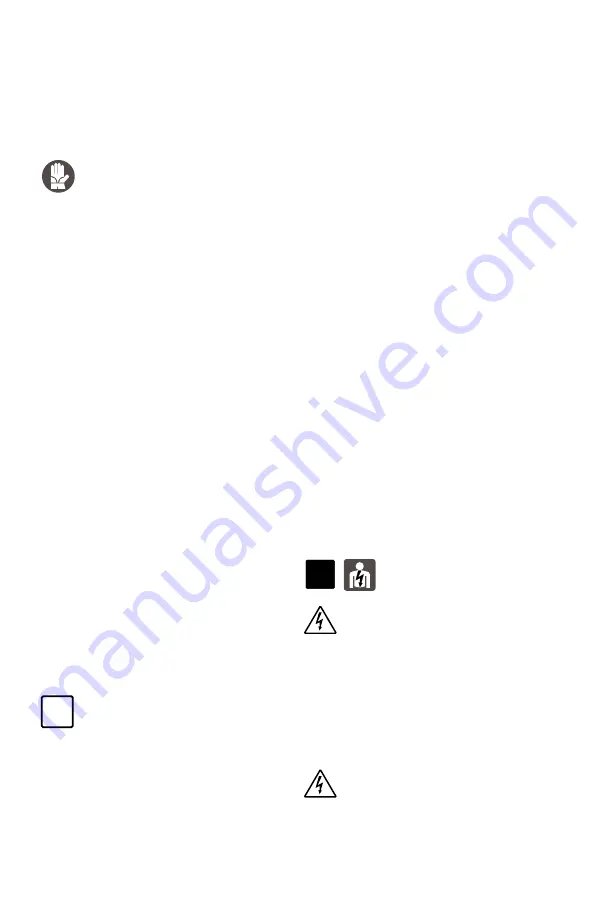
4.5. Individual protection devices
During installation, starting and maintenance it is suggested
to the authorized operators to consider the use of individual
protection devices suitable for described activities.
During ordinary and extraordinary maintenance interventions,
safety gloves are required.
Signal Individual protection device
HAND PROTECTION
(gloves for protection against chemical, thermal and
mechanical risks).
5. TRANSPORTATION AND HANDLING
The product is packed to maintain the content intact.
During transportation avoid to stack excessive weights.
Ensure that during the transportation the box cannot move.
It is not necessary to use any special vehicle to transport the
packaged device.
The transport vehicles must comply, for the weight and
dimensions, with the chosen product (see technical catalogue
dimensions and weights).
5.1. Handling
Handle with care, the packages must not receive impacts.
Avoid to impact onto the package materials that could damage
the pump.
If the weight exceeds 55 lbs the package must be handled by
two person at the same time.
6. INSTALLATION
6.1. Dimensions
For the dimensions of the device (see technical catalogue).
6.2. Ambient requirements and installation site dimensions.
The customer has to prepare the installation site in order to
guarantee the right installation and in order to fulfill the device
requirements (electrical supply, etc...).
The place where the device will be installed must fulfill the
requirements in the paragraph
3.2. Operating conditions
It’s Absolutely forbidden to install the machine in an environment
with potentially explosive atmosphere.
6.3. Unpacking
Inspect the device in order to check any damages
which may have occurred during transportation.
Package material, once removed, must be discarded/
recycled according to local laws of the destination
country.
6.4. Installation
See installation examples, par. 13 fig. 1 and 2.
The pumps must be installed with the rotor axis in the horizontal
position and with the feet under the pump.
Place the pump as close as possible to the suction source.
Provide space around the pump for motor ventilation, to allow
for checking of shaft rota-tion, for filling and draining the pump.
i
OFF
ON
6.4.1. Pipes
Ensure the insides of pipes are clean and unobstructed before
connection.
ATTENTION: The pipes connected to the pump should be
secured to rest clamps so that they do not transmit stress, strain or
vibrations to the pump (par. 13 fig. 3).
Tighten the pipes or union coupling to the extent sufficient to
ensure a tight seal.
Excessive torque may cause damage to the pump.
When the pipe or union coupling is mounted, keep the pump
casing connection blocked with a second wrench, making sure
the connection is not deformed by excessive tightening.
The pipe diameters must not be smaller than the pump
connections.
6.4.2. Suction pipe
For capacities over 17,6 US gpm use a suction pipe 1” 1/4 (DN
32).
The suction pipe must be perfectly airtight and be led upwards in
order to avoid air pockets.
With a pump located above the water level (suction lift operation,
par. 13. fig. 2) fit a foot valve with strainer which must always
remain immersed or a check valve on the suction connection.
If operating with flexible hoses use a reinforced spiral suction
hose, in order to avoid the hose narrowing due to suction vacuum.
With the liquid level on the suction side above the pump (inflow
under positive suction head, par. 13. fig.1 fit an inlet gate valve.
For suction from a storage tank fit an anti-backflow valve. Follow
local specifications if increasing network pressure.
Install a strainer on the suction side of the pump to prevent
foreign particles from entering the pump.
6.4.3. Delivery pipe
Fit a gate valve in the delivery pipe to adjust delivery and head.
Install a pressure gauge.
With a geodetic head at outlet over 49 ft fit a check valve
between the pump and the gate valve in order to protect the
pump from water hammering.
6.5. Electrical connection
Electrical connection must be carried out only by
a qualified electrician in accordance with local
regulations.
Always follow the National Electrical Code (NEC), or the
Canadian Electrical Code, as well as all local, state and provincial
codes. Code questions should be directed to your local electrical
inspector. Failure to follow electrical codes and OSHA safety
standards may result in personal injury or equipment damage.
Failure to follow manufacturer’s installation instructions may
result in electrical shock, fire hazard, personal injury or death,
damaged equipment, provide unsatisfactory performance, and
may void manufacturer’s warranty.
Install, ground and wire according to local and National
Electrical Code Requirements.
Electrical supply MUST match pump’s nameplate specifications.
Incorrect voltage can cause fire, damage to the motor and voids
the warranty.
Pumps not protected MUST be provided with contactors and
thermal overloads for single phase motors. See motor nameplate.
i
OFF
ON
i
OFF
ON
i
OFF
ON
i
OFF
ON
i
OFF
ON