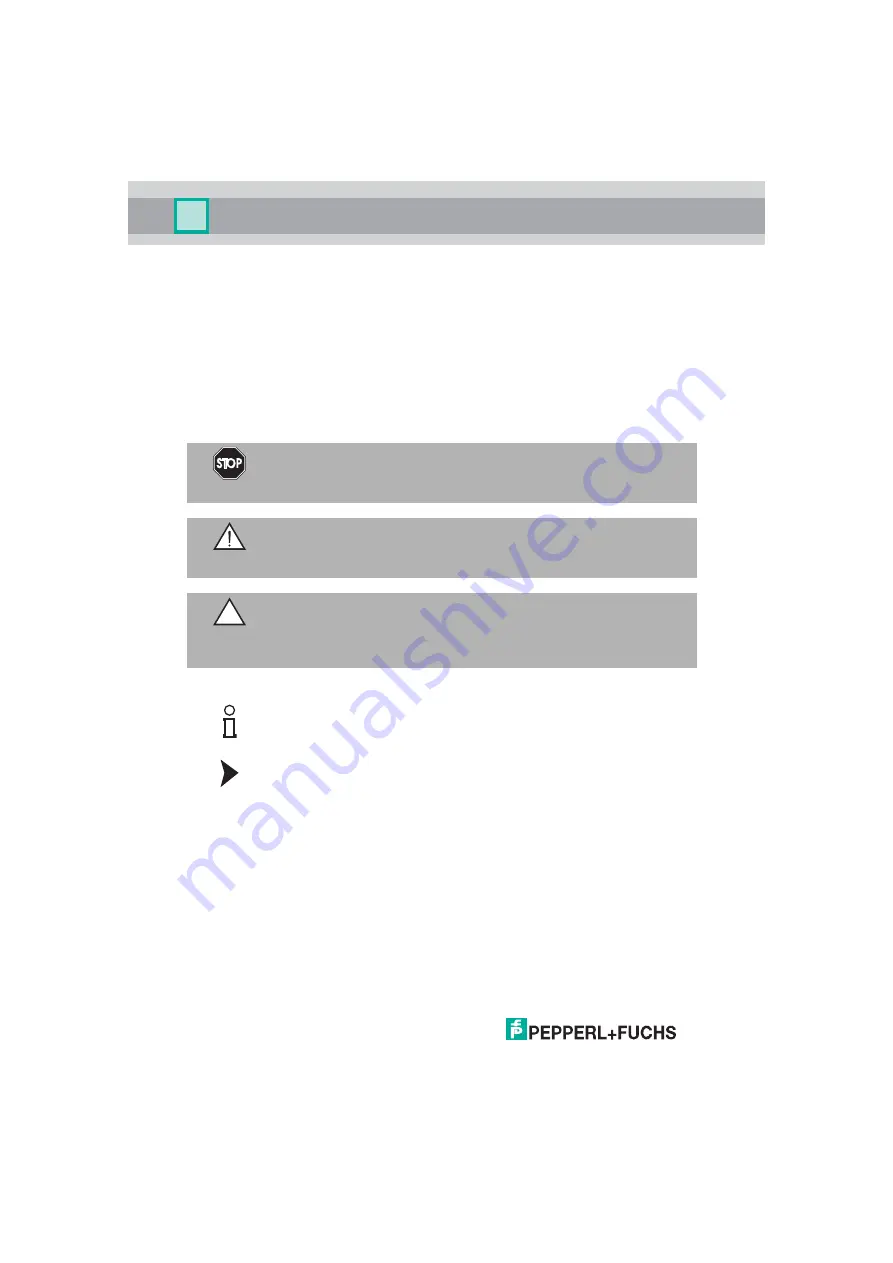
20
17-
06
6
Functional Safety HiC2883
Introduction
1.3
Symbols Used
This document contains symbols for the identification of warning messages and
of informative messages.
Warning Messages
You will find warning messages, whenever dangers may arise from your actions.
It is mandatory that you observe these warning messages for your personal safety
and in order to avoid property damage.
Depending on the risk level, the warning messages are displayed in descending
order as follows:
Informative Symbols
Action
This symbol indicates a paragraph with instructions. You are prompted to perform
an action or a sequence of actions.
Danger!
This symbol indicates an imminent danger.
Non-observance will result in personal injury or death.
Warning!
This symbol indicates a possible fault or danger.
Non-observance may cause personal injury or serious property damage.
Caution!
This symbol indicates a possible fault.
Non-observance could interrupt the device and any connected systems and
plants, or result in their complete failure.
Note!
This symbol brings important information to your attention.