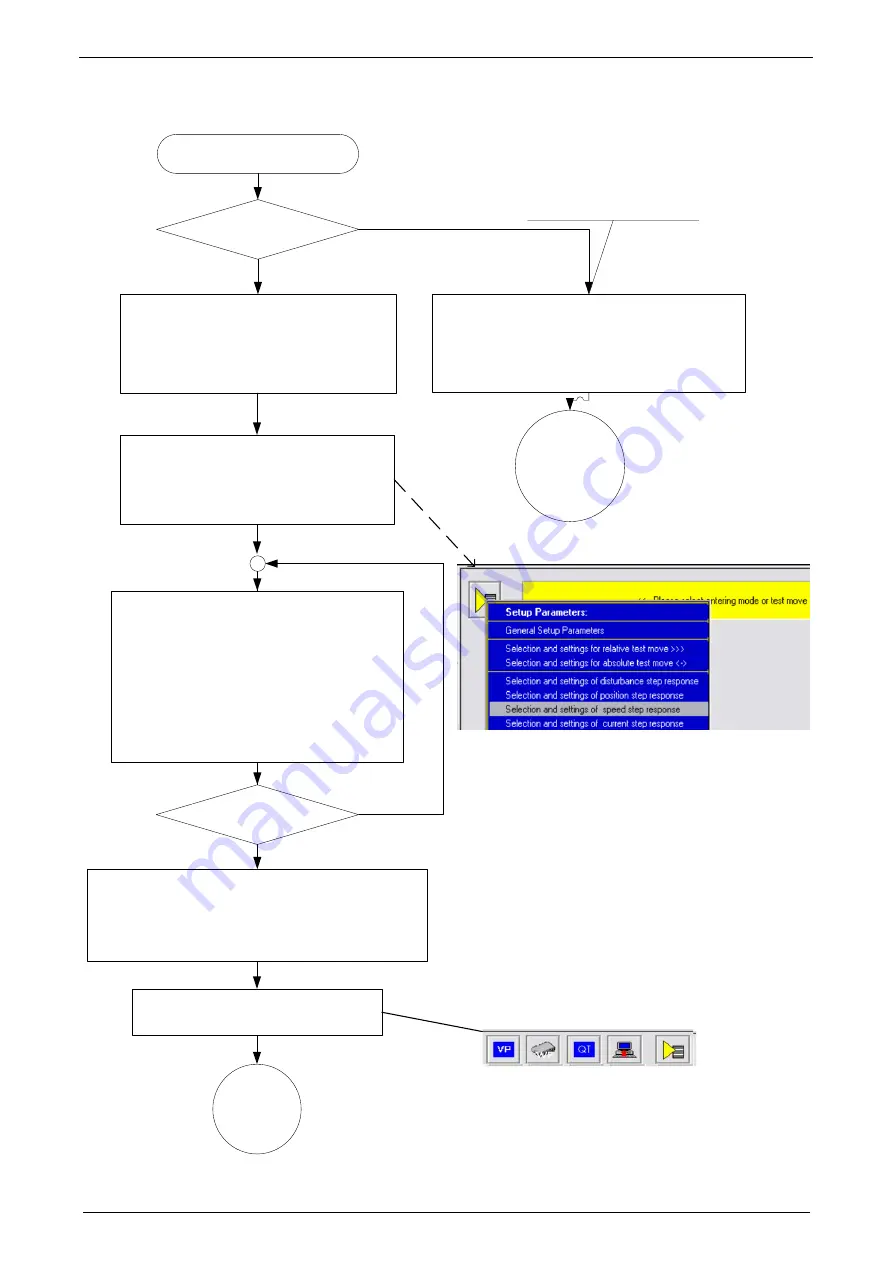
Parker EME
Setting up Compax3
192-120103 N13 C3I20T11 / C3I32T11 December 2010
231
Flow chart controller optimization of a direct drive
“Controller optimization direct
drive”
Is it a PowerRod?
Status controller with disturbance torque
-“Observer time constant” (Obj. 2120.1) >=125µs
(the higher the value, the slower the observer)
- “Activate disturbance value” (Obj. 2120.7)=1
yes
no
Default settings for PowerRod:
1.) “following error filter” (Obj. 2200.24) = 1470µs
2.) “following error dead zone” (Obj. 2200.20) = 0.025 mm
3.) “Friction feedforward” (Obj. 2200.21) = 0 mA
Vary the default settings if needs be.
See chapters:
-“Control measures for
drives iinvolving friction”
Select speed jerk response in the setup window /
tab “parameter), select the size of the jerk and
define jerk.
Respect the setpoint speed and the actual speed
Smooth, stable behavior?
1.) “Observer time constant” (Obj. 2120.1) and Vary filter of
observed disturbance (Obj. 2120.5) increase “stiffness” (Obj.
2100.2) until the optimum is reached
2.) In systems with
high friction
, reduce “attenuation” (Obj.
2100.3) and increase “stiffness” (Obj. 2100.2) until the
optimum is reached.
3.) In the event of
optimization to speed constancy
,
increase “attenuation” (Obj. 2100.3) and reduce “stiffness” as
far as necessary (Obj. 2100.2) until the optimum is reached.
yes
no
Main diagram
Move over the entire positioning range, verify
the settings and correct if necessary.
Store settings with WF!
Stabilize controller with the aid of:
•
Decrease stiffness (Obj. 2100.2)
•
or/also reduce observer time constant (Obj. 2120.1)
•
or/also reduce control signal filter (Obj. 2120.1)
•
or/also modify attenuation (Obj. 2100.3)
“Controller
optimization
standard”