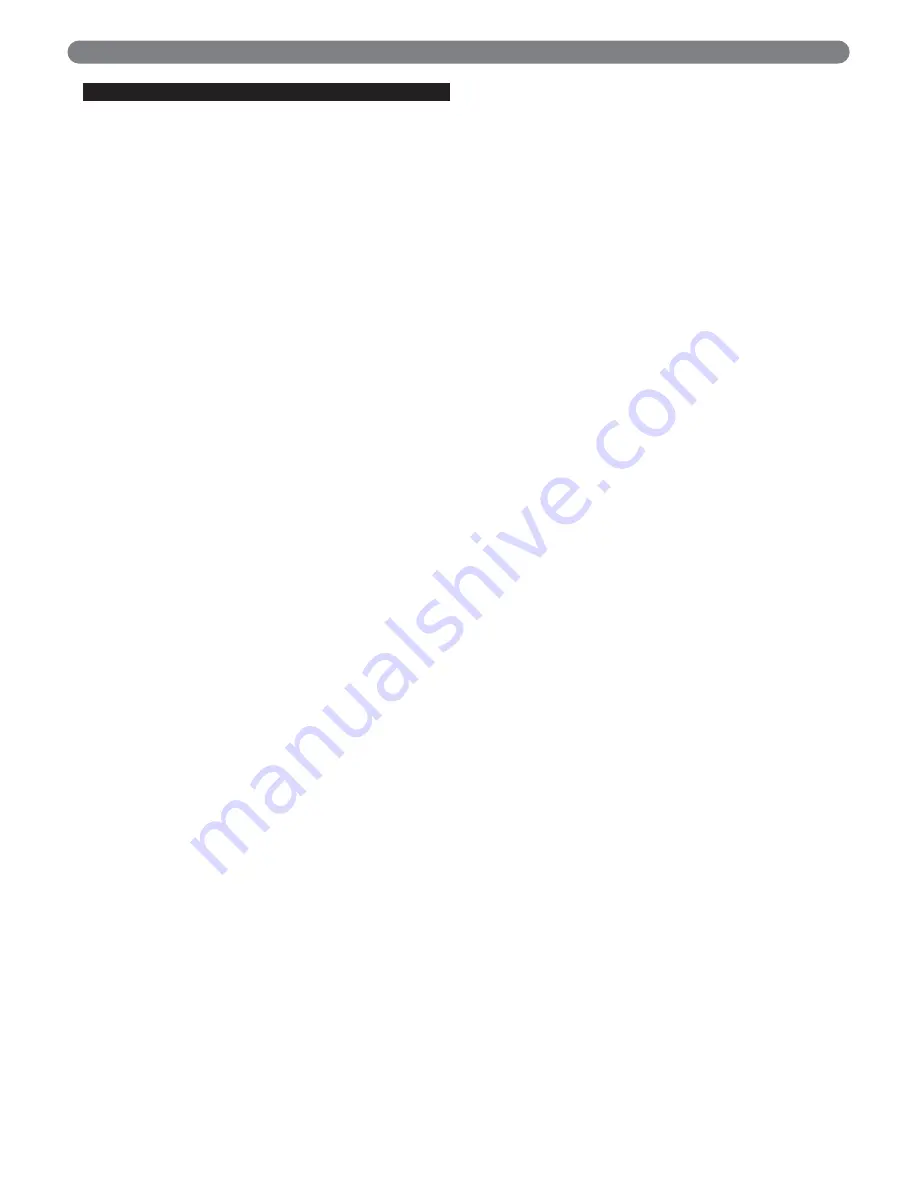
19
ELECTRICAL
D. BOILER SEQUENCE OF OPERATION
1. Thermostat calls for heat.
2. Limit control energizes circulator.
3. Limit control energizes B1 circuit if boiler water
temperature is below setpoint minus differential.
Setpoint is calculated according to thermostat cycle
and economy/efficiency setting. See limit control
literature for further information.
4. BR relay energizes blower.
5. Negative pressure induced by blower switches
Pressure Switch, continuing power through closed
contacts (BR-2) and flame roll-out switch.
6. Gas valve energizes.
a. Ignitor on.
b. Pilot gas on, igniting pilot
7. Pilot flame detected.
a. Ignitor off.
b. Main gas on, igniting main burners.
Note: If pilot flame is not detected within 90 seconds,
the igniter and pilot are turned off for 5 minutes. The
sequence then resumes at Step 6a.
8. Call for heat ends.
a. Pilot and main gas off, extinguishing pilot and
main burners.
b. Blower and circulator off.
Summary of Contents for PSC II
Page 1: ...PSC II Boilers Series Gas Installation Operation Maintenance Manual...
Page 14: ...12 Figure 4 3 Vertical Venting System VENTING VENTILATION AND AIR INLET...
Page 24: ...22 START UP PROCEDURES Figure 7 3 Operating Instructions...
Page 25: ...23 START UP PROCEDURES Figure 7 4 Operating Instructions...
Page 34: ...32 MAINTENANCE Figure 9 2 Inspection of Flueways Burners and Vent System...
Page 38: ...36 REPAIR PARTS Figure 11 2...