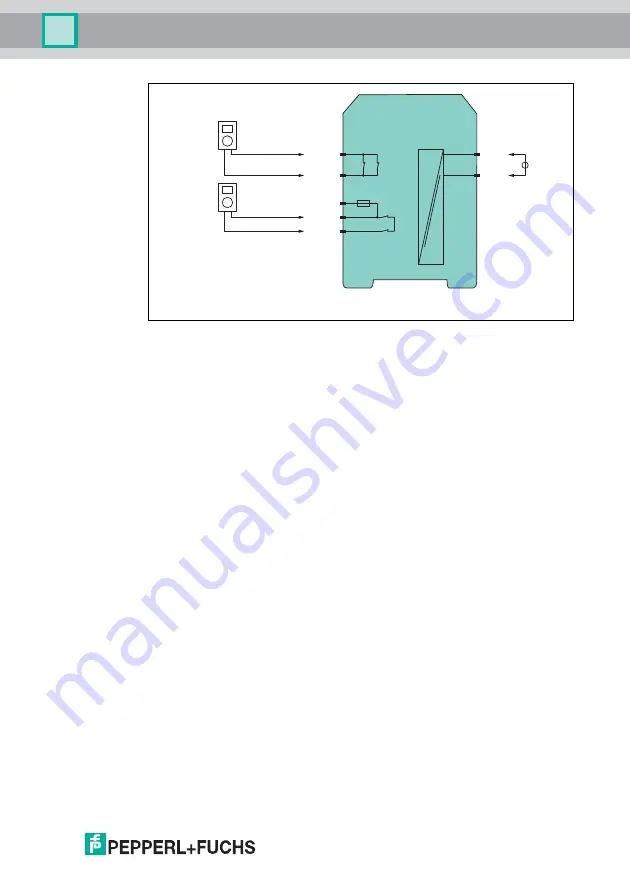
SAFETY MANUAL SIL KFD0-RSH-1.4S.PS2
Proof Test
22
5538
201
1-
04
15
Figure 4.5
Proof test set-up for KFD0-RSH-1.4S.PS2, test 5
Only if all tests are successfully done, the proof test is successfull.
7
4
5
6
2
3
8(+/-)
24 V
Multimeter
(
Ω
)
Multimeter
(
Ω
)