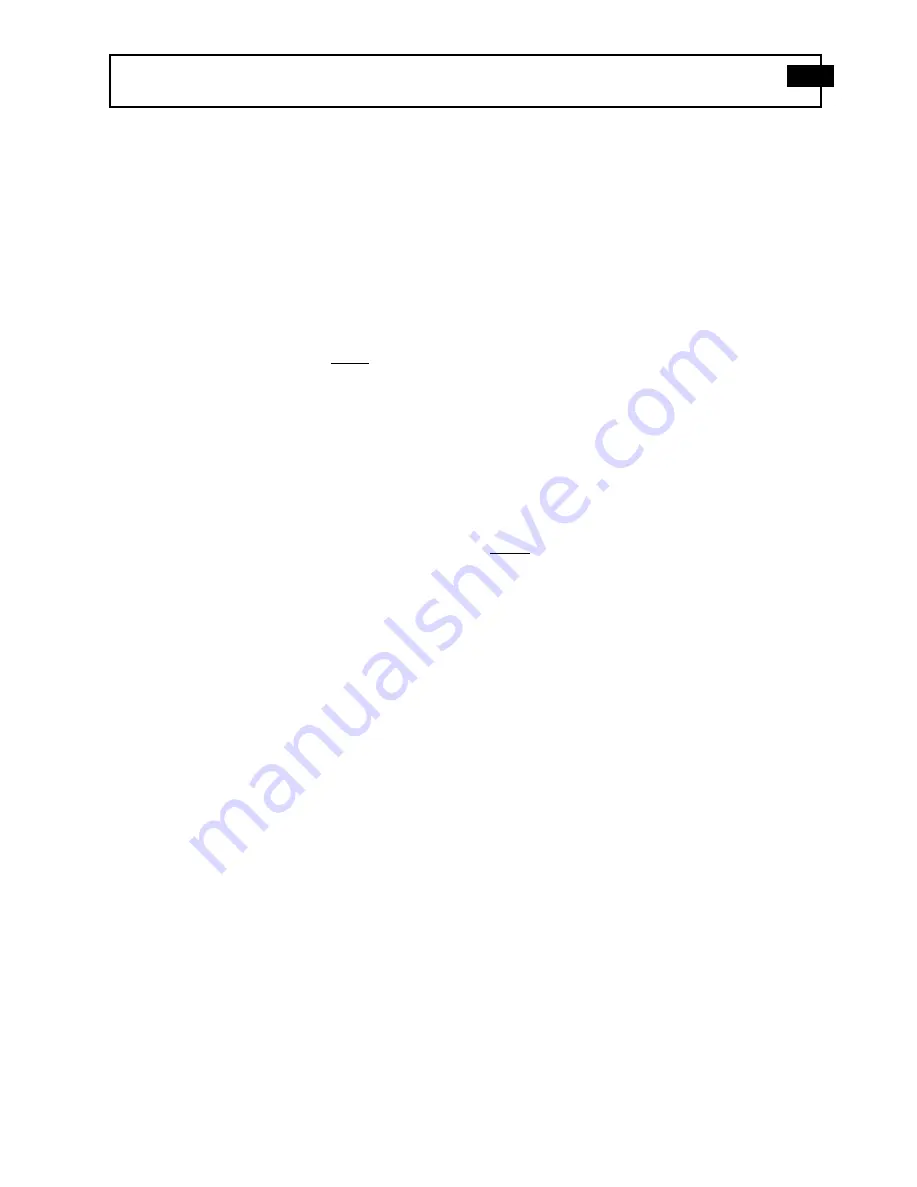
ICP
®
IMPEDANCE HEAD (DRIVING POINT SENSOR) OPERATION MANUAL
1
1.0
Introduction
Mechanical structures characteristically transfer motion and
force; their product is defined as mechanical energy. By
imparting motion and force to a specimen through the
impedance head (also known as a driving point sensor) and
evaluating the data, a better understanding of the behavior of
the test object is achieved.
The term
“
mechanical impedance
”
is quite important in
analyzing structures and is generally defined as Force divided
by Velocity:
Mechanical Impedance =
Force
Velocity
More commonly, however, the input force-to-output motion
relationship is viewed at driving points as Acceleration divided
by Force. This is properly defined as an inertance frequency
response function.
Connection between a stinger or shaker armature and the test
specimen is made via the 10-32 tapped holes provided at either
end of the Model 288D01.
2.0
Description
Refer to the Installation Drawing provided in this manual for
the exact dimensions of the Model 288D01. This unit is
designed to maximize stiffness and natural frequency and to
minimize mass compensation, cross talk, and transverse
sensitivity. The impedance head is engineered to minimize the
strain sensitivity of the accelerometer and to reduce the
acceleration sensitivity of the force gauge.
The built-in microelectronic amplifiers convert the high-
impedance signals generated by the quartz-element force
gauge and the ceramic-element accelerometer to low-
impedance voltage signals.
If you wish to learn more about sensors with built-in
microelectronic circuitry, known as ICP
®
sensors, consult
PCB
’
s
“
General Operating Guide for use with Piezoelectric
ICP
®
Accelerometers,
”
a brochure (included in this manual)
outlining the technical specifics associated with piezoelectric
sensors. Topics covered include charge versus voltage mode
systems, sensor time constants, effect of discharge time
constant on low frequency response, and power requirements.
3.0
Installation
For details regarding mounting hole preparation and other
installation guidance, consult the Installation Drawing
provided in this manual.
It is important to make certain that the mating surfaces at both
ends of the Model 288D01 are very flat. While ground
surfaces are preferable, satisfactory surfaces may be obtained
by other machining techniques, such as turning, milling and
spotfacing.
The clearly labeled end of the force sensor should be attached
to the test object. Usually, the driving point sensor is
connected to the test structure through an adhesive mounting
base. The base is typically bonded with an extremely stiff
“
dental cement
”
type adhesive. If the sensor is stud mounted,
however, tighten to the recommended mounting torque as
listed on the Installation Drawing.
NOTE: Ensure that the Model 288D01 is installed properly
with the connector end attaching to the stinger. This is unlike
the previous versions of impedance heads (Model 288B01 and
earlier), which were installed with the connectors closest to the
structure interface.
Connect the stinger or shaker armature to the other end. A
stinger is a thin, flexible rod that helps ensure that only
uniaxial force is applied to the test structure. For more
information on stingers, refer to the Excitation Stinger Data
Sheet included in this manual.
Caution
When torquing on the sensor, be careful not to damage the
connectors with the torque wrench.
NOTE: To avoid any phase shift between force and reference
acceleration at higher frequencies, provide a rigid mount
between the sensor and the test structure by using a stud or
suitably stiff adhesive.
4.0
Operation
Connect the force and acceleration connectors to the respective
ICP
®
signal conditioners using Model 002A Coaxial Cable (or
its equivalent). Check to ensure that cable connections are
tight.
Most PCB signal conditioners employ a fault-monitoring
voltmeter incorporated into the front panel to monitor sensor
bias voltage. Normal operation of sensor amplifiers is
indicated by a mid-scale reading on this meter.
The outputs of the signal conditioners may be connected
directly to the analyzer since the output impedance of the
sensor is less than 250 ohms.
5.0
Maintenance and Repair
The sealed construction of the Model 288D01 precludes field
maintenance. Should problems occur, contact the factory for
instructions on returning the unit for repair or replacement.
MANUAL NUMBER: 18296
MANUAL REVISION: NR