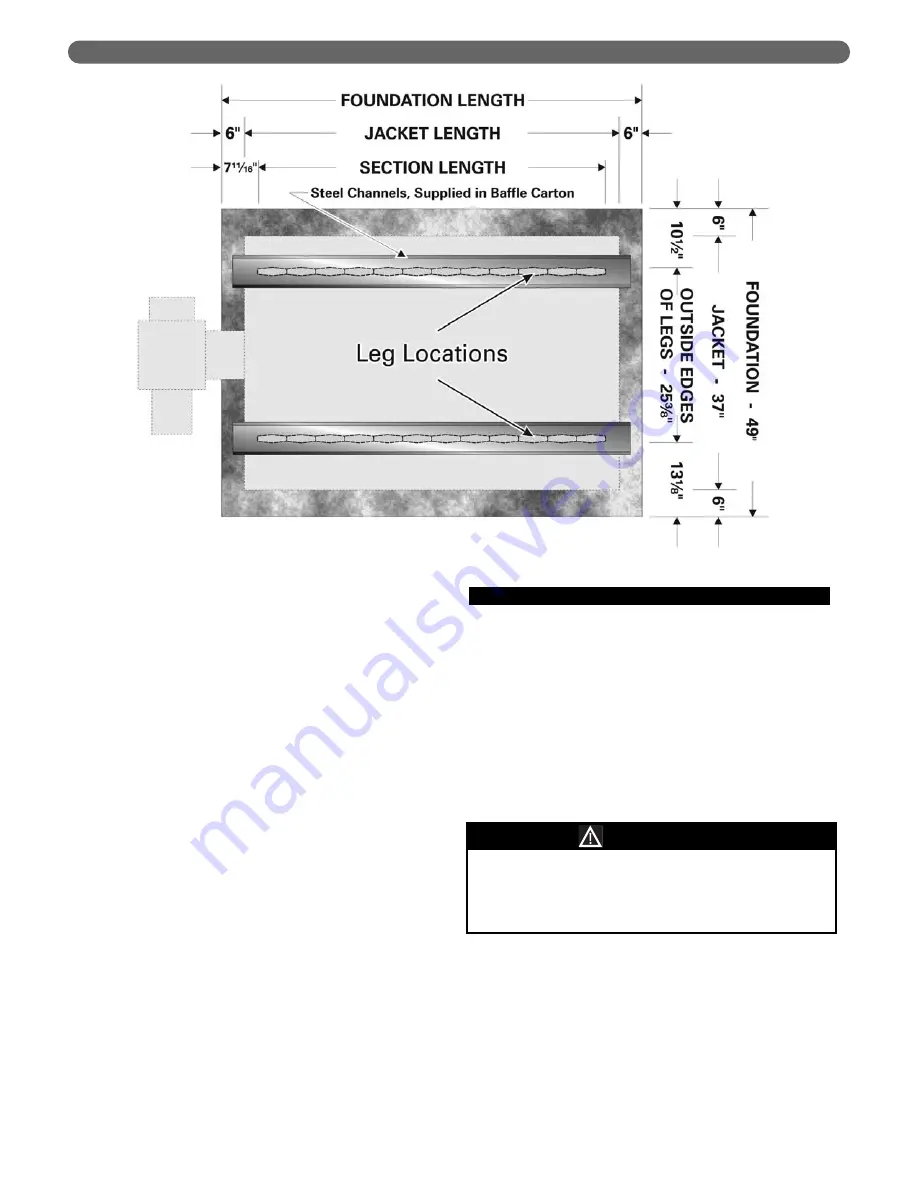
4
8. Exterior Vents:
a) Insulate sufficiently to ensure adequate draft and
to prevent vent damage due to condensation.
9. Vent Connection to Boiler:
a) Support the weight of the vent system
independently of the boiler flue connection.
b) Provide support of the vent connector
(breeching) at maximum 12 foot intervals to
prevent sagging and to provide a minimum
upward slope of 1/4" per foot.
10. Do not vent natural draft appliances in a combined
vent which operates under positive pressure.
11. Draft Regulator: Install a barometric draft regulator
where using high chimney or any high draft vent.
This is needed to prevent causing negative draft in
the boiler. Excess draft will cause flame lifting and
possible impingement.
12. The Draft Damper for the LCE boiler is a separate
piece, shipped in the Top Flue Outlet Carton.
a) Install the Draft Damper as close as possible to
the boiler flue outlet. It can be installed vertically
or horizontally provided that the connecting vent
piping and fittings are designed and installed for
pressurized service.
b) Secure the damper to the vent with screws and
seal the joints with a bead of high temperature
silicone sealant (found in Section Assembly Kits).
c) The vent must be installed so it can be
disconnected and the Top Flue Outlet removed
for proper cleaning of the flueways.
E. BOILER SETTING
1. If the boiler room floor is not level or if additional
structural support is needed, provide a good, level
foundation for the boiler with the minimum
dimensions given in Table 1.1. The flooring and
structural support system must be suitable for the
operating weight of the boiler and any connected
piping. Place the Steel Channels on the foundation
as shown in Figure 1.4.
2. Do not operate the boiler until the foundation, if new
concrete, has thoroughly cured. The concrete might
be damaged if heated too quickly due to the
entrained moisture remaining.
3. If the boiler is installed in a penthouse or if wiring of
any sort is run underneath the boiler foundation,
construct the foundation with provision for air flow
underneath between the main floor and the top of
the boiler foundation.
a) An acceptable foundation would be concrete
blocks laid with the openings lined up.
Do not install this boiler on carpeting or any
combustible flooring. A significant fire hazard could
result, with potential for property damage, personal
injury or death.
WARNING
Figure 1.4: Foundation Layout
PREINSTALLATION
Summary of Contents for Gas/Oil Boilers
Page 1: ...LC LCE Gas Oil Boilers Water Series Oil Gas Installation Operation Maintenance Manual...
Page 15: ...13 PLACE THE BOILER Figure 2 5 Series LC Boiler Assembly Right Side View...
Page 16: ...14 PLACE THE BOILER Figure 2 6 Series LCE Boiler Assembly Right Side View...
Page 18: ...16 Figure 2 9 LC LCE Boiler Section Assembly Sequence PLACE THE BOILER...
Page 26: ...24 Figure 3 6 Piping for Variable Low Temperature Systems Single Boiler PIPE THE BOILER...
Page 28: ...26 Figure 3 8 Piping for Variable Low Temperature Systems Multiple Boilers PIPE THE BOILER...
Page 30: ...28 ASSEMBLE THE JACKET Figure 4 2 Jacket Assembly...
Page 37: ...35 INSTALL CONTROLS AND TRIM Figure 8 2 Control and Pipe Tapping Locations...
Page 50: ...48 REPAIR PARTS Figure 12 2 Series LCE Boiler Assembly...
Page 53: ...51 NOTES NOTES...
Page 54: ...52 NOTES...