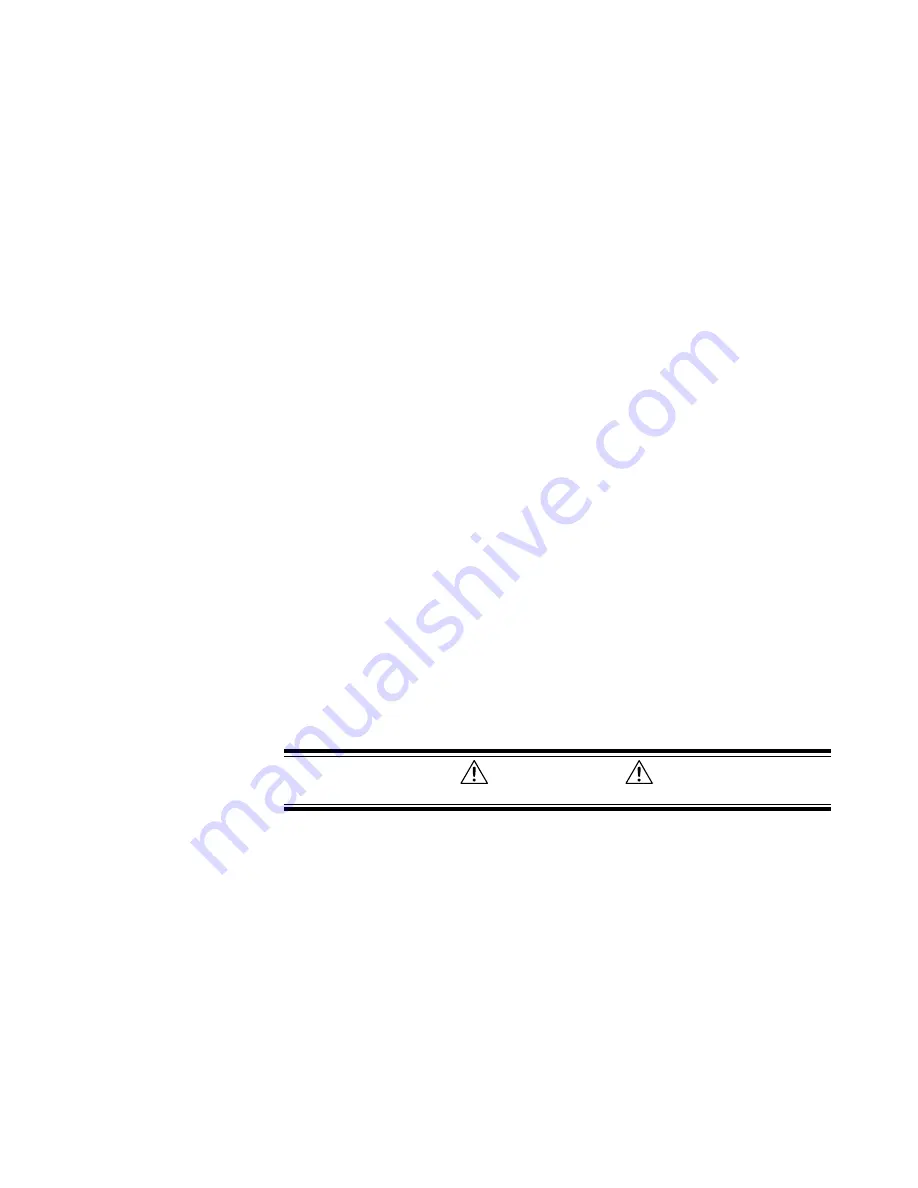
Chapter 2 – Installation
29
E-DC Hardware Installation Guide
(see resistor selection tables in the
Automatic Test
section). Next select R
S
,
the resistor in the same section of the table that is associated with your
desired standby current. Then use the following equation to find R
REMOTE
.
R
REMOTE
= -13,300 (3750 + R
C
) / (R
C
- R
S
)
R
C
= Resistor associated with the operating current
R
S
= Resistor associated with the desired standby current
F
AULT
O
UTPUT
The fault output is an open-collector, open emitter output from an ILD213
OPTO isolator. The output transistor will conduct when the drive is
functioning properly. The transistor will not conduct when any of the
following conditions exist.
•
No power is applied to the drive
•
There is insufficient voltage (<24VDC)
•
The drive detects a motor fault
•
The remote input is enabled
The fault output has the following electrical characteristics:
•
V
CEO
= 70VDC
•
V
CESAT
= 0.3VDC
•
Collector Current = 10 mA maximum (e.g. 2.4 K
Ω
at 24VDC)
•
Maximum Dissipation = 55 mW
G
EAR
S
HIFT
I
NPUT
The gear shift input is an optically isolated input. The GS+ terminal
(pin 11) is connected to the anode of the OPTO lead via a 681
Ω
current
limiting resistor. The GS- terminal (pin 23) is connected to the cathode of
the OPTO lead. The OPTO requires a minimum of 3.5 mA—
approximately
4.0 VDC
—to ensure proper system operation. This input may be differen-
tially driven.
CAUTION
Reverse voltage in excess of 6VDC may damage this device.
With no external current limiting resistor, the current is controlled by the
applied voltage. This is due to a fixed voltage drop of 1.5VDC on the opto
LED and the internal series resistor (681
Ω
).
The gear shift function allows a user with a limited frequency generator to
achieve higher velocities while using high resolution settings. The drive
multiplies each step pulse it receives by a factor of 8. This function may
be invoked
on-the-fly
; however, to prevent stalling and to keep track of
motor position, it should only be invoked when the motor is not moving.
Using the gear shift function is equivalent to changing drive resolution,
and may have an adverse effect on low speed performance (smoothness).
We recommend that you do not use the gear shift with resolution settings
less than 10,000 steps per revolution.
www.comoso.com
Summary of Contents for E-DC
Page 4: ...4 E DC Hardware Installation Guide www comoso com...
Page 8: ...8 E DC Hardware Installation Guide Chapter 1 Introduction www comoso com...
Page 46: ...46 E DC Hardware Installation Guide Chapter 3 Troubleshooting www comoso com...
Page 50: ...50 E DC Hardware Installation Guide Appendix A LVD Installation Instructions www comoso com...
Page 60: ...60 E DC Hardware Installation Guide Appendix B EMC Installation Guide www comoso com...