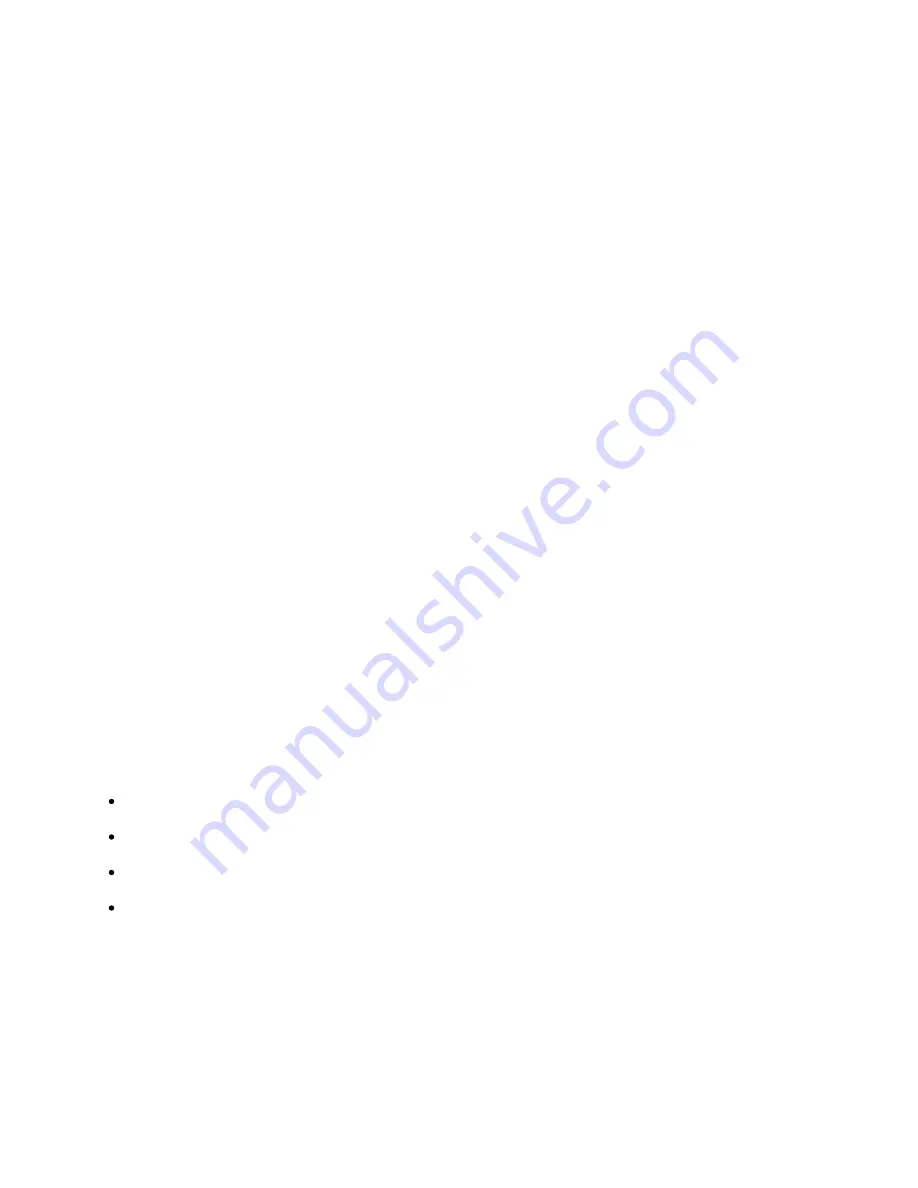
2
SECTION III
INSTALLATION
3-1
Location:
Several factors should be considered when selecting a location for the pumping. The unit should be
accessible for both inspection and maintenance. Headroom should be provided for the use of crane,
hoist or other necessary lifting devices. The pump should be located as close as possible to the liquid
supply so that the suction line is short and direct. Location should require a minimum of elbows and
fittings in the discharge line to minimize friction losses. The unit should be protected against flooding.
3-2
Mounting:
The pump unit is designed to be installed in the pipeline. Standard piping supports on either side of the
pump should be used to eliminate pipe stresses.
3-3
Piping:
The suction and discharge pipes must be in line, and the pump must not be used to pull the piping into
place by tightening the flange bolts. Pipes should be supported near the pump.
3-4
Wiring and Controls:
The electric motor power supply connections mush conform to national and local codes. The
motor ratings stamped on the motor nameplate must match the line voltage and wire capacity.
DO
NOT USE ANY OTHER VOLTAGE
SECTION IV
OPERATION
4-1
Starting:
Turn the pump shaft by hand to insure that the parts do not bind
Open the valve in the pump suction line, if fitted
Close discharge valve
Prime the pump in one of the following ways:
1.
If the pump operates under positive pressure, open vent valve on top of the pump casing. After
all entrained air has escaped, close the vent valves. Rotate the shaft, if possible, to allow any air
trapped in the impeller passages to escape.
2.
If the pump operates on a suction lift and a foot valve is included in the system, fill the pump and
the suction line with liquid from an outside source. Trapped air should be allowed to escape
through the vent valve while filling.