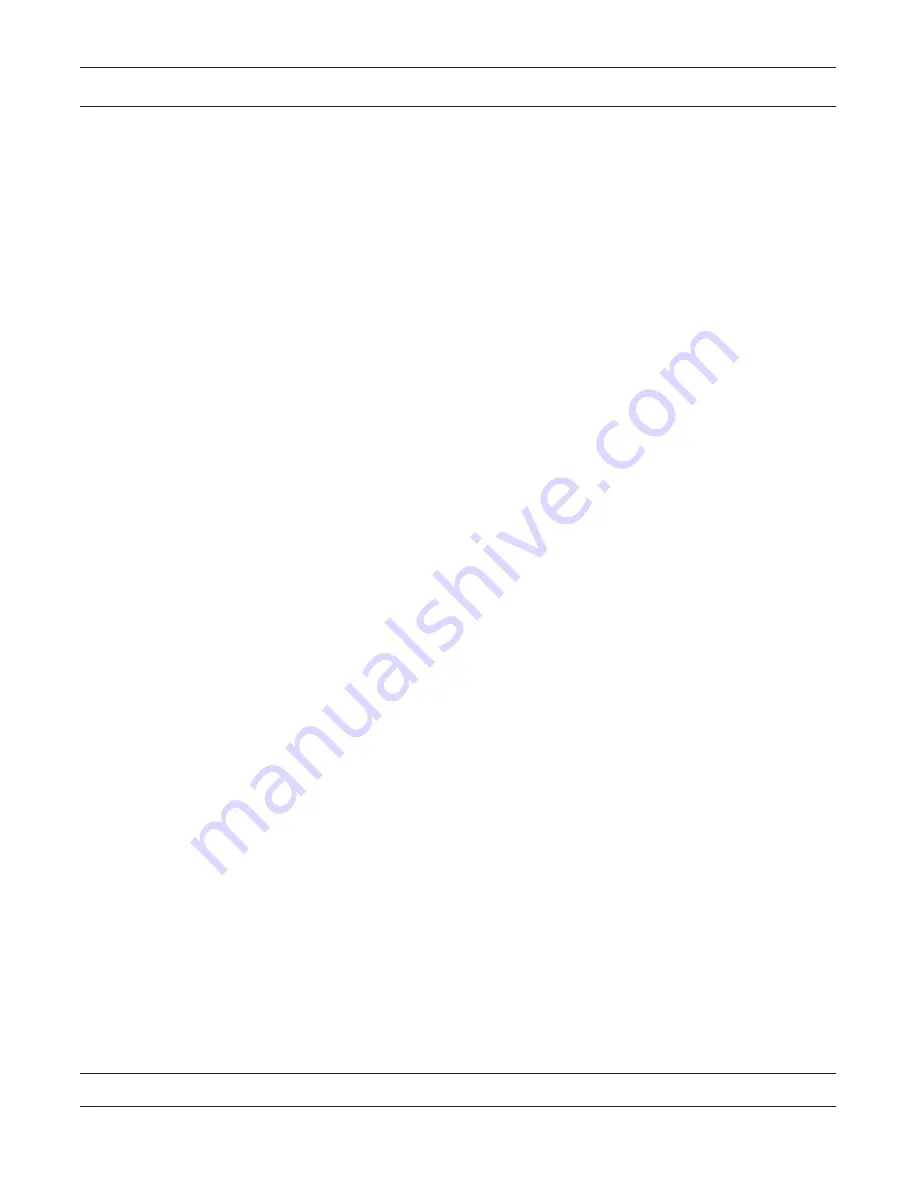
Page 13
Installation Instructions
Outlet Fittings
Apply thread sealant to the ¾” NPT thread of the adapter (Item 1) of the top end closure and securely thread the
male half of the union (Item 9, Outlet Fitting Kit) to it.
Apply thread sealant to both ends of the ¾” NPT nipple (Item 9, Outlet Fitting Kit), and securely thread it to the
female portion of the union (Item 9, Outlet Fitting Kit) and the elbow (Item 9, Outlet Fitting Kit). If installing with the
backflush kit, substitute the backflush kit for the elbow (see Figure 2).
Remove the red retainer clips and the adapters from the ends of the meter assembly (Item 10).
Apply thread sealant to the 3/4” NPT thread of the meter assembly adapters.
Securely thread one of the meter assembly adapters into the elbow (Item 9, Outlet Fitting Kit). If installing with the
backflush kit, substitute the tee from the backflush kit for the elbow (see Figure 2).
Drain Fittings
Apply thread sealant to the NPT nipples and reducer bushings (Items 11, Drain Fitting Kit).
Securely thread the male half of the union (Item 11, Drain Fitting Kit) to the ¾” NPT nipple.
Securely thread a reducer bushing (Item 11, Drain Fitting Kit) to the female half of the union (Item 11, Drain Fitting
Kit) and a reducer bushing to the inlet end of the DLFC (Item 13). The flow direction is indicated on the body of the
flow control.
Securely thread one of the 1/2” NPT nipples (Item 11, Drain Fitting Kit) into each reducer bushing (Item 11, Drain
Fitting Kit).
Securely thread the inlet port of the solenoid valve (Item 12) onto the 1/2” nipple which is connected to the union.
The valves flow direction is indicated on the valve.
Securely thread the outlet port of the solenoid valve (Item 12) onto the 1/2” nipple which is connected to the 7 gpm
DLFC. The flow direction is indicated on the body of the flow control.
Securely thread the 3/4” NPT nipple (Item 11, Drain Fitting Kit) into the top port of the vessel (Item 1).
NOTE: Use a wrench to hold the vessel’s side port when tightening a fitting, movement of the port could
damage the shell and/or the port.
Inlet Fittings
Apply thread sealant to the 3/4” NPT nipples (Items 7, Inlet Fitting Kit).
Securely thread one of the nipples into the outlet of the 10 GPM flow control (Item 8). The flow direction is indicated
on the body of the flow control.
Securely thread female half of the union (Items 7, Inlet Fitting Kit) into the nipple extending from the 10 GPM flow
control. If installing with the backflush kit, insert the backflush kit inlet solenoid valve between the union and the
flow control (see Figure 2). If installing the recommended fittings for integrity testing, install immediately prior to the
union (see Figures 1 and 2).
Securely thread the male half of the union (Items 7, Inlet Fitting Kit) onto the other 3/4” NPT nipple (Items 7, Inlet
Fitting Kit).
Securely thread the 3/4” NPT nipple (Items 7, Inlet Fitting Kit) into the bottom port of the vessel (Item 1).
NOTE: Use a wrench to hold the vessel’s side port when tightening a fitting, movement of the port could
damage the shell and/or the port.
Insert Vessel Top Head
Install the square cut seal into the groove below the stainless steel ring at the top end of the vessel. The seal should
be lubricated
lightly
on the ID surface only with the supplied silicone.
Installing the head into the vessel.
a. Install the top closure into the vessel. Using both thumbs, apply equal pressure on opposite sides of the head
to force it into the vessel so that it clears the retaining ring groove.
b. Carefully insert the retaining ring into the groove. This is done by inserting the lead end of the spiral ring
(end without bent tab) into the stainless steel retaining ring groove located in the shell, slowly pushing the
remaining turns into the shell.
c. Check that the spiral retaining ring is fully seated in the groove. If it is not, remove it and check for foreign
materials that would cause the spiral ring to not fully seat.
1.
2.
3.
4.
5.
1.
2.
3.
4.
5.
6.
7.
1.
2.
3.
4.
5.
1.
2.