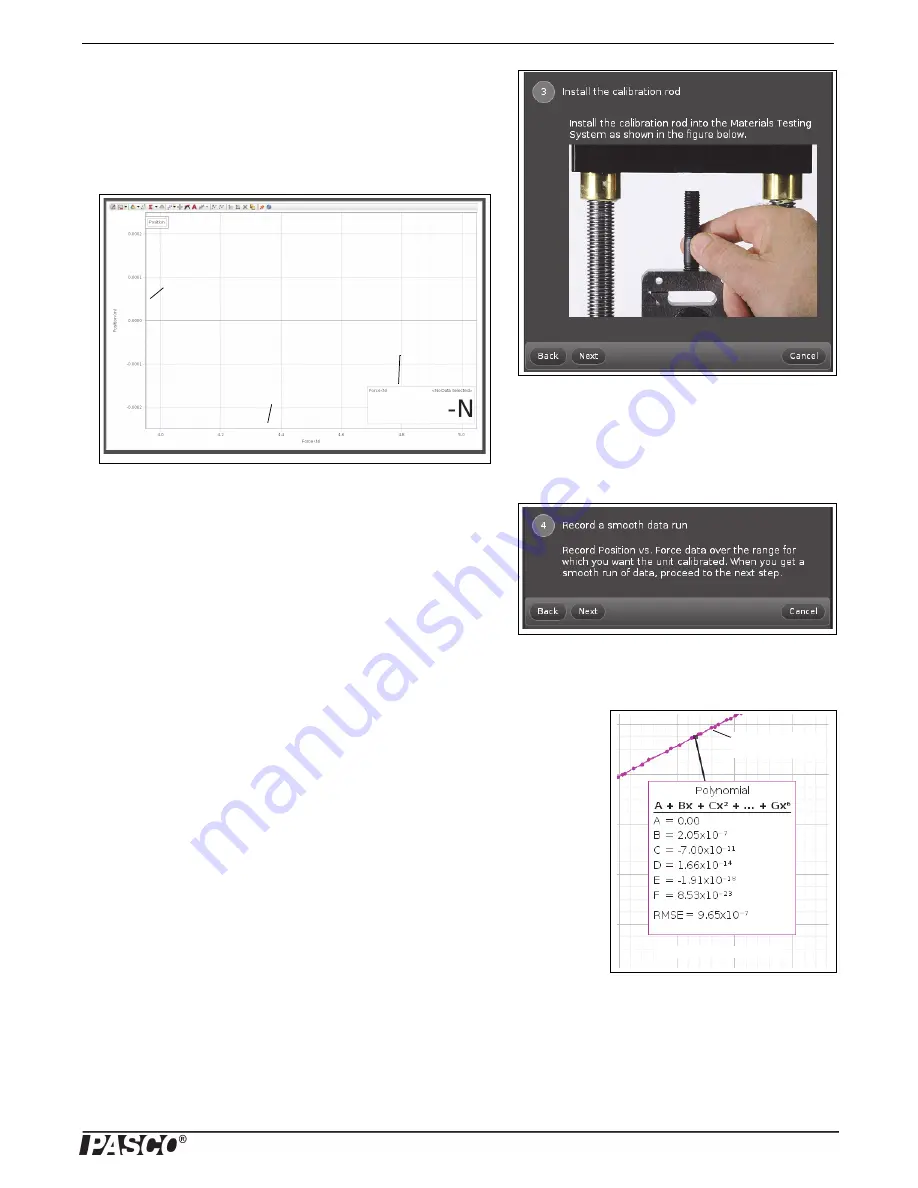
Model No.ME-8236
Appendix A: Calibration
15
012-13762D
Step Three: Install the Calibration Rod
The ‘calibration wizard” changes to show an illustration about how to
install the calibration rod.
In addition to the illustration, a Graph display of Position (m) versus
Force (N) opens. A Digits display of Force (N) is part of the Graph dis-
play.
•
Click
Next
to show Step Four: “Record a smooth data run”.
Step Four: Record a Smooth Data Run
NOTE: To make a calibration that will accurately correct for compli-
ance, it is necessary to calibrate the Materials Testing Machine over the
same range of force and the same conditions you expect to use when
you are testing your samples.
•
Click
Record
and collect a smooth run of position versus force
data.
•
When the data collection is finished, click
Stop
.
REMINDER: If the run of data is not smooth, delete the run and try again.
NOTE: A Polynomial curve fit is automatically applied to the run of position versus
force data.
•
Click
Next
to open Step Five, “Polynomial Fit”.
Position (m)
Force (N)
Digits display of
Force (N)
Position versus
force data
Polynomial curve fit