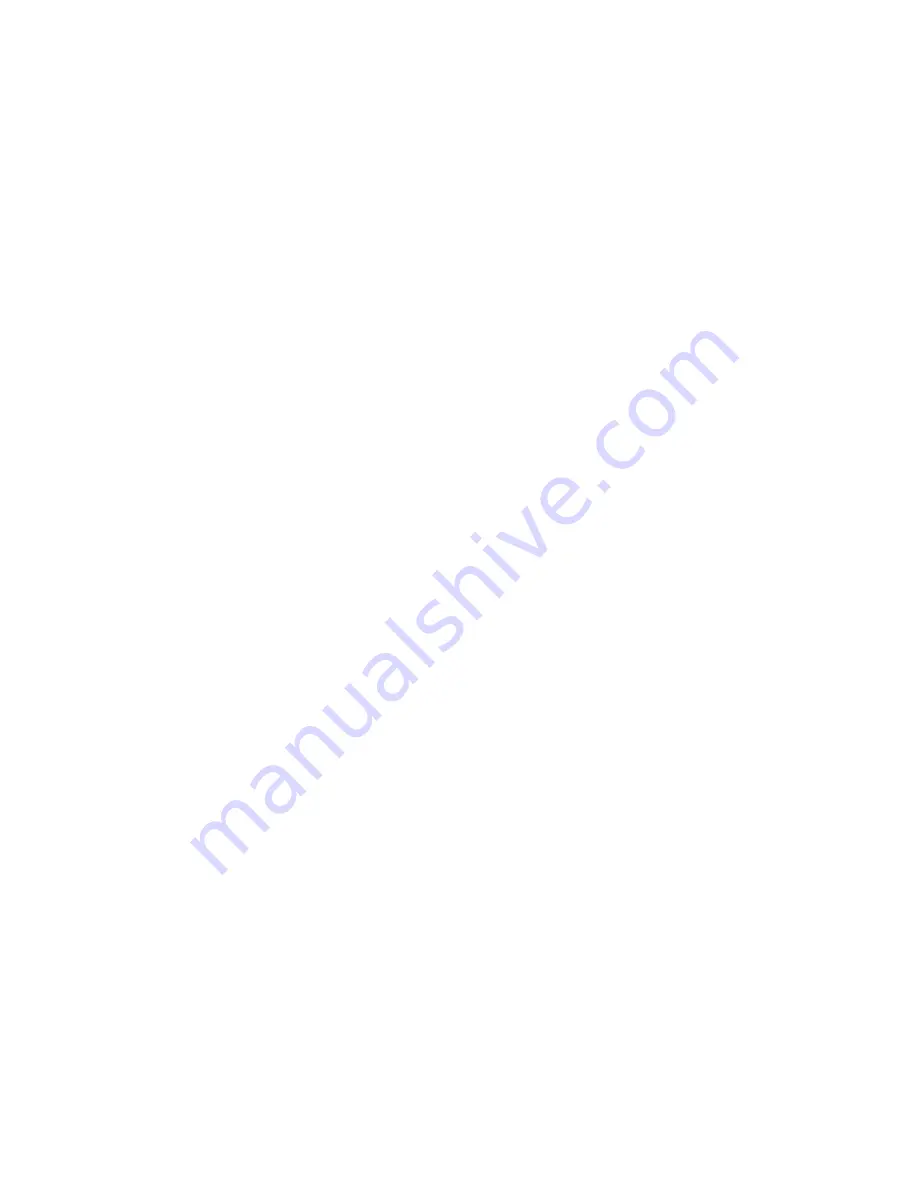
1
General
OPERATING GUIDE
for use with
PIEZOELECTRIC CHARGE MODE ACCELEROMETERS
SPECIFICATION SHEET, INSTALLATION DRAWING
AND CALIBRATION INFORMATION ENCLOSED
PCB ASSUMES NO RESPONSIBILITY FOR DAMAGE CAUSED TO THIS PRODUCT AS A RESULT OF
PROCEDURES THAT ARE INCONSISTENT WITH THIS OPERATING GUIDE.
1.0 INTRODUCTION
Congratulations on the purchase of a quality PCB charge
mode accelerometer. In order to ensure the highest level
of performance for this product, it is imperative that you
properly familiarize yourself with the correct mounting
and installation techniques before attempting to operate
this device. If, after reading this manual, you have any
additional questions concerning this sensor or its
application, feel free to call an Application Engineer at
716-684-0001 or the closest PCB representative.
2.0 CHARGE MODE ACCELEROMETERS
Ceramic and UHT 12 shear-structured accelerometers
offer high performance for precision vibration
measurements in high-temperature environments. The
use of sensing crystals, operating in the shear mode,
reduces erroneous output due to base strain, thermal
transients, and transverse motion.
Charge mode accelerometers output a strong, high-
impedance charge signal directly from their sensing
element. They do not contain built-in signal
conditioning electronics; the signal is conditioned
externally by either a laboratory-style charge amplifier
or in-line charge converter prior to being analyzed by a
readout or recording device. The absence of built-in
electronics permits operation to elevated temperatures of
500 °F (260 °C) for most ceramic crystal models and
typically 900
°
F
(482 °C) and extreme application up to
100 °F (650 °
C)
for
UHT-12.
These accelerometers are ideal for structural testing,
machine monitoring, and vehicular shock and vibration
measurement tasks where high temperatures preclude
the use of accelerometers with built-in microelectronics.
Enclosed is a
Specification Sheet
, which lists the
complete performance characteristics of the particular
accelerometer.
3.0 OPTIONAL FEATURES
In addition to these standard features, a variety of
options are also available. When listed before the model
number, the following prefix letters indicate that the
sensor is manufactured or supplied with optional
features:
A
option- adhesive mount;
J
option- electrical
ground isolation;
M
option- metric mounting thread;
P
option- positive polarity output (for use with non-
inverting, signal conditioning amplifiers); and
W
option-
water-resistant cable connection.
4.0 INSTALLATION OVERVIEW
When choosing a mounting method, consider closely
both the advantages and disadvantages of each
technique. Characteristics like location, ruggedness,
amplitude
range,
accessibility,
temperature,
and
portability are extremely critical. However, the most
important and often overlooked consideration is the
effect the mounting technique has on the high-frequency
performance of the accelerometer.
Shown hereafter are six possible mounting techniques
and their effects on the performance of a typical
piezoelectric accelerometer. (Note that not all of the
mounting methods may apply to your particular sensor.)
The mounting configurations and corresponding graph
demonstrate how the high-frequency response of the
accelerometer may be compromised as mass is added to
the system and/or the mounting stiffness is reduced.
Note:
The low-frequency response is unaffected by the
mounting technique. Its roll-off behavior is dependent