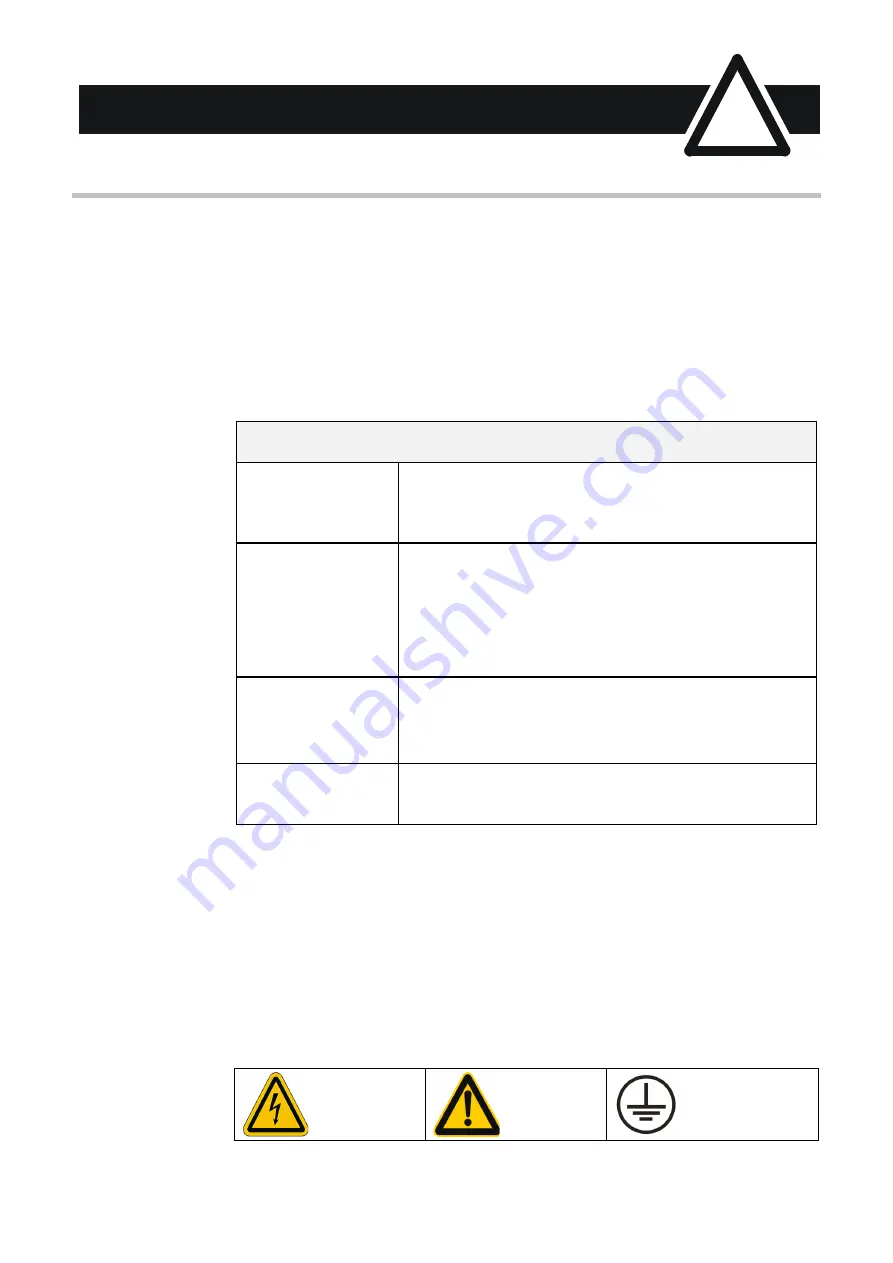
Cont.3
Requirements
IMPORTANT:
Please read this information BEFORE installing the equipment.
Intended Users
This manual is to be made available to all persons who are required to install, configure or
service equipment described herein, or any other associated operation.
The information given is intended to highlight safety issues, EMC considerations, and to enable
the user to obtain maximum benefit from the equipment.
Complete the following table for future reference detailing how the unit is to be installed and
used.
INSTALLATION DETAILS
Model Number
(see product label)
Where installed
(for your own
information)
Unit used as a:
(refer to Certification
for the Inverter)
ο
Component
ο
Relevant Apparatus
Unit fitted:
ο
Wall-mounted
ο
Enclosure
Application Area
The equipment described is intended for industrial motor speed control utilising DC motors, AC
induction or AC synchronous machines
Personnel
Installation, operation and maintenance of the equipment should be carried out by qualified
personnel. A qualified person is someone who is technically competent and familiar with all
safety information and established safety practices; with the installation process, operation and
maintenance of this equipment; and with all the hazards involved.
Product Warnings
Caution
Risk of electric
shock
Caution
Refer to
documentation
Earth/Ground
Protective
Conductor
Terminal
Safety Information
!
Summary of Contents for Siemens APOGEE P1
Page 6: ......