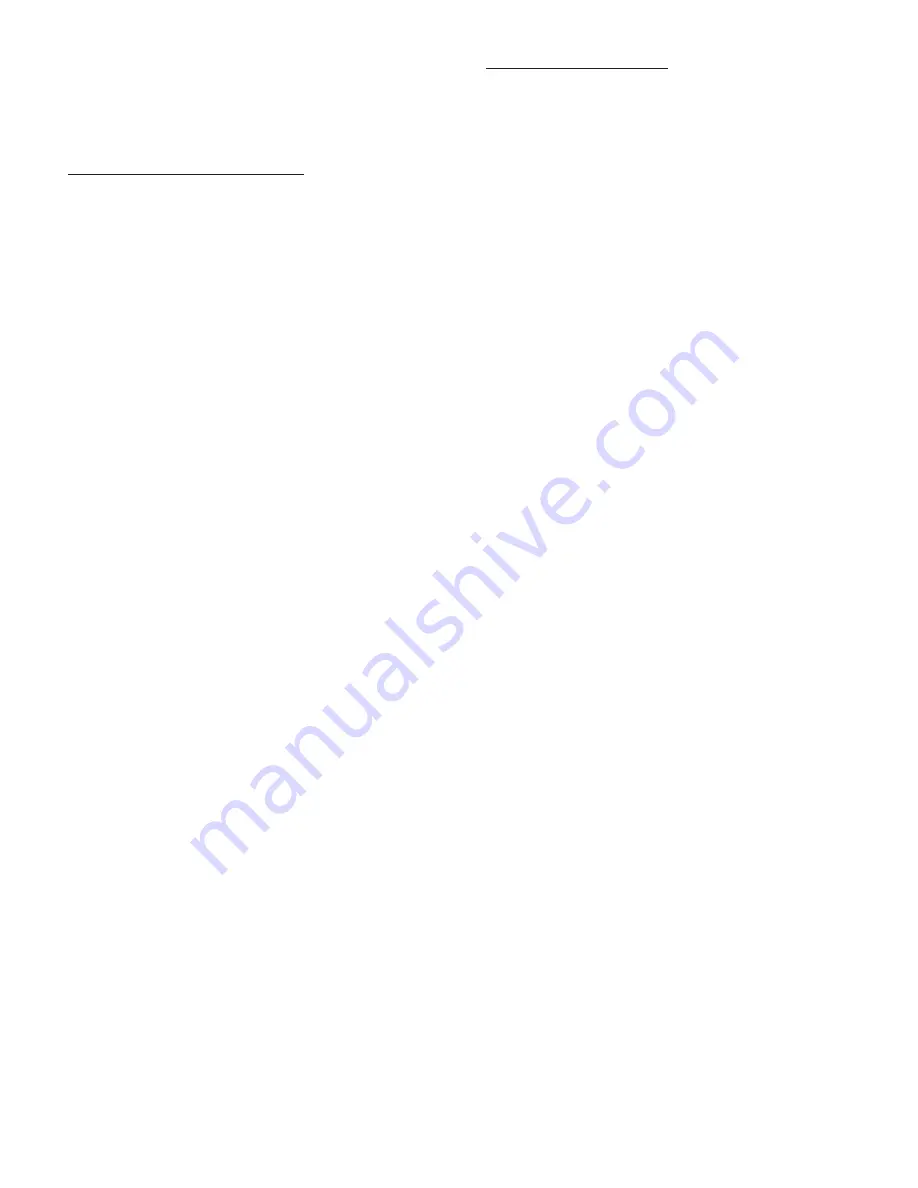
5
4
SEAL
Remove the rotating part of the seal by pulling it off the
shaft.
The stationary seat can be pressed from the
seal plate.
ASSEMBLY INSTRUCTIONS
All pump parts should be cleaned thoroughly before
being reassembled.
MOTOR
Assure that the rubber slinger is in place on the
motor shaft.
SEAL
A new pump seal should always be used when
rebuilding a pump.
Apply some light oil to the rubber that surrounds the
ceramic stationary seat. Insert the seal seat into the
seal plate using finger pressure to press firmly and
squarely until it bottoms. Care must be taken to keep
grease and dirt off face areas of the seal. Be sure the
seal faces are not damaged during assembly (cracked,
scratched or chipped) or the seal will leak.
Position the seal plate into the motor flange. Use care
not to chip the stationary seal seat by hitting the motor
shaft.
Carefully press the rotating seal assembly onto the
motor shaft. The smooth face of the carbon ring must
contact the ceramic seat. The rubber ring must seal
against the shaft.
IMPELLER
Hold the motor shaft and check that the rubber ring of
the seal is positioned on the shaft.
Turn the impeller clockwise onto the shaft.
Replace the capacitor taking care not to pinch any
wires and tighten capacitor clamp and replace motor
end cover taking care not to pinch any wires.
VOLUTE
Assure that a new or good condition gasket is in place
on the seal plate.
Carefully position the volute in alignment over the
impeller and seal plate.
Assemble the components. The bottom two cap screws
must also pass through the bracket.
RESTARTING OPERATION
The pump must be primed before starting. The pump
volute and suction piping must be filled with water
before starting motor. A hand pump or ejector can be
used for priming when desired.
Reconnect electrical power.
After a few minutes of operation, check that there is no
leakage from the pump or piping.
TROUBLESHOOTING
No water delivered.
1. Pump not properly primed; repeat priming
operation.
2. Discharge head too high. Check total head with
gauge at pump inlet and discharge. (With no
water, the gauge at discharge would show shut-off
pressure.)
3. Suction lift too high. Check with vacuum gauge. This
should not exceed 15 feet.
4. Air leak in suction line. Check line under pressure to
find leak.
5. Air pocket in suction line. Check line for
proper slope.
6. Impeller or suction line plugged.
7. Impeller and volute case badly worn. Disassemble
pump if clearance on diameter is over .030".
Replace worn impeller and worn volute case.
Not enough water delivered.
1. Discharge head too high. Check total head with
gauge at pump inlet and discharge. (With no
water, the gauge at discharge would show shut-off
pressure.)
2. Suction lift too high. Check with vacuum gauge. This
should not exceed 15 feet.
3. Air leak in suction line. Check line under pressure to
find leak.
4. Impeller or suction line plugged.
5. Impeller and volute case badly worn. Disassemble
pump if clearance on diameter is over .030".
Replace worn impeller and worn volute case.
6. Impeller diameter too small for condition required.
Not enough pressure.
1. Excessive volume being discharged. Throttle
discharge valve.
2. Air leak in suction line. Check line under pressure to
find leak.
3. Impeller or suction line plugged.
4. Impeller and volute case badly worn. Disassemble
pump if clearance on diameter is over .030".
Replace worn impeller and worn volute case.
5. Impeller diameter too small for condition required.
Pump runs for short while, then loses prime.
1. Suction lift too high. Check with vacuum gauge. This
should not exceed 15 feet.
2. Air leak in suction line. Check line under pressure to
find leak.
3. Air pocket in suction line. Check line for
proper slope.
4. Suction strainer plugged. Clean strainer.
Seal leaking.
Seal is worn or seal face cocked. Replace with new
seal and carefully follow directions.