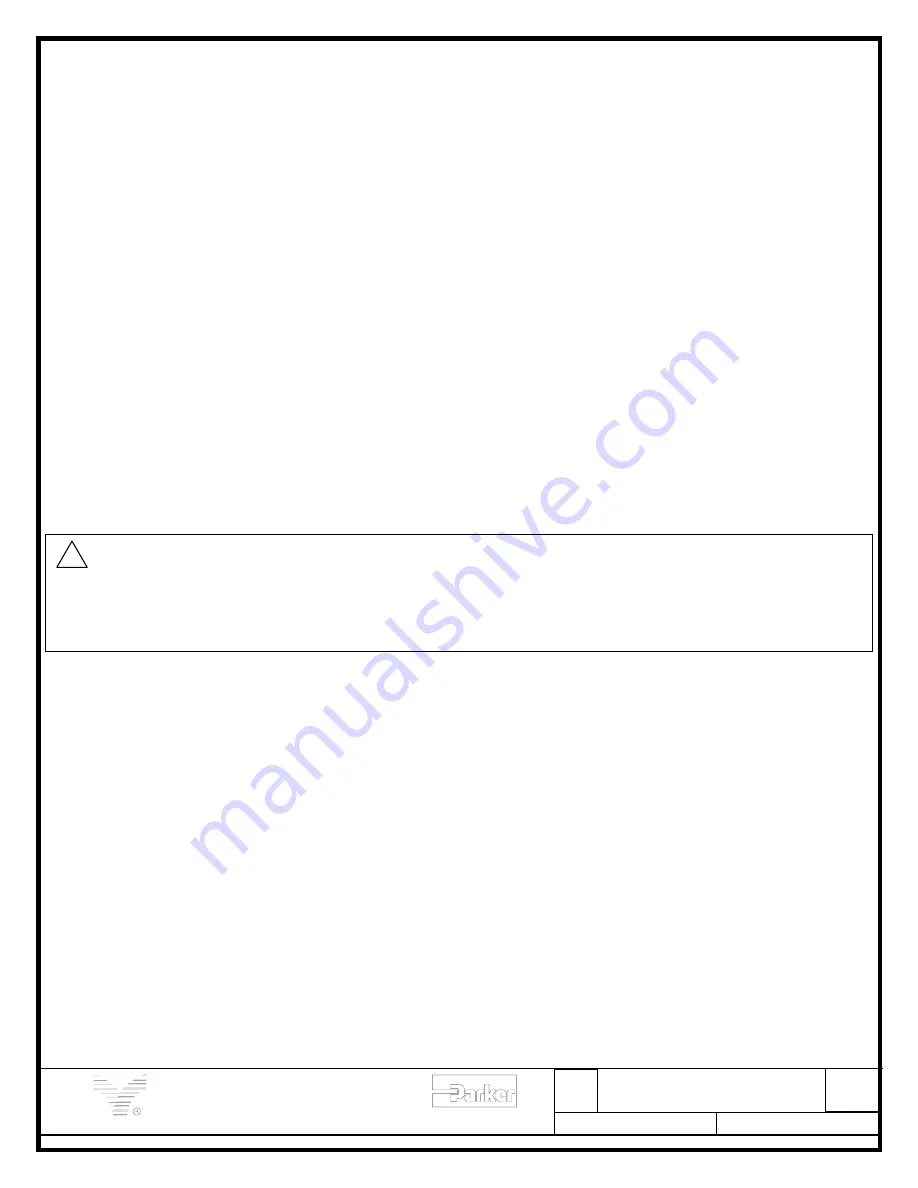
PART NUMBER
54099314
PARKER HANNIFIN CORPORATION
VERIFLO DIVISION
250 CANAL BOULEVARD, P.O. BOX 4034
RICHMOND, CA 94804-0034
INSTRUMENTATION
SCALE: --------
REV.
-
A
SHEET
3
of
3
VERIFLO
Example: SPE coefficient = 1 psig per 100 psig
Starting supply pressure = 500 psig
Final supply pressure = 100 psig
Delivery Pressure decrease= SPE x (
Starting
Supply
Pressure – Final S
upply
Pressure
)
= 1x (500-100)= 4 psi
SPECIAL INSTRUCTIONS
Preset Regulators:
Preset regulators do not have an adjusting knob and are set at the factory to provide a specified
delivery pressure. When pressure is applied to the inlet of the preset regulator, the delivery pressure may exceed the
specified delivery pressure if the system is not flowing gas. The downstream system must be flowing or vented to reduce
the pressure to the preset delivery pressure.
Dome Operated Regulators:
Dome operated regulators do not have an adjusting knob. Regulator delivery pressure is
controlled by supplying air or nitrogen gas pressure to the 1/8” NPT port in the regulator cap. Delivery pressure is
increased as dome pressure is increased and decreased as dome pressure is decreased. If gas is not flowing it will be
necessary to vent the downstream system to reduce the pressure. When using dome operated regulators adhere to the
following precaution:
do not allow the dome pressure to exceed 210 psig.
MAINTENANCE
IMPROPER REPAIR OR SERVICING OF THIS PRODUCT CAN CAUSE DEATH, PERSONAL INJURY AND PROPERTY DAMAGE.
Veriflo Division products must pass rigid acceptance tests before leaving the factory. All repairs and servicing of this product must only be performed by
factory certified personnel and tested for operation and leakage. Veriflo Division cannot assume responsibility for the performance or safety of a
customer repaired or serviced product or for any damages resulting from failure of a customer repaired or serviced product or otherwise altered product.
Maintenance:
A pressure regulator should be checked periodically for proper and safe operation. A pressure regulator
should also be checked after cylinder changes or system maintenance. The user is solely responsible for ensuring that
the recommended checks can be safely performed and are adequate to ensure proper and safe operation of the user’s
system.
A regulator that does not comply with the recommended checks or malfunctions in any manner must be
immediately removed from service. Do not attempt to repair the regulator.
Check for regulator seat leak. Fully close the regulator by turning the adjusting knob counter clockwise until the stop is
reached. Apply pressure to the regulator inlet. Close the upstream supply valve. Monitor the pressure between the
supply valve and the regulator for 5 minutes. The pressure should not decrease.
Check flow shutoff. Confirm after flow is stopped, that delivery pressure does not exceed the regulator’s maximum
outlet pressure.
Check the regulator function. Confirm delivery pressure increases when the adjusting knob is turned clockwise or
dome pressure increased, and decreases when turned counter clockwise or dome pressure decreased.
Check for leaks to atmosphere. There should be no leaks to atmosphere. Use a leak test method compatible with your
system.
Removing a regulator from service:
Follow your system safety and maintenance procedures when removing a
regulator from service. Before removing the regulator, the user must:
Isolate the regulator from all pressure sources upstream and downstream of the regulator by closing the appropriate
valves.
Lockout valves and other system equipment as required.
Properly purge hazardous gases from the regulator.
Vent all pressure in the regulator.
!
WARNING