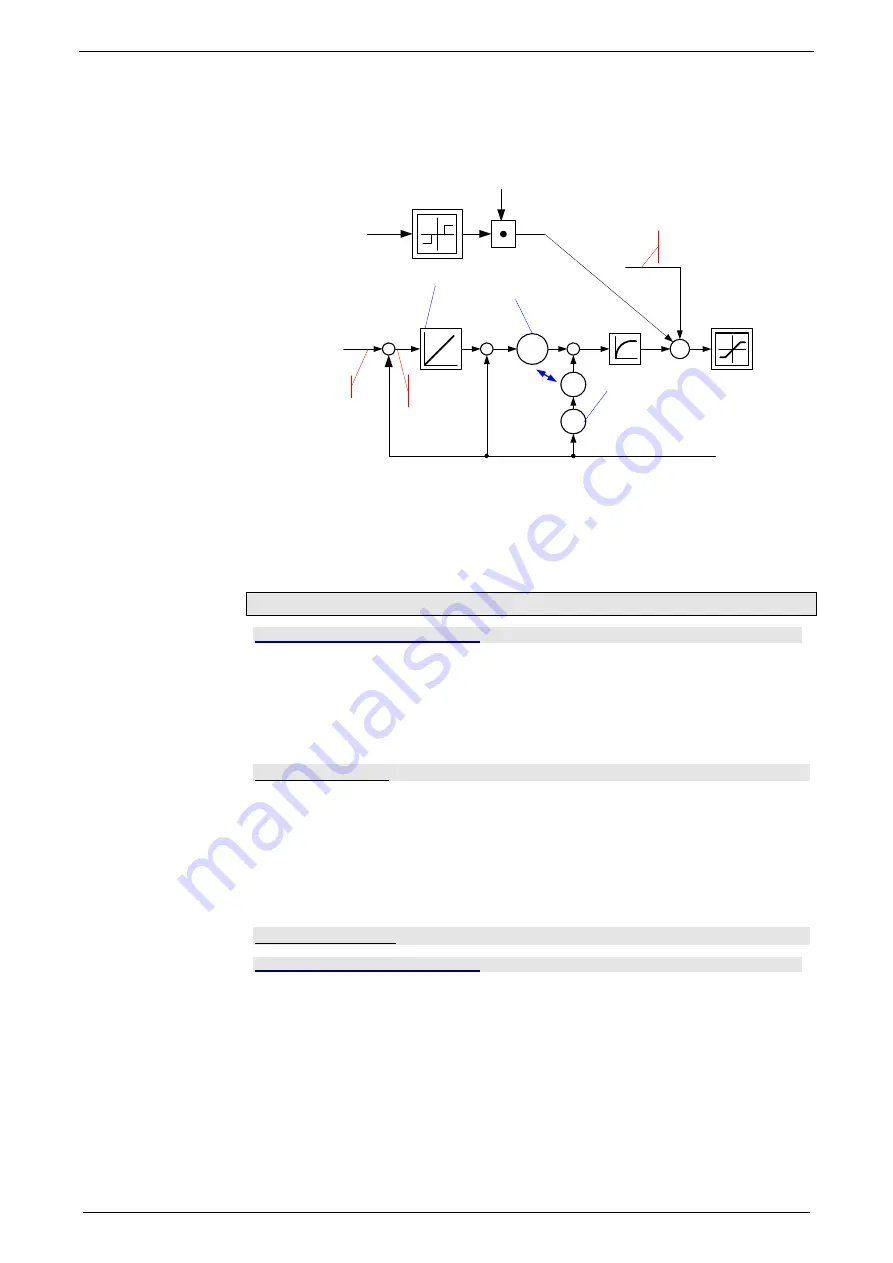
Parker EME
Setting up Compax3
192-120101 N11 C3I11T11 November 2007
173
Friction compensation
The activation of the friction compensation (end of the velocity loop)
K
I
pv
K
D
K
-
-
-
pv
K
T
681.6 Speed
Tracking error
2100.7 Velocity loop - "D" term
2100.2 Stiffness
2100.3 Damping
681.10 Setpoint Speed
688.14 Current &
jerk feed-forward RMS
f(n
SG
, n, O2200.24, Obj. 2200.20)
Filter tracking error
The friction compensation helps the control to surmount static friction at low
setpoint speeds. The non linear characteristic line is partly compensted by this and
a smaller deadband can be chosen, which will increase the position accuracy. The
amplitude of the friction compenstion depends on the application and must be
calculated if needed. If the value is set too high, corrective movements may result
and the tendency to oscillate is increased.
Commissioning window
In this chapter you can read about:
Load identification............................................................................................................................173
Setpoint generation..........................................................................................................................173
Commissioning window
With the aid of the setup window, the drive can be set up in a simple way.
Load identification
If you do not know the mass moment of inertia, it can be determined. For this, you
click on the corresponding button (see setup window no. 13). After the following
parameter entry, the identification can be started via the same button.
For more detailed information on the load identification, see the device help,
chapter "load identification".
This measurement requires the correct EMC or torque constant value Kt.
Setpoint generation
In this chapter you can read about:
Internal setpoint generation .............................................................................................................173
External setpoint generation ............................................................................................................175
The setpoints for the control loops are provided in two different ways - internally or
externally. The setpoint generation depends on the technology option of the device.
Internal setpoint generation
The internal setpoint generation can be used for the technology option s>T10. In
this case, the internal setpoint genertor generates the entire motion profile with
position, velocity, acceleration and jerk.