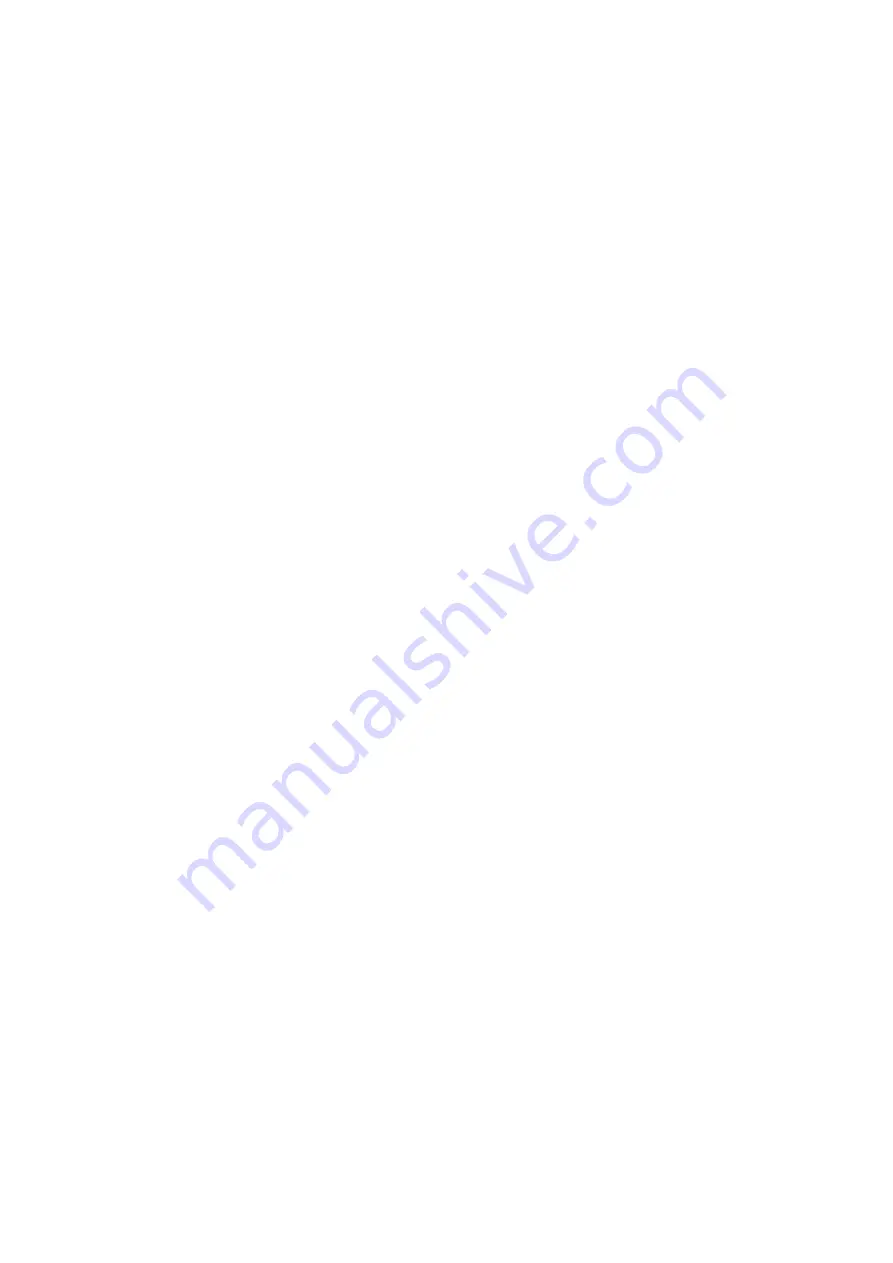
Features
•
Keep the work surface clean. Disorder invites to
injuries.
•
This precision pipe notch is a useful accessory
for your column drill, which allows you to make
round cuts in pipes of different shapes at any
angle from 0 ° to 45 °.
•
Sturdy and durable steel frame holds yours
workpieces in place during use.
•
The adjustable angle bracket (# 17) can be
adapted to any work table and is especially sui
-
table for mounting on column drilling tables.
•
The adjustable angle bracket (# 17) can rotates
and rotates, which together with the adjustable
holder makes it very easy to cut compound
angles.
•
Works with all standard column drills, and can
be adapted to a number of different circular
inserts, hole saws and milling inserts.
Warning:
When using this pipe notch with a power
tool, observe all safety instructions pertaining to
that equipment. See the operating instructions
for the power tool for safe operation when using
accessories.
Upackning
When unpacking, make sure the item is intact and
undamaged. If any parts are missing or broken,
please contact us.
Assembly
•
The spindle (# 7) is delivered incorrectly in
-
verted. Remove it and return it to the correct
position before using the tool.
•
Your pipe notch must be mounted on the co
-
lumn drill table using the angle bracket (# 17).
Depending on the configuration of your column
drill table, you can use T-bolts, trolley bolts or
standard machine bolts, washers and nuts.
•
After mounting, make sure that the spindle
(# 7) moves smoothly without locking to the
bushings (# 5). All unnecessary friction causes
excessive wear on the bushings (# 5).
•
The angle of the pipe notch can be adjusted
by loosening the bolts (# 16) that adjust the
adjustable angle bracket (# 17), and move the
assembly as much as needed.
•
To make side-to-side adjustments, adjust the
bolts (# 15) that hold the adjustable angle
bracket (# 17) to the body (# 13).
•
When installing the hole saw, first check if its
shaft is 1.27cm (1/2 ”) or 1.59cm (5/8”). The
spindle thread is for 1.27cm (1/2 ”), the doll has
a hole saw adapter (# 3) for a thread of 1.59cm
(5/8”) that can be screwed on over 1.27cm
(1/2 ”) -The thread. You may need to use the
hole saw adapter washer (# 4) for a good and
secure fit.
•
To install a saw blade or cutter, first fix the
spindle (# 7) with the locking pin (# 14). Do not
use a locking bar or clamps to hold the spi
-
der (# 7), as this will cause damage. Slide the
locking pin (# 14) through the hole on the side
of the spindle support (# 6) and through the
spindle (# 7). Install the blade, then remove the
locking pin (# 14).
Use
1. Insert the pipe you want to cut into the clamp
assembly (# 1), under the inverted ”V”. The
inverted V-function of the clamp holds your
pipe (up to 2 ”long) in place. Do not insert the
tube more than half its length. When cutting at
sharp angles, just insert the tube far enough to
start cutting. Use the handle / steering wheel
mounting (# 2) to hold the tube in place.
2. Set the speed of your column drill to around
500 rpm for most materials. When cutting hard
alloy pipes with thin walls, higher speeds are
required. When cutting softer, coarser materi
-
als, a lower speed may be appropriate. Sugges
-
tion: Practice on leftover material before cutting
into your work material.
3. While working, lubricate both the hole saw
and the bushings with cutting oil to extend the
service life.
4. When cutting sharp angles with larger diameter
pipes, you need to set the spindle support (# 6)
in the highest position to make room. However,
you should always position the spindle support
(# 6) as low as possible to maintain accuracy.
To move the spindle support (# 6), you only
need to loosen the two bolts (# 16) that secure
it to the body (# 13), and move and fasten the
bolts (# 16) again.
5. To adjust the angle of the clamp, loosen the
bolts (# 15) that hold them against body (# 13)
and then continue cutting the workpiece.
6. When the pipe is clamped in the pipe notch and
the angle is correct, you can start cutting the
workpiece.
7. To remove the blade or insert, turn off the
column drill, insert the locking pin (# 14) into
the spindle support (# 6) and remove the insert.
Maintenance
•
Observe good workshop practice for your safe
-
ty and to extend the life of your tools.
•
Brush chips and debris from the pipe notch
continuously, especially from the bushings and
the spindle area to avoid these components are
scratched or stuck.
•
Use a suitable light grease on the bushings to
prevent overheating and wear.
•
Use cutting fluid properly to prevent tools or
materials from overheating and to remove cut