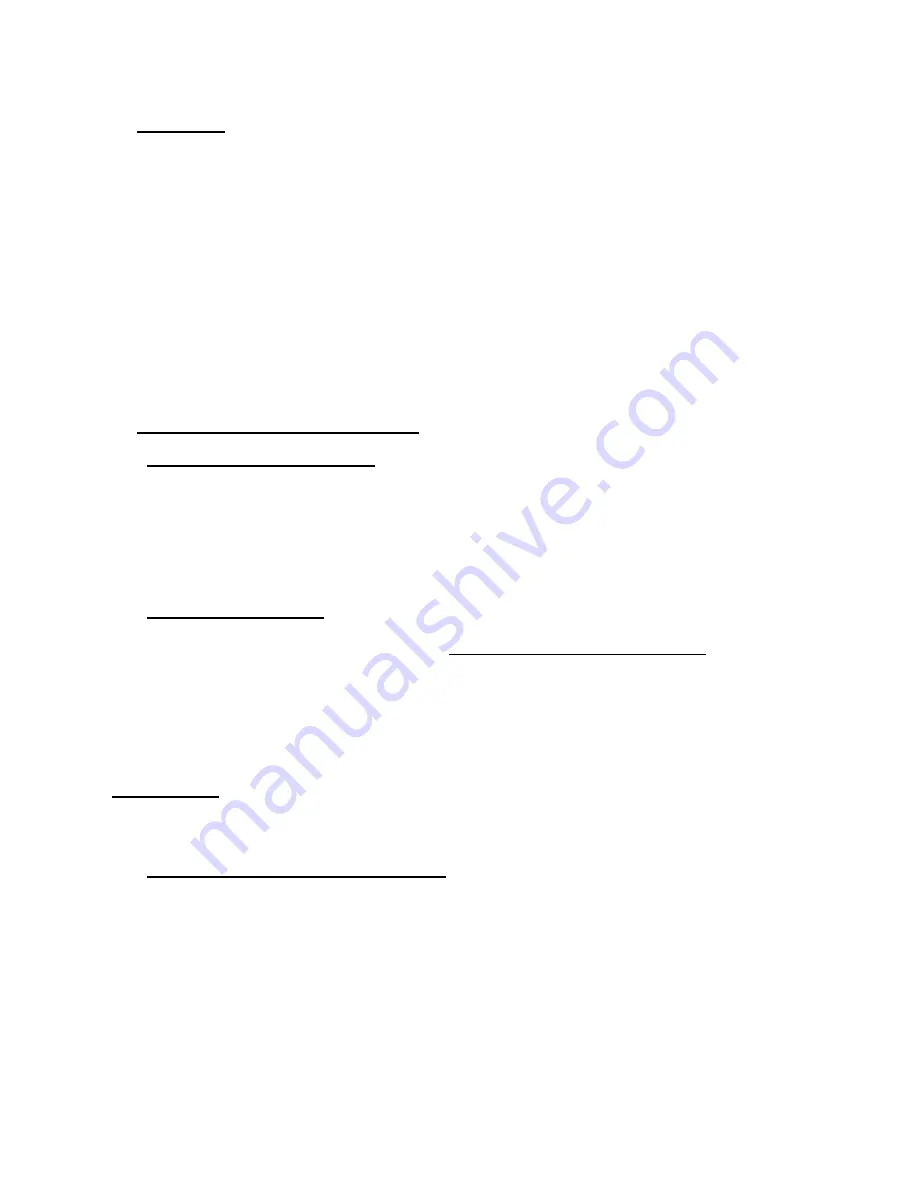
GP-M230-BX-010A
2300 / IO 210 Manual
RD: June 2006
R.L. 10A
KH
1. GENERAL
2. INSTALLATION REQUIREMENTS
2.1 MOUNTING CLEARANCES
Series 2300 / IO 210 Heaters must be mounted with minimum clearances as shown in Section
8.4. It should also be located with respect to building construction and equipment so as to pro-
vide sufficient clearance and accessibility for servicing and cleaning of burners and ignition
control. Minimum mounting height is to be no less than 96”. Do not store or place anything di-
rectly underneath heater
2.2 HEATER MOUNTING
IMPORTANT:
For either horizontal or angle mounting, the long axis of the heater must be
level. Use only non-combustible mounting hardware. Diagram 2 on Page 5 illustrates typical
suspension hardware that may be used., and provided by Schwank as an optional component.
2.3 GAS SUPPLY LINE INSTALLATION
•
All piping must be installed according to local codes.
•
An approved flexible connector between the heater and gas piping must be installed. The
same is available as an option from Schwank.
•
A drip-pocket at the inlet connection must be provided.
•
On propane-fired units, a main line filter is recommended.
•
Piping joint compounds must be resistant to the action of liquefied petroleum gases.
•
All piping joints should be tested for leaks with a soap and water solution.
Page 1
Series 2300 / IO 210 Heaters are approved for both horizontal and angle mounting. When angle
mounting, the short axis may be rotated to a maximum of 45°; however this may direct a large
portion of infrared heat above the heads of seated occupants in many applications.
Schwank recommends a 30° mounting angle in most applications. Refer to Diagram 8. Im-
proper angle mounting can result in damage to the heater or unsafe operation, and will void
warranty.
The gas fired infra-red combined intensity heaters are suitable to be installed for heating of out-
door and non residential indoor spaces. These installation instructions are intended for the Se-
ries 2300 / IO 210 Heaters.
All installations must conform to the following:, all local and national code requirements in-
cluding the current CAN/CGA-B149.1 installation code for gas burning appliances and equip-
ment as well as the Canadian Electrical Code PART 1 CSAC22.1 (latest edition) must be ob-
served. All installations in the U.S.A. must conform to local and national code requirements
including, National Fuel Gas code ANSI Z223.1, and the National Electrical Code ANSI/NFPA
No 70 (latest edition). Due to ever changing standards and requirements, revision to equipment
and installation procedures may be necessary. In case of discrepancies, the latest installation
manual will take priority.