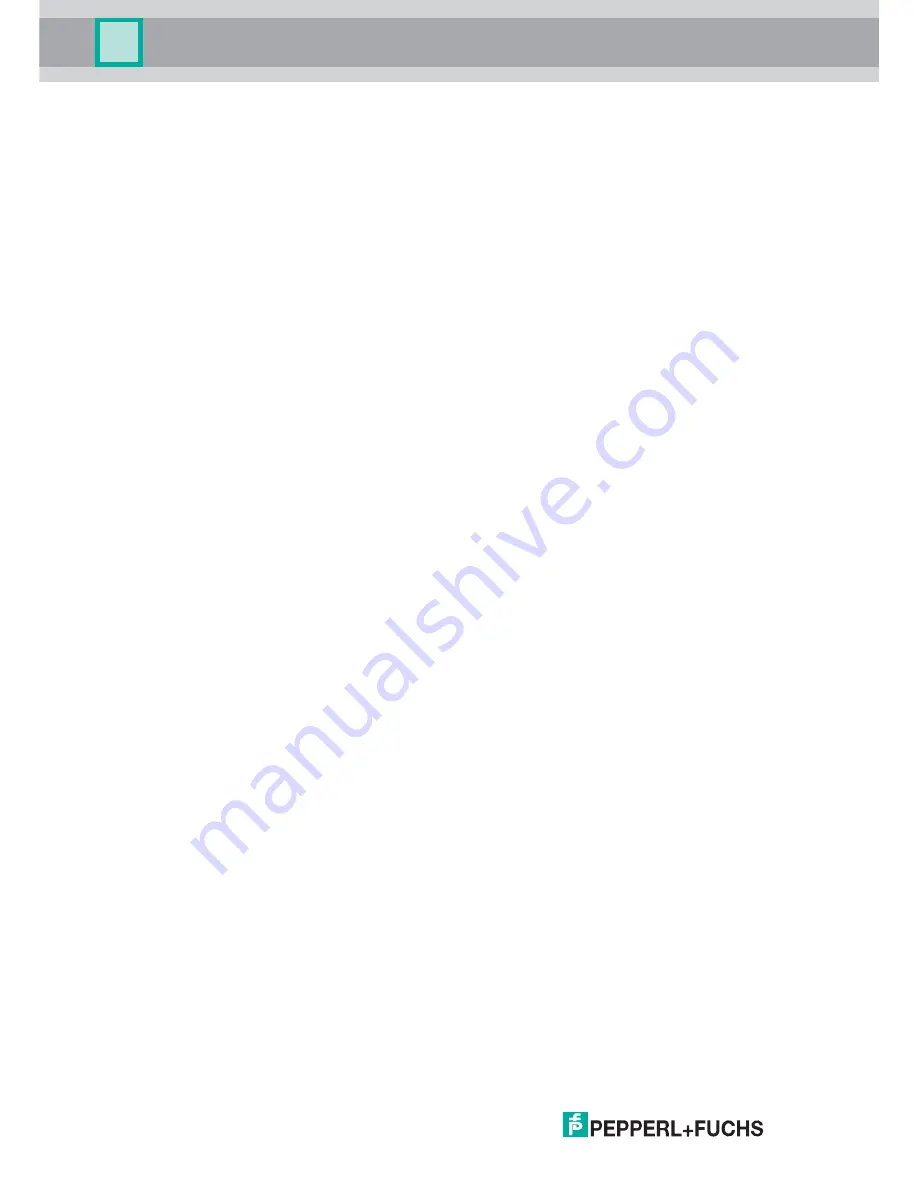
2
018-
06
10
Functional Safety KFD2-RSH-1.2D.FL2, KFD2-RSH-1.2D.FL3
Planning
3.2
Assumptions
The following assumptions have been made during the FMEDA:
•
Failure rates are constant, wear is not considered.
•
Failure rate based on the Siemens standard SN29500.
•
The safety-related device is considered to be of type
A
device with a hardware fault
tolerance of
0
.
•
The device will be used under average industrial ambient conditions comparable to the
classification "stationary mounted" according to MIL-HDBK-217F.
Alternatively, operating stress conditions typical of an industrial field environment similar to
IEC/EN 60654-1 Class C with an average temperature over a long period of time of 40
º
C
may be assumed. For a higher average temperature of 60
º
C, the failure rates must be
multiplied by a factor of 2.5 based on experience. A similar factor must be used if frequent
temperature fluctuations are expected.The nominal voltage at the digital input is 24 V.
Ensure that the nominal voltage do not exceed 26.4 V under all operating conditions.
•
The DO card must be able to supply a signal current of at least 100 mA.
•
Observe for the high demand mode the useful lifetime limitations of the output relays.
•
The relay contacts must be protected against overcurrent with a suitable current limitation.
For this purpose, either the internal fuse or an external current limitation with the same limit
values must be used.
SIL 3 application
•
The device shall claim less than 10 % of the total failure rate for a SIL 3 safety loop.
•
For a SIL 3 application operating in low demand mode the total PFD
avg
value of the
SIF (
S
afety
I
nstrumented
F
unction) should be smaller than 10
-3
, hence the maximum
allowable PFD
avg
value would then be 10
-4
.
•
For a SIL 3 application operating in high demand mode the total PFH value of the
SIF should be smaller than 10
-7
per hour, hence the maximum allowable PFH value would
then be 10
-8
per hour.
•
Since the safety loop has a hardware fault tolerance of
0
and it is a type
A
device, the
SFF must be > 90 % according to table 2 of IEC/EN 61508-2 for a SIL 3 (sub) system.
SILCL and PL application
•
The device was qualified for use in safety functions acc. to IEC/EN 62061 and
EN/ISO 13849-1. The device fulfils the requirements for a SILCL of SIL 3 acc. to
IEC/EN 62061 and due to the equivalency between these standards PL e acc. to
EN/ISO 13849-1.