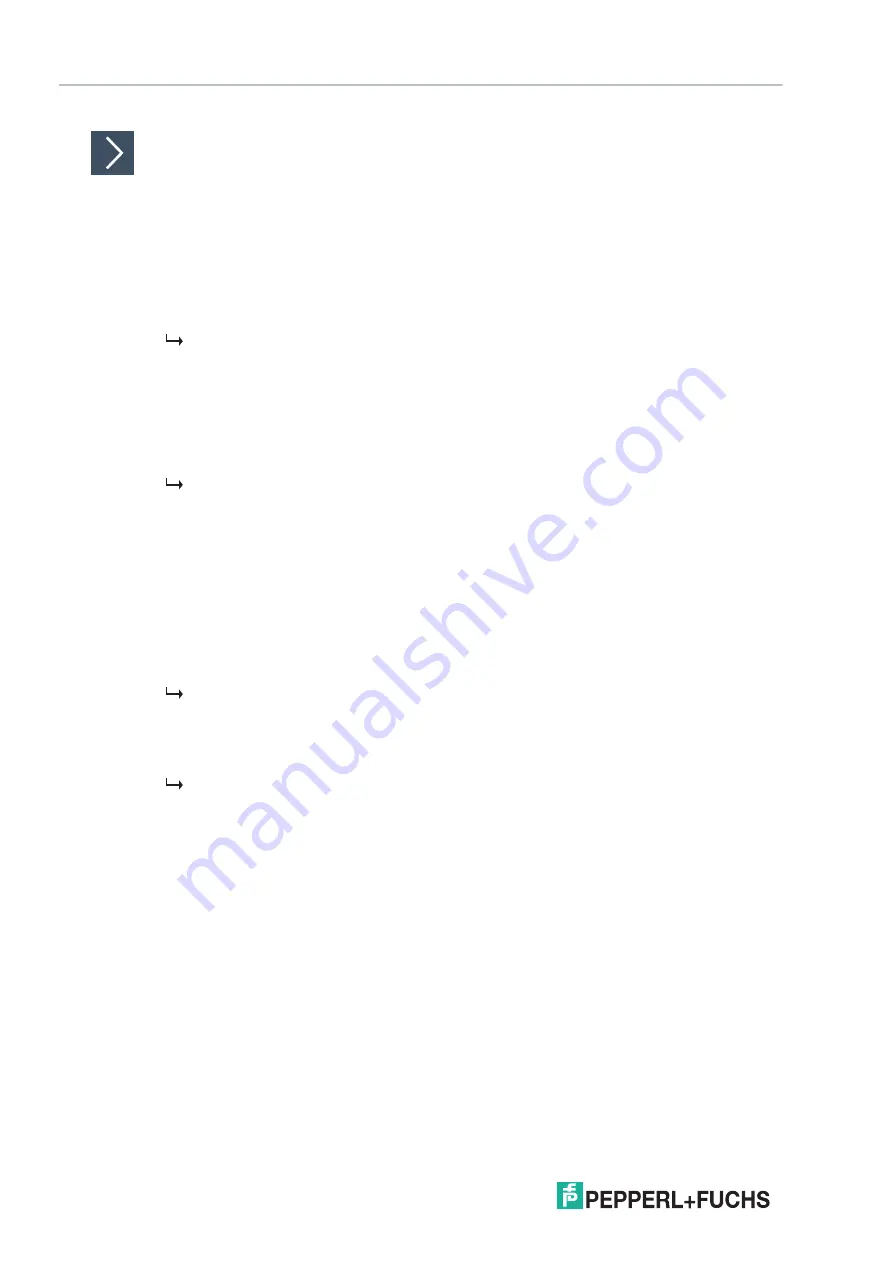
2
02
1-
10
18
Functional Safety HiD282*, HiD284*
Operation
Proof Test Procedure
1.
Put out of service the entire safety loop. Protect the application by means of other measures.
2.
Prepare a test set-up, see figures below.
3.
Simulate the sensor state by connecting a potentiometer, a resistor for short circuit detection
or by a resistor for lead breakage detection.
Test each input channel individually.
4.
Connect a potentiometer of 4.7 k
(threshold for normal operation) to the input.
The threshold must be between 1.4 mA and 1.9 mA, the hysteresis must
be between 170
µ
A and 250
µ
A.
• If the input current is above the threshold the relay must be activated for normal mode
of operation. The yellow LED lights up.
• If the input current is below the threshold the relay must be activated for inverted mode
of operation. The yellow LED lights up.
5.
Connect a resistor R
SC
(220
) or a resistor R
LB
(150 k
) to the input.
The device must detect an external fault. This state is indicated by red LED and the relay
of the corresponding output must be de-activated. The yellow LED is off.
6.
For HiD282* devices
Connect a load of 240
/2.5 W to the output.
For HiD284* devices
Connect a load of 2.4 k
to the output.
7.
For HiD282* devices
Test all relay outputs with a specific current, e. g. 100 mA. To avoid electric shock,
use a test voltage of 24 V DC. Check that the relay contacts are open.
The relays must be de-activated. The relay contacts must
definitely open
.
For HiD284* devices
Test all transistor outputs with a specific current, e. g. 10 mA. To avoid electric shock,
use a test voltage of 24 V DC. Check that the transistors are not conducting.
The transistors must be de-activated. The transistor outputs must
definitely not
conducting
.
8.
After the test, reset the device to the original settings.
9.
Check the correct behavior of the safety loop. Is the configuration correct?
10.
Secure the DIP switches to prevent unintentional adjustments.