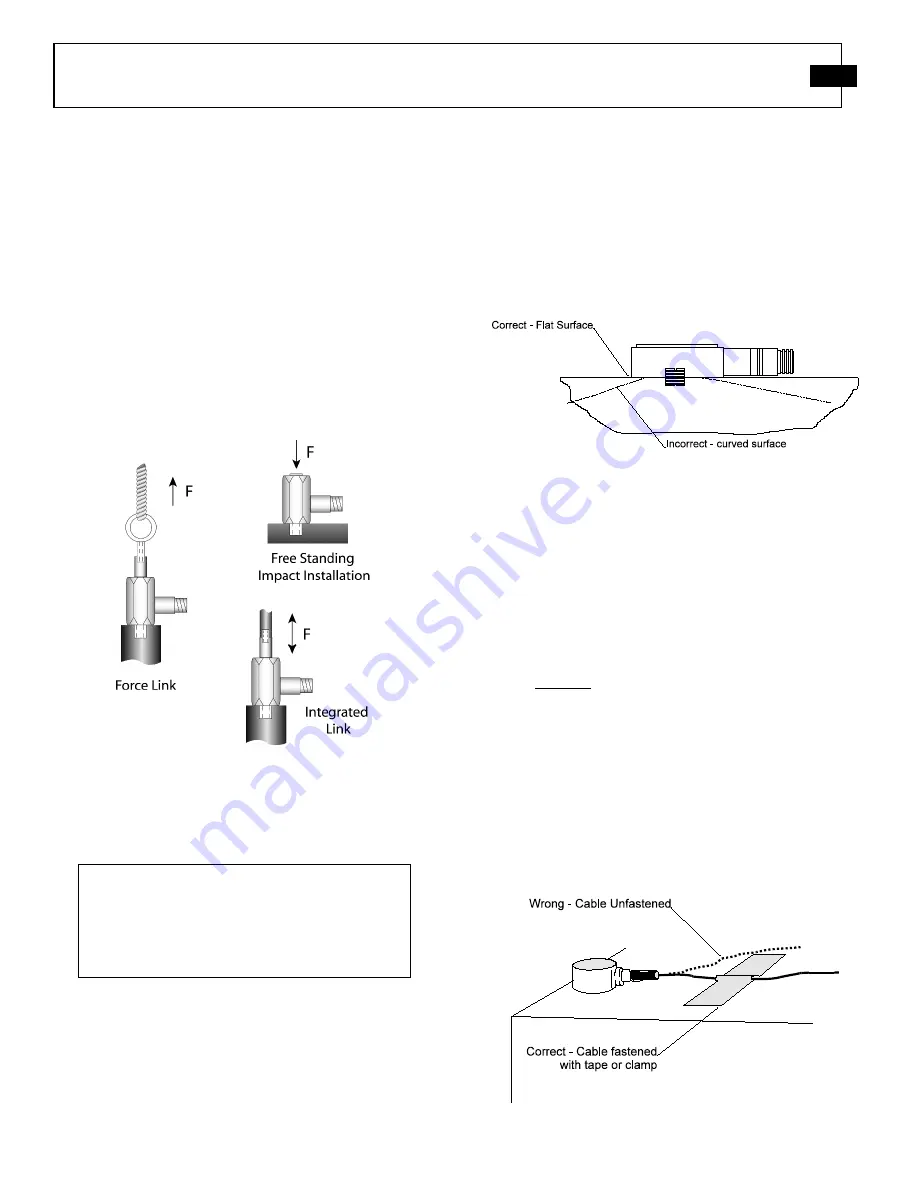
ICP
FORCE SENSOR OPERATION MANUAL
5
the sensor. Link, integrated link, and freestanding installations
are possible as outlined in Figure 9.
Caution
– Bending moment concerns
In this model, axial application of forces is critical during
measurements due to the sensitivity to bending moments. This
sensor series has a very high output (2200mV/lb, 500mV/N) so
care should be taken that applied forces are axial to prevent
unwanted output (noise) due to bending moments. In addition,
the “hat” applied to certain models enabling direct tensile
measurements is very small. Axial loads or excessive masses
applied to this “hat” could cause it to break away from the main
sensor body.
Due to its highly sensitive characteristic, Series 209 sensors
may be susceptible to thermal drift caused by temperature
transients. These sensors are recommended for use in
temperature stable environments only.
Figure 10 - Series 209 Miniature/High Sensitivity
ICP
Force Sensor
3.0 INSTALLATION
Refer to the Installation Drawing supplied with this manual for
specific outline dimensions and installation details for your
particular model. The specification is also included to provide
details of the sensor’s characteristic properties.
It is important that the surface to which each sensor is mounted
be perfectly flat to avoid flexing of the base, which could affect
sensor sensitivity and result in erroneous data (see
Figure 11
).
A good mating surface may be obtained by lapping, turning,
spot-facing, or surface grinding. Surface flatness should be
held to within 0.001 (TIR) over the entire mating surface.
When mounting sensors between two plates care should be
taken to assure mounting surfaces are flat and parallel. Non-
parallel surfaces could place unwanted stress on internal
components leading to premature sensor failure. The protective
cap should remain on the electrical connector during
installation to prevent connector contamination or damage.
Figure 11 - Force Sensor Installation
A light coating of silicon grease (DC-4 or equivalent) on the
mating surface enhances the coupling between the mounting
base and mounting surface and provides the best high-
frequency response.
Connect one end of the coaxial cable to the sensor connector
and the other end to the XDCR jack input on the signal
conditioner. Make sure to tighten the cable connector to the
sensor. DO NOT spin the sensor onto the cable, as this fatigues
the cable’s center pin, resulting in a signal with a shorted output
or intermittent signal and a damaged cable.
For installation in dirty, humid, or rugged environments, it is
suggested that the electrical connection be shielded against dust
or moisture with shrink tubing or other protective material.
Strain relieving the cable/sensor connection can also prolong
cable life. Mounting cables to a test structure with tape,
clamps, or adhesives minimizes cable whip. See
Figure 12
for
an example of a sensor installation with a securely fastened
cable.
CAUTION!
Please read all instructions before attempting to
operate this product.
Damage to built-in amplifier
due to incorrect power or misapplication is NOT
covered by warranty
Summary of Contents for 209C11
Page 17: ......