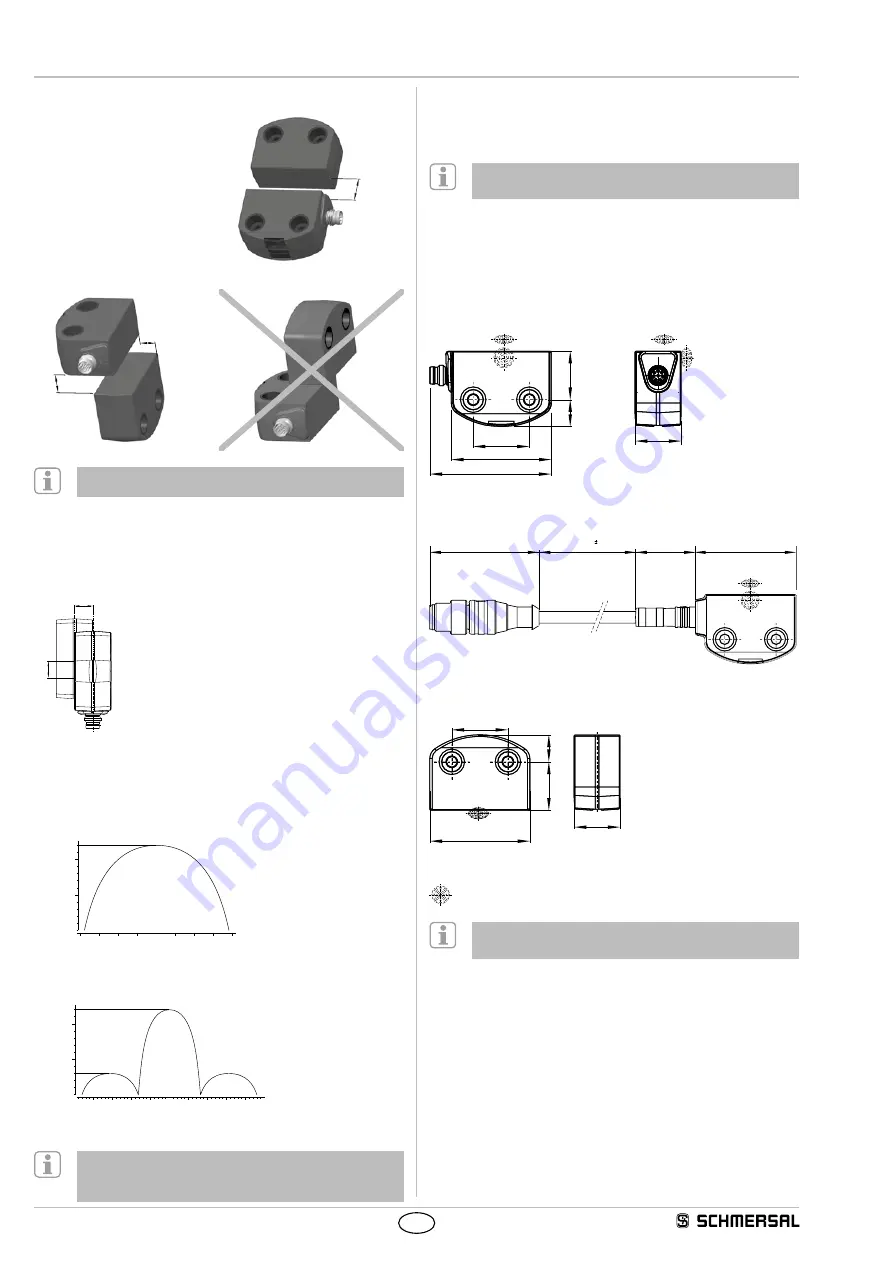
4
Operating instructions
Safety sensor
RSS260 AS
EN
3.2 Actuating directions
Actuation from front
12
Actuation from side
9
7
Lateral actuation only from the shown sensor side
3.3 Switching distance
The side allows for a maximum height misalignment (X) of sensor
and actuator of ± 8 mm (e.g. mounting tolerance or due to guard door
sagging). The axial misalignment (Y) is max. ± 18 mm.
Y
X
Actuating curves
The actuating curves represent the typical switching distance of
the safety sensor during the approach of the actuator subject to the
actuating direction
Transverse misalignment
-5
-20
5
10 15
-15
20
-10
0
Y [mm]
S [mm]
0
5
10
12
Height misalignment
-5
-20
-24
5
10 15
-15
20 24
-10
0
X [mm]
S [mm]
0
5
10
12
Preferred actuation directions: from front or from side
In case of a lateral actuation, the switching distances are
reduced by approx. 3 mm.
3.4 Adjustment
The continuous signal of the yellow LED signals the actuator detection; the
flashing of the yellow LED after a delay signals that the safety sensor is
actuated in the hysteresis area.
Recommended Adjustment
Align the safety sensor and actuator at a distance of 0.5 x s
ao
.
The correct functionality of both safety channels must be checked by
means of the connected safety-monitoring module.
3.5 Dimensions
All measurements in mm.
Safety sensor RSS260-…-ST-AS
19
10
.5
22
39.2
47.5
18
M4
Safety sensor RSS260-...-LSTM12-AS
43
25
47
250
10
Actuator RST260-1 / RST260-1-AD01 … 15
19
10.5
39
22
18
M4
Legend:
active area
Alternative suitable actuators with different design:
refer to products.schmersal.com.
3.6 Accessories
(to be ordered separately)
Kit tamper-proof screws
• 4 x M4x20 incl. washers, ordering code 103006158
• 4 x M4x25 incl. washers, ordering code 101217746
Sealing kit
• Ordering code
103004733
• Plugs: 4 flat pieces for flush finish and 4 round pieces for high screw
heads to seal the installation holes
• Flush one-way plugs for flat screw heads, also suitable as tampering
protection for the screw fixings