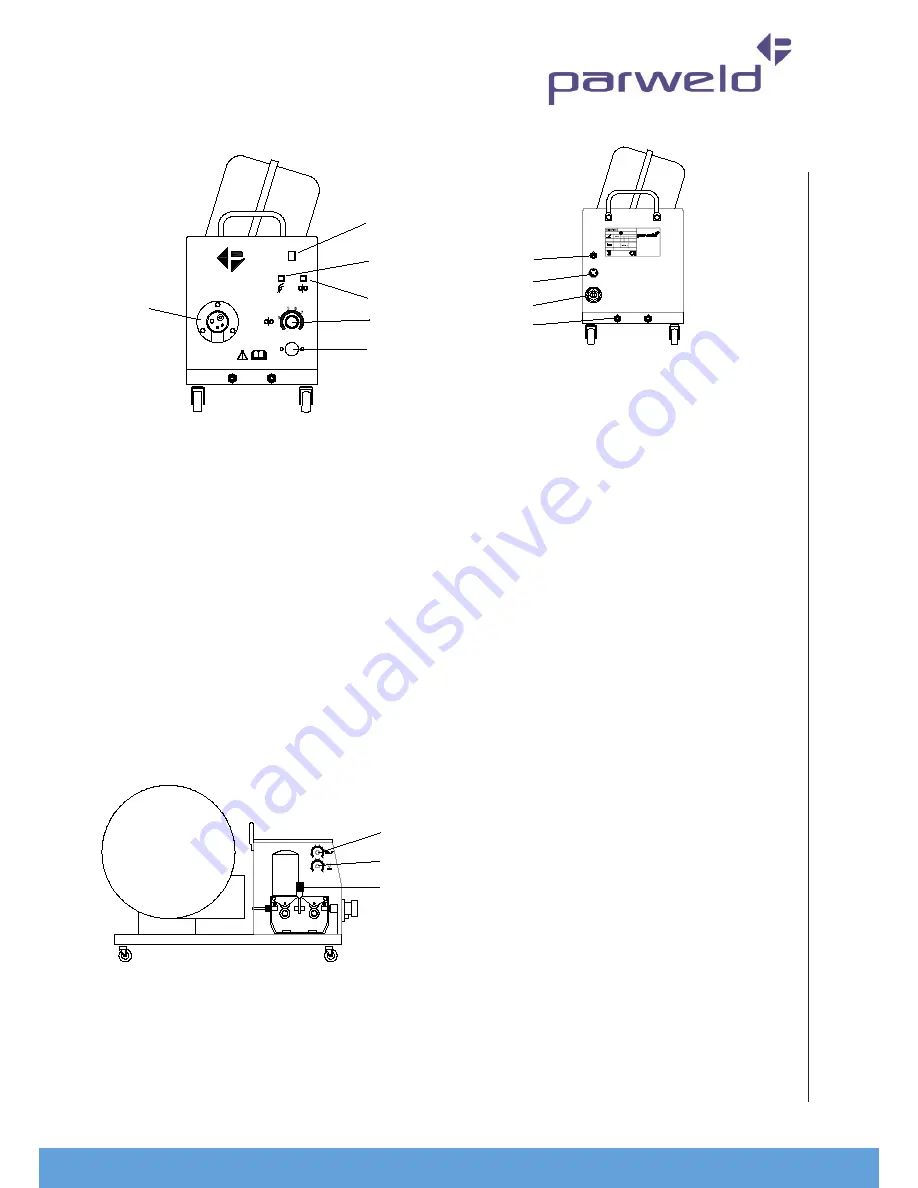
www.parweld.com
XTM WF100
4T
2T
10
8
9
2
1
4
PUSH PULL
CONTROL 42V
16
17
18
19
20
21
7
4.0 Description of controls
1. Digital display for amperage and Voltage
(displayed real time)
2. Fault light This light will illuminate when a fault or
over temperature condition has occurred. If this
light illuminates allow the machine to cool with
the fan still running until it extinguished. If the
light does not go off when the power source has
cooled down then have the machine checked by a
qualified engineer.
3. Mains input light This light illuminates when the
mains power is connected and the machine is
switched on.
4. On Off switch. The machine is switched off when
the light (4) is off and the fan is not running.
5. Coarse Voltage selector switch. This switch is used
to select the require welding voltage each position
of the switch represents approximately 4V.
Do Not operate this switch while welding
6. Fine Voltage selector switch. This switch is used to
select the require welding voltage each position of
the switch represents approximately 0.5V.
Do Not operate this switch while welding
7. Work return lead connection. This socket allows
connection of the work return lead to the front of
the machine.
Note the XTM403S has 2 sockets for the work return
lead please refer below
8. Work return lead connection. High inductance
connection, this should be used when in spray
transfer mode to give a more stable arc. (Only
fitted to XTM403S)
9. Mains input connection Input connection for the
pre-installed mains cable
10. Control circuit protection fuse.
11. Gas cylinder retention chain to be used when a
gas cylinder is mounted on the rear tray.
12. Auxiliary output. 240V 3A auxiliary output for use
with water cooler or small power tools.
13. Protection fuse for the Auxiliary output
14. Socket for the interconnection cable to link to the
wire feeder.
15. Welding power connection to connect to the inter
connect cable.
16. 2T 4T, when in the 2T position the torch trigger
will have a momentary operation ie the welding
operation will start when the rigger is depressed
and stop when it is released. In the 4T position a
short press and release of the trigger will start the
welding operation and a short press and release
with stop the operation. The 4T mode is ideal for
long welds as it reduces operator fatigue.
17. Gas purge button. Pressing this button allow gas
to flow through the welding torch and so allow
checking of the gas flow before starting the
welding process.
18. Wire inching button, allows the welding wire to
be fed through the torch without engergising the
welding power.
19. Wire feed speed adjustment, controls the speed of
wire feeding from 0.8 to 24 m/min. Increasing the
wire feed speed also has the effect of increasing
the welding current
20. Location for control socket if machine is fitted with
Push Pull torch
21. Torch connector The Euro connector provided the
external connection for the welding torch
9
4
3
9
4
3
22
23
24
60A/ 17V to 350A/ 31.5V
X
60%
100%
1 ~50 Hz
U
1
= 42V
IP 21S
Rohs Compliant
ENGLAND.
DY12 2TZ,
WORCESTERSHIRE,
LONG BANK BEWDLEY,
BEWDLEY BUSINESS PARK,
PARWELD LTD,
S No.
ISO/ IEC 60974-1
I
2
500A
350A
M
I
1
eff = A
WIRE FEEDER
CONTROL
INTERCONNECTING
CABLE
GAS INPUT
25
26
27
27