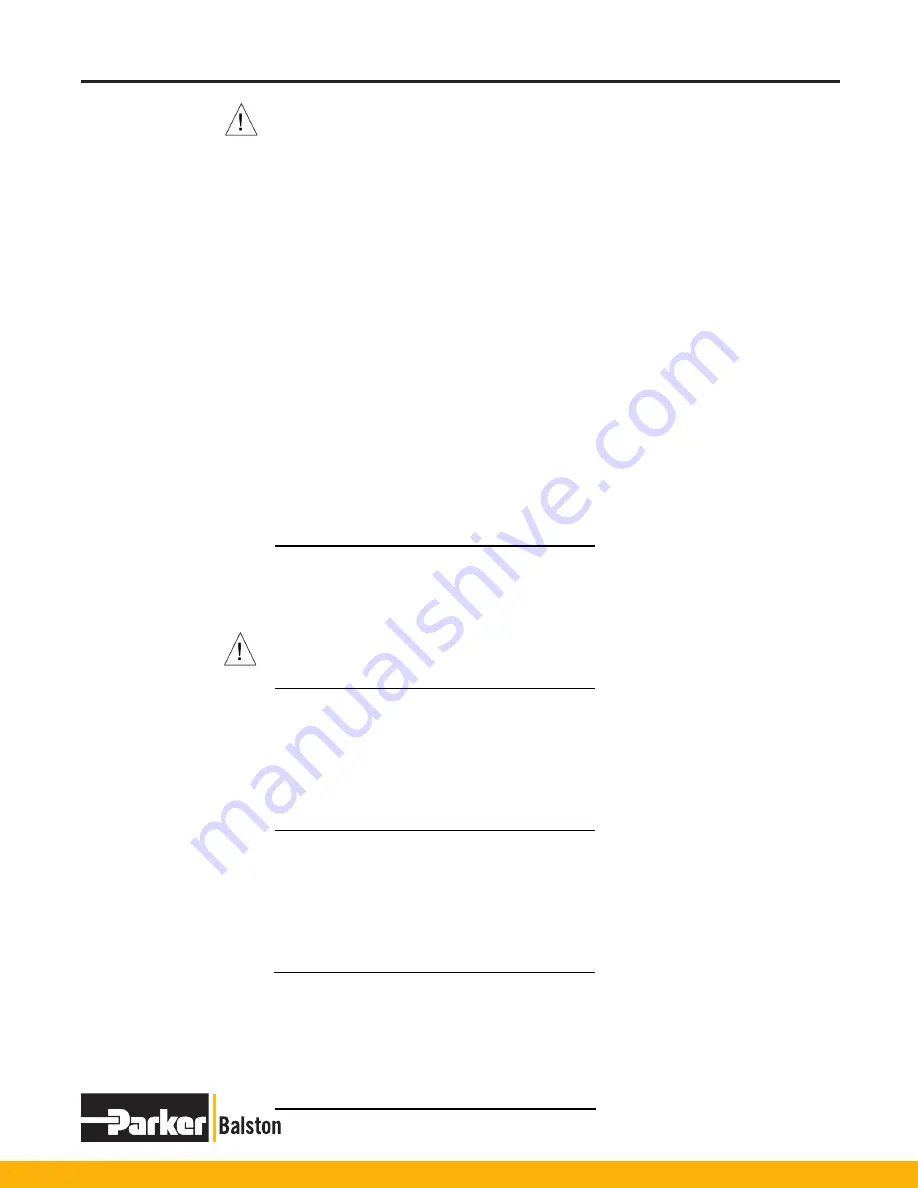
Bulletin TI-SteamSR-M
Installation, Operation and Maintenance Manual
Technical Information
Balston
®
Series "SR" Steam Filters
Parker Hannifin Corporation
Industrial Gas Filtration and
Generation Division
Haverhill, MA • 1-800-343-4048
www.balstonfilters.com
4
Operator must wear insulated gloves while servicing the Balston Steam Filter.
To replace a filter cartridge, shut off the steam valve and vent the steam from the housing
by opening the bleeder valve slowly (on multiple housing assemblies, one bleeder valve will
vent all of the housings). Loosen the external compression ring, using the spanner wrench
supplied. Lift the bowl off the filter. Unscrew the element retainer and remove it from the tie
rod. Pull the used filter cartridge off the support core. Slide the new filter cartridge down on
the support core and replace the element retainer on the tie rod, making sure the spring is
compressed. Replace the bowl and tighten the external compression ring with the spanner
wrench. Close the bleeder valve. Write the date of the filter cartridge change on the date tag
attached to the housing. Changing a filter cartridge takes approximately 5 minutes.
Note:
Each time a filter cartridge is changed, spread a light coat of lubricant on the rubber
sealing ring and on the threads of the metal compression ring. A new seal and lubricant is
included with each box of replacement filter cartridges.
The Balston Steam Filters are equipped with inverted bucket traps which function as auto-
matic condensate drains. An integral strainer is included with the trap and may occasionally
become plugged with pipe scale or other debris. To clean the debris from the screen, simply
remove the steam trap from the filter and back flush the trap with tap water.
A continuous discharge of live steam accompanied by a violent bucket rattle, indicates that
the trap has lost its prime. This can usually be corrected by closing the inlet valve for a few
minutes and then gradually opening it.
Caution:
Remove all steam pressure from filter before removing trap. After backflushing,
reassemble trap to filter using Rectorseal
(TM) ®
#5, or equivalent, on the threads.
How to Change
the Filter
Cartridge
Steam Trap
Maintenance
Principal
Specifications
23/75 SR
Ports
1" NPT
Condensate Drain Connection
1/2" NPT
Bleeder Valve Outlet
1/4" NPT
Max Operating Pressure
125 psig
Max Operating Temperature
350°F
Flow Rate
500 lb/hr
Materials of Construction
304/304L
Seals
EPR
SP2-23/75SR, SP3-23/75SR
Ports
1-1/2" NPT
Condensate Drain Connection
1/2" NPT
Bleeder Valve Outlet
1/4" NPT
Max Operating Pressure
125 psig
Max Operating Temperature
350°F
Flow Rate
1000, 1500 lb/hr
Materials of Construction
304/304L
Seals
EPR
SP4-23/75SR, SP6-23/75SR
Ports
2" NPT
Condensate Drain Connection
1/2" NPT
Bleeder Valve Outlet
1/4" NPT
Max Operating Pressure
125 psig
Max Operating Temperature
350°F
Flow Rate
2000, 3000 lb/hr
Materials of Construction
304/304L
Seals
EPR
Since the Steam Filter is installed upstream from the steam control valve, it is exposed to
steam at full line pressure at all times, regardless of the equipment operating schedule. As
a result of this constant exposure, the filter cartridge should be replaced every six weeks
regardless of the frequency of use of the equipment downstream. If the filter cartridge is
allowed to remain in service considerably longer than six weeks, the resin binder in the car-
tridge will weaken and the cartridge will no longer filter at its initial efficiency. Filter cartridge
life is based on steam pressure up to 125 psig (8.6 barg). Record the date of the cartridge
replacement on the tag attached to the filter housing.
When to Change the
Filter Cartridge
Maintenance