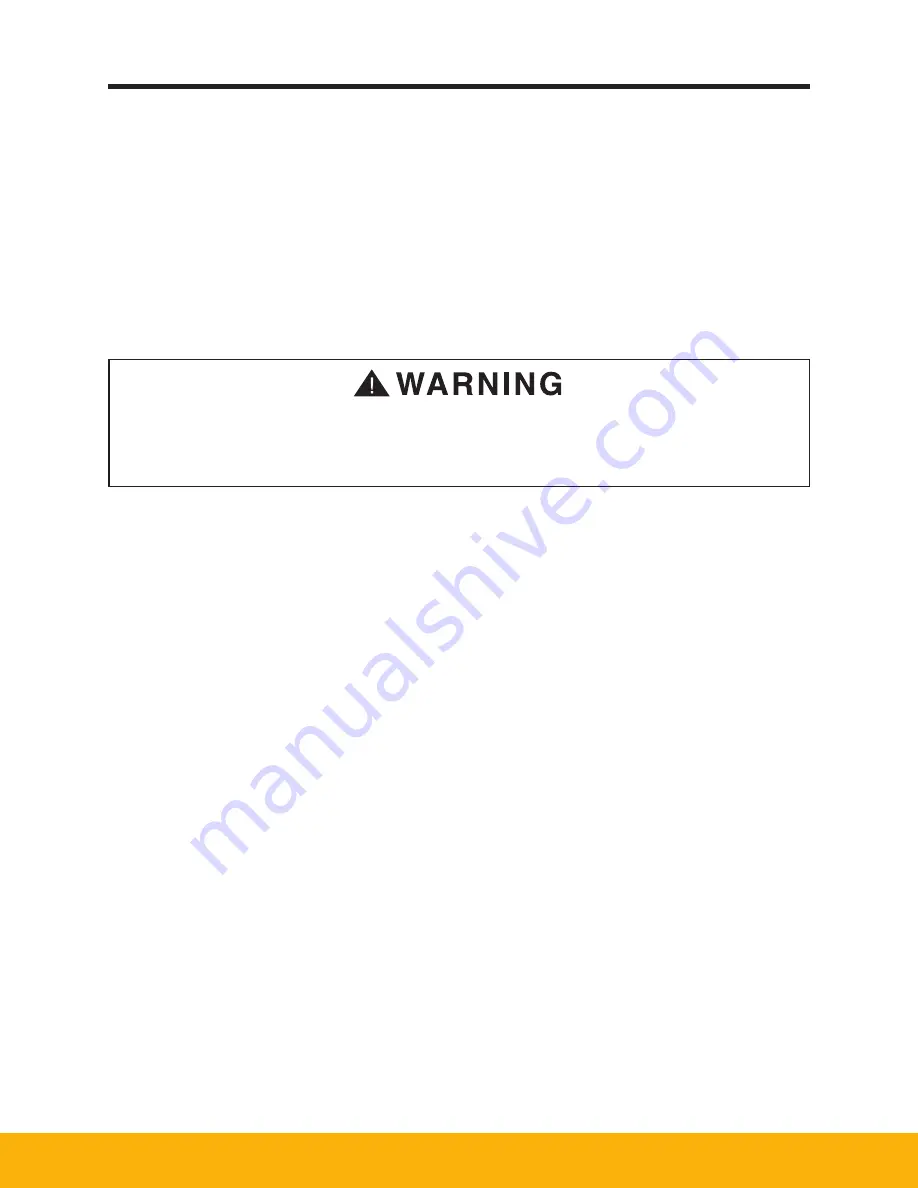
Shaker Dust Collector
SDC Series
11
3.3 Electrical Installation
ELECTRICAL SHOCK HAZARD
All electrical work should be performed by a qualified electrician in accordance with local electrical codes.
Disconnect electrical power before installing or servicing any electrical component.
General
Several types of standard electrical components can be installed to control and monitor your dust
collection equipment. A properly sized fused disconnect or circuit breaker should be installed to
adequately protect the equipment. Refer back to the nameplate on the SDC unit or control enclosure
to verify the control configuration purchased with your unit for proper sizing. Refer to Figures 8-11
(pg 10-14).
3.3.1 Mounting of the Controls
The control enclosure require access at the beginning and end of every shift of operation.
Location should be in a convenient, accessible area. The Parker control enclosure contains
the motor starters for both the blower and shaker motors.
It is recommended that the controls be mounted on a wall or pedestal subject to minimal vibration and
electrical noise. It is also suggested that the unit be located in a convenient location with the controls
as to allow the customer easier access to wire to the unit blower and shaker motors.
3.2.4 Filter Module Assembly
Prior to mounting the filter module to the hopper assembly, apply two ribbons of sealant to the hopper
flange to create a figure “8” pattern around the mounting holes. This technique is shown in Figure 4
-Detail A (pg. 6).
Place the filter module onto the hopper assembly (as shown in Figure 4). Drift pins may be required for
aligning holes between the two assemblies.
With the filter module still supported, use hardware (refer to Figure 4) to bolt the hopper and filter
module together. Securely tighten all hardware at the filter module and hopper. Check leg assembly
sway braces (if applicable) to ensure they are tight.
Disconnect lifting slings and spreader bars used for installation.
3.4 Optional Equipment Assembly
3.4.1 Magnelic
®
Gage
Magnehlic
®
gage is used to monitor the pressure drop across the filter in your SDC unit. This helps you
to monitor the performance of your equipment and alerts you to when the filter requires replacement.
The SDC unit cabinet comes with two pre-drilled holes located on the left side of the cabinet for the
pressure taps and (4) dimples to locate and install the Magnehelic
®
gage. The holes are plugged when
unit is shipped. Remove the snap in plugs using a flat head screw-driver and install the (2) pressure taps
in the SDC panels. To tighten the pressure taps, access to the inside part of the cabinet is required.
Removal of the filter cassette will be necessary to complete this installation. Drill out the (4) locating
dimples (closest to the door side) to allow clearance for 1/4” supplied hardware (5/16 drill bit is
recommended). Access the inside of the cabinet to tighten down the bracket hardware.
Install the gage into the bracket using the supplied hardware.
After the pressure taps are installed, run 1/4” tubing from the SDC cabinet to the Magnehelic
®
gage
and connect to the dirty air side of the cabinet to the pressure port marked “High” and the clean air side
to the pressure port marked “Low”. Take care not to kink the tubing during installation.
Summary of Contents for SDC
Page 1: ...Shaker Dust Collector Owner s Manual Model SDC...
Page 6: ...Page intentionally left blank...
Page 8: ...Shaker Dust Collector SDC Series 4 Figure 1 Unit Operation...
Page 10: ...Shaker Dust Collector SDC Series 6 Figure 2 Installation Details 61 10074 1...
Page 14: ...Shaker Dust Collector SDC Series 10 Figure 7 SDC 840 1050 Hopper Assembly 61 10074 14...
Page 25: ...Shaker Dust Collector SDC Series 21 Figure 13 Replacement Parts DWG 61 10074 15...