengths or in the convenient pre-marked
“Ready-to-Cut” box.
Selecting Drum Abrasives
To achieve maximum sanding results, it is
important to select the proper grit of abrasive for
the type of sanding being performed. As with
any sanding operation, first begin sanding with a
coarser grit, depending on the roughness of the
stock, or the amount of stock to be removed.
Then progressively work toward finer grits. The
chart below shows the general uses for the
various grits. Performax offers strip rolls in the
nine different abrasive grits shown.
Selecting Abrasive Grits
The amount of stock to be removed is a major
consideration when choosing the grit grade to
start with. Grits of 24, 36, 50, 60 and 80 are
primarily designed for stock removal. Grits of 24
and 36 will remove the most material in one
pass, whether you are doing abrasive planing,
cleaning up glued panels or flattening stock.
Grits from 100 through 220 are primarily
finishing grits designed to remove the scratch
pattern from the previous grit used. For best
results, never skip more than one grit grade
when progressing through a sanding sequence.
For fine work, such as furniture, try not to skip
any grit grades during the sanding process. In
general, premium quality abrasives such as
genuine Performax abrasives will produce a
better finish with a less noticeable scratch
pattern.
Note:
Grits that are too fine can
sometimes burnish the wood and leave a glossy
surface that will not accept stains evenly. This
will vary by the type of wood. Oak, for example,
is susceptible to burnishing because of its open
pores.
Cleaning Abrasive Strips
A sandpaper cleaning stick may be used to
remove deposits and help extend sandpaper life.
To use, operate the sanding drum with the dust
cover open.
For your own safety, always
wear eye protection while
performing sandpaper
cleaning, and take all
precautions to avoid any
contact of hands or clothing
with uncovered drums. Hold
the cleaning stick against the
rotating drum and move it
along the drum surface. It is a
good idea to use a shop brush
or air nozzle to remove any
cleaning stick crumbs from
the drums before resuming
sanding operations.
Cloth-backed abrasives can be cleaned by
soaking in paint thinner or mineral spirits for 20
minutes to one hour. Then use a nylon brush to
remove any buildup.
Stretching Abrasive Life
Abrasive life can also be increased by removing
the abrasive strip from the drum and reversing it.
To do this, remove the strip and use what was
the trailing end as the starting end on the left
(outboard) side of the drum. Reversing the strip
will provide a fresh set of cutting edges on the
drum.
Grit
Common Application
24 Grit
Abrasive planing, surfacing rough-
sawn boards, maximum stock
removal, glue removal.
36 Grit
Abrasive planing, surfacing rough
sawn boards, maximum stock
removal, glue removal.
60 Grit
Surfacing and dimensioning boards,
truing warped boards
80 Grit
Surfacing, light dimensioning,
removing planer ripples.
100 Grit
Light surfacing, removing light planer
ripples.
120 Grit
Light surfacing, minimal stock removal.
150 Grit
Finish sanding, minimal stock removal.
180 Grit
Finish sanding only, not for stock
removal.
220 Grit
Finish sanding only, not for stock
removal.
Summary of Contents for 10-20 PLUS
Page 10: ...10 This Page Intentionally Left Blank...
Page 20: ...20 Exploded View 10 20 PLUS Sander...
Page 23: ...23 Wiring Diagram...