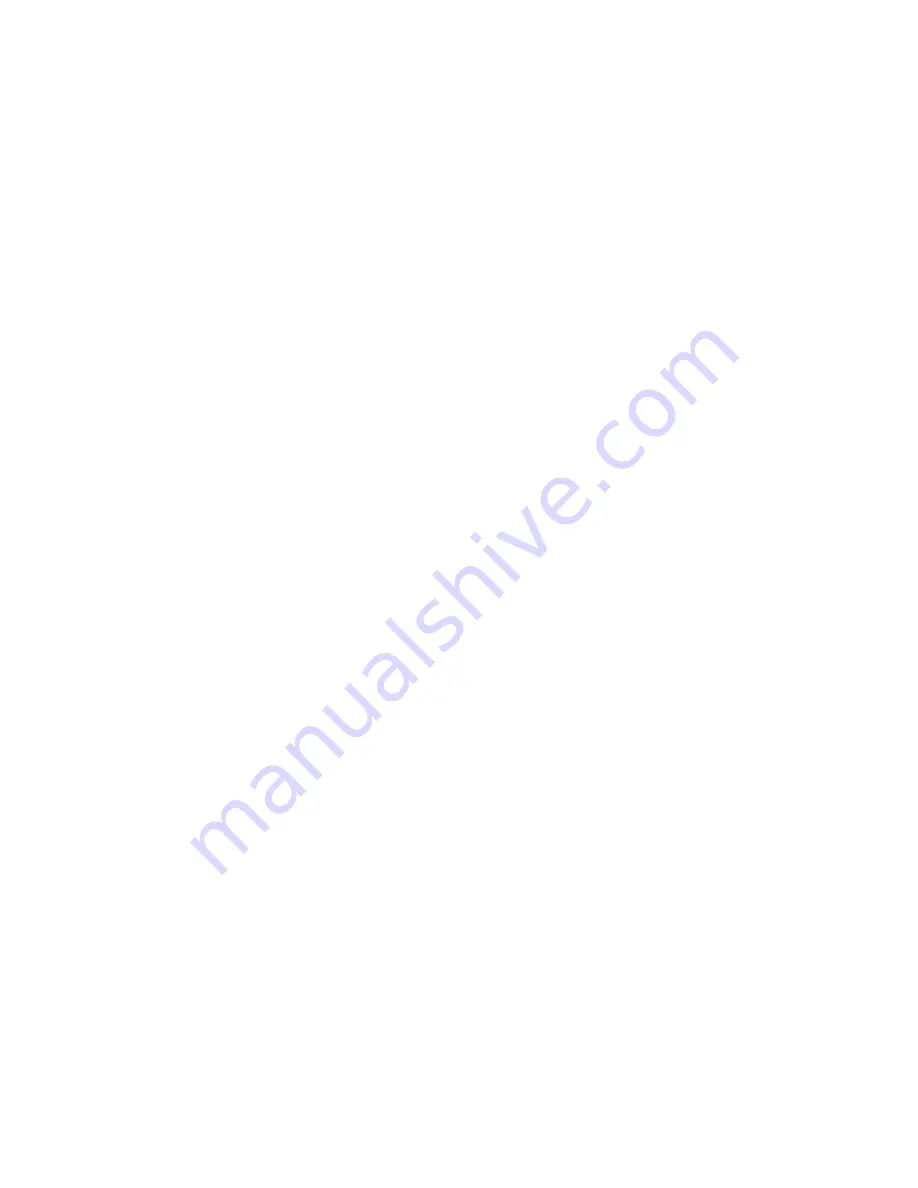
9
8.
Press the bearings (16 & 18) onto the shaft (6).
9.
Install the bearing spacer ring (78) into the outboard bearing cartridge (33) and the seal (89A) into the
inboard bearing cartridge (31).
10.
Install the cartridges (31 & 33) onto the bearings (16 & 18) and fasten them to the bearing covers (37).
11.
Install the dowel pins into the case rings (7) and slide onto the impeller (2).
12.
Lower the rotating element into the lower half casing (1A). Note: Align the grooves in the O.D. of the
cartridges (31 & 33) with the machined side of the casing. This centers the impeller in the volute. Align
the thru holes in the cartridges (31 & 33) and glands (17) with the holes in the casing (1A & 1B).
13.
Start the socket head cap screws to hold the glands (17) into the casing (1A & 1B) in the hole located at
bottom dead center. (There are drilled holes in the cartridges for access to these cap screws). Tighten
and then back off one half round.
14.
Before placing the parting flange gasket (73) into position, place a 1/8” tp 3/16” bead of
Permatex Ultra
Blue RTV Silicone Product No. 77B
or equivalent sealant on the parting flange inside the perimeter of
parting flange bolt locations and adjacent to the hydraulic passages.
15.
Place the parting flange gasket (73) into position onto the lower casing half (1A).
16.
Before placing the upper casing half (1B) into position, place a 1/8” to 3/16” (3 to 5 mm) bead of
Permatex Ultra Blue RTV Silicone Product No. 77B
or equivalent sealant on top of the parting flange
gasket inside the perimeter of parting flange bolt locations and adjacent to the hydraulic passages
17.
Lower the upper half casing (1B) into position. Install alignment pins at the casing parting flange joint.
18.
Install and tighten all three screws in each gland (17).
19.
Install case parting flange bolts and tighten.
20.
Install bearing caps. Insert alignment pins into bearing cartridges (31 & 33). (Drill cartridges for pins if
new.)
21.
Torque all parting flange bolts, including the bearing cap bolts using the following appropriate dry torque
values according to the bolt size:
½” – 75 to 90 ft-lbs (10 to 13 kgf-m)
5/8” – 150 to 180 ft-lbs (21 to 25 kgf-m)
¾” – 260 to 300 ft-lbs (36 to 42 kgf-m)
22.
Install all fittings and tubing that were removed.
23.
Rotate by hand to insure that the parts do not bind.
LOCATING OPERATING DIFFICULTIES
In the majority of cases, operating difficulties are external to the pump and the following causes should be
carefully investigated before undertaking repairs:
No Water Delivered
Pump not primed – indicated by no pressure on discharge.
Summary of Contents for HSC
Page 15: ......
Page 16: ...13 Notes ...