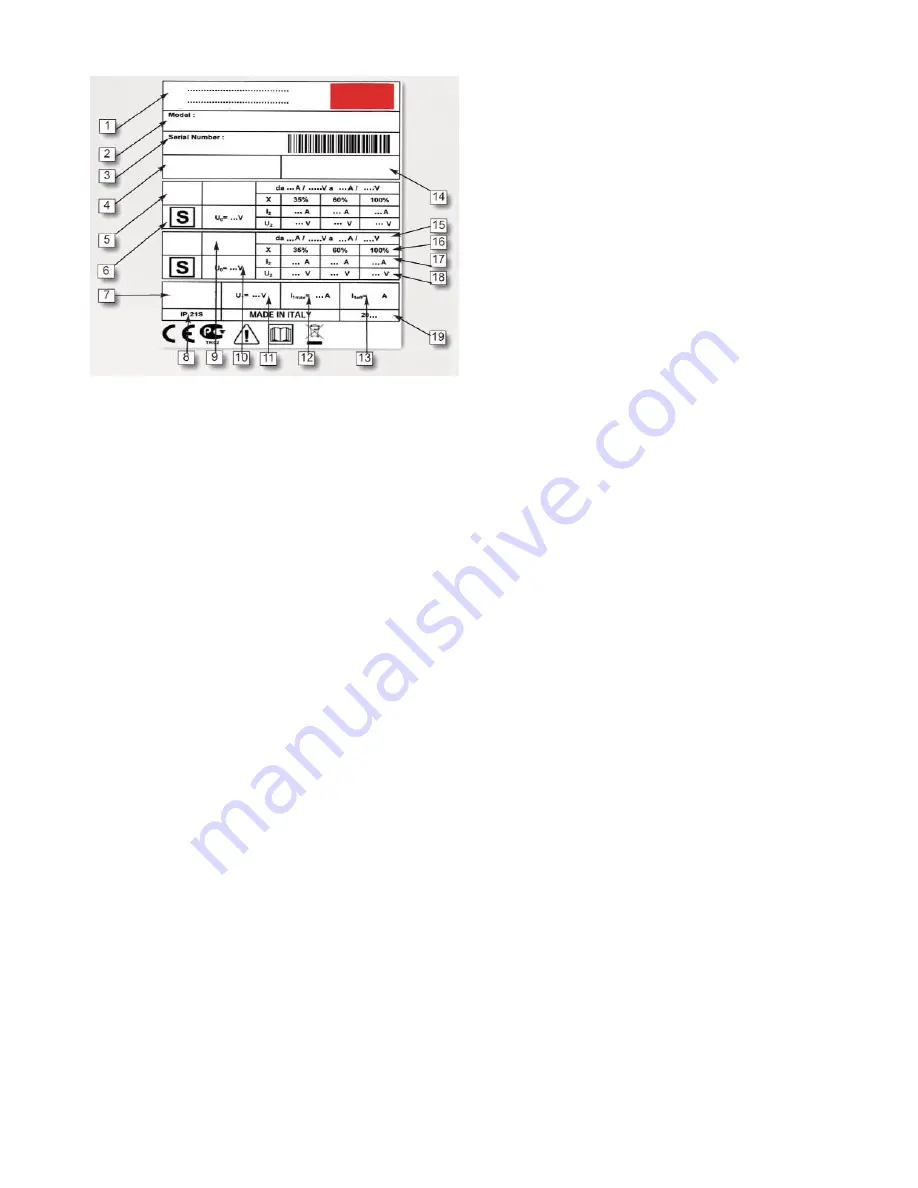
DATA PLATE
1. MANUFACTURER’S NAME, ADRESS AND COMPANY LOGO
2. MODEL
3. SERIAL NUMBER
4. BLOCK DIAGRAM
5. WELDING OUTPUT
6. SUITABLE FOR ENVIRONMENT WITH INCREASED HAZARD OF
ELECTRIC SHOCK
7. POWER SUPPLY
8. DEGREE OF PROTECTION
9. TYPE OF WELDING OUTPUT CURRENT
10. INPUT VOLTAGE
11. RATED INPUT VOLTAGE
12. MAXIMUM RATED INPUT CURRENT
13. MAXIMUM EFFECTIVE INPUT CURRENT
14. APPLICABLE STANDARDS
15. RANGE OF WELDING VOLTAGE-CURRENT
16. DUTY CYCLE
17. RATED WELDING CURRENT
18. CONVENTIONAL LOAD VOLTAGE
19. YEAR OF CONSTRUCTION
CONSTRUCTION SPECIFICATIONS:
WEIGHT [Kg]: 23
Dimensions:
Width [mm]: 220
Depth [mm]: 560
Height [mm]: 480
Protection rating: IP 21S
Height S.L.M. [m]: 1000
Usage temp. [°C]: -10/+40
Storage temp. [°C]: -20/+55 T
est temp. [°C]: 40
Applicable standards: EN.60974-1 EN.60974-10
Group/Class: Gruppo 2 Classe A
Thermal protection: Termostato Incorporato
ELECTRICAL INPUT :
Line voltage: 230
No. phases: 1
Frequency [Hz]: 50/60
Effective line current [A]: 21,6
Maximum line current [A]: 40,3
Input Power [kVA]: 5
Circuit protection: Time-delay fuses or Co K magnetothermal curve
OUT-PUT CHARACTERISTICS:
Static characteristics: Cadente
Fill Diameter: 0.6-0.8-1.0-1.2
Welding mode: MIG/MAG
Weld current range: from 15A / 14,75V to 235A / 25,75V
Open circuit voltage [V]: 55
Output current and tension: Duty [%]: 35 60 100
I2 [A]: 220 160 130
U2 [V]: 25 22 20,5
Welding mode: TIG
Weld current range: from 15A / 10,6V to 235A / 19,4V
Open circuit voltage [V]: 55
Out-put current and tension: Duty [%]: 35 60 100
I2 [A]: 220 160 130
U2 [V]: 18,8 16,4 15,2
Welding mode: MMA
Weld current range: from 15A / 10,6V to 185A / 17,4V Open circuit voltage [V]: 55
Duty [%]: 35 60 100
I2 [A]: 185 138 109
U2 [V]: 27,4 25,52 24,36 6 1.