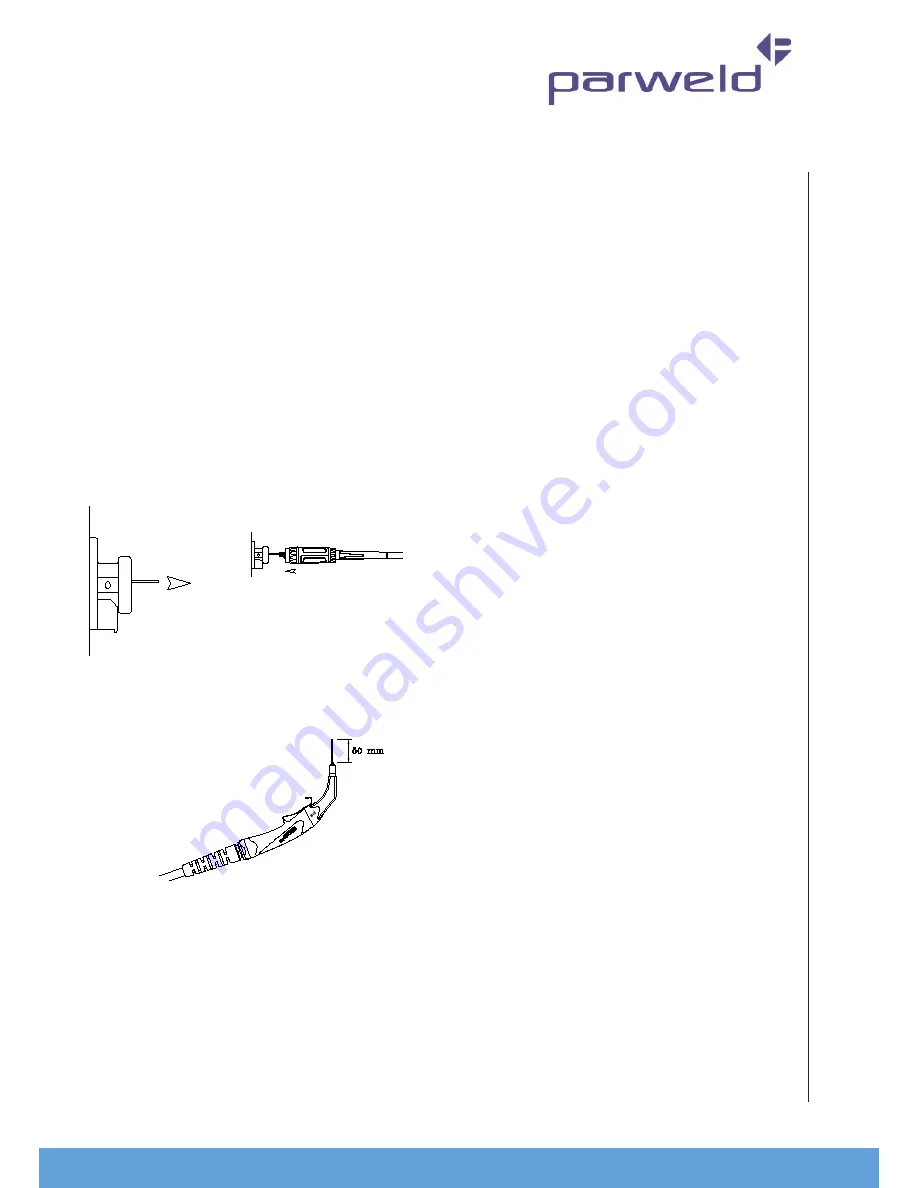
www.parweld.com
9
1.
T
urn off the power source.
2. Release the pressure on the idle rolls by swinging
the adjustable pressure arm down. Lift the cast
idle roll assembly and allow it to sit in an upright
position.
3. Unscrew the plastic knob retaining the lower
grooved drive roll and side off the drive roller.
4. Ensure the wire size marked on the side of the
feed roller matches the wire size to be used.
5. Replace the drive rolls in reverse of the above
procedure ensuring the wire size to be used is
marked on the outward facing side of the roller as
it is refitted.
Fig 1
Fig 2
x
it securely into the top of the machine. Lift the wire
feeder up onto the power source and locate the post
into the tube on the underside of the wire feeder
taking care to ensure it is fully located on the post.
Connection of the interconnect cable.
Working at the wire feeder end insert the Dinse power
connector and twist it to lock it securely. Connect the
gas hose to the inlet on the rear of the wire feeder
followed by the 4 pin plug taking care to align the pins
before inserting the plug.
At the power source end connect the Dinse socket and
twist to secure, connect the 5 pin control socket taking
care to align the pins before inserting the plug. The
gas hose should be lead off to the outlet connection of
the gas regulator.
5.5 Output Polarity Connections
The welder, as shipped from the factory, is connected
for electrode positive (+) polarity. This is the normal
polarity for MIG welding.
5.6 Changing drive roll sets
NOTE: Be sure that the torch liner and contact tip are
also sized to match the selected wire size.
5.7 Welding wire installation
1. Open the Wire drum cover by pulling down and
out on the bottom of the cover
2. Unscrew the plastic retaining wheel from the end
of the spool holder shaft.
3. Position the wire spool so that it will rotate in a
direction when feeding so as to be de-reeled from
the bottom of the coil.
4. Slide the wire spool all the way onto the shaft and
refit the plastic retaining nut.
Note:- There is a friction brake on the reel hub
assembly to prevent the wire spool over running
when welding stops ensure the this is slackened to the
minimum setting. It can be adjusted by means of the
nut visible when the plastic nut is removed.
5. Turn the Spool until the free end of the electrode
is accessible. While securely holding the
electrode, cut off the bent end and straighten the
first six inches. (If the electrode is not properly
straightened, it may not feed properly through the
wire drive system Manually feed the wire from
the wire reel and through the wire guide and then
over the top of the wire feed rollers (ensure the
pressure arms are in the raised position.)
6. Continue to feed the wire through the outlet
guide until 20mm of wire is protruding from the
front of the machine torch connector.
7. Reposition the adjustable pressure arms to
there original position to apply pressure. Adjust
pressure as necessary.
Note the pressure arm should be adjusted in order to
give the minimum amount of pressure on the wire to
allow reliable feeding,
5.8 torch installation
Your Parweld MIG/MAG Welding Torch has been
supplied ready to weld. It has been supplied with
the standard consumables denoted in the product
brochure.
To connect the torch to the power source:-
1. Remove the tip adaptor and contact tip
2. Inch the wire from the exit of the wire guide on
the feed unit as Figure 1. Ensure that it does not
short out on any machine panels.
3. Carefully slide the electrode wire into the torch
liner and slowly locate the torch gun plug body
into the feed unit central connector and tighten
the gun plug nut as Figure 2
Note; To aid the initial location of a new torch and to
prevent damage to the gas nipple O-ring a very light
application of grease to the O Ring is beneficial.
4. Keeping the torch as straight as possible, use the
power source inch facility or torch trigger to feed
the electrode wire 50mm from the end of the liner
conduit.
5. Once the electrode wire has stopped, refit the tip
adaptor, diffuser, contact tip and gas nozzle.