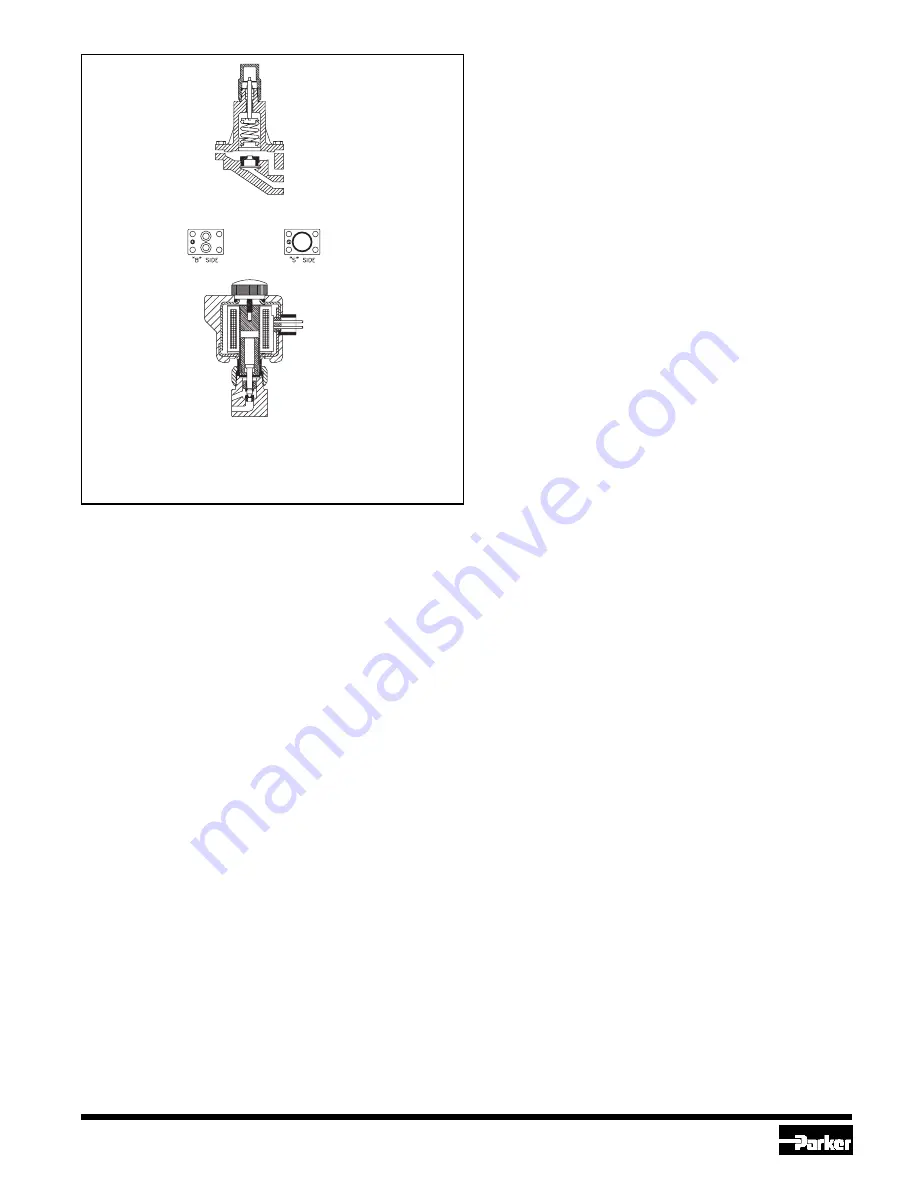
Refrigerating Specialties Division
7
Maintenance and Service General Procedure:
Before disassembly of regulator, make certain that all refrigerant has
been removed (pumped out) from the regulator and its companion
strainer where one is used. Read Safety Bulletin RSBCV.
Dirt In the system Is the greatest single cause of regulator malfunction.
All screens or filters must be cleaned or replaced when they become
dirty. At start up it is especially important that these Items are cleaned
or changed frequently. When the RSF close-coupled companion
strainers are used, maintain according to instructions in Bulletin
DN00-10. Moisture in halocarbon systems in particular can cause
corrosion or form ice, causing the piston to freeze in position.
Filter-driers should be used and maintained for halocarbon systems.
Before deciding to disassemble a regulator for servicing, the following
investigations should be made:
Check the manual opening stem; it should be turned in for automatic
operation.
Check the regulator setting to make sure it is properly adjusted. Turn
adjusting screw slowly to see if regulator responds. Check regulator
pressure range; if wrong, range spring must be replaced.
Check other system components for proper operation. Make sure
that the regulator receives the proper electrical signal where modular
pilot solenoids are used. Make sure they are same as the power
supply.
Check hand valves in the system to make sure they are open or closed
as required and the system is receiving liquid or gas as the case may
be.
Electrical
The Refrigerating Specialties Division molded water resistant Class
“B” solenoid coil is designed for long life and powerful opening force.
The standard coil housing meets NEMA 3R and 4 requirements. This
sealed construction can withstand direct contact with moisture and
ice. The coil housing far exceeds the requirements of NEMA Standard
ICS, 1-110.57 salt spray test for rust resistance.
By definition, Class “B” coil construction will permit coil temperatures,
as measured by resistance method, as high as 130°C (266°F). Final
coil temperatures are a function of both fluid and ambient temperatures.
The higher fluid temperatures require lower ambient temperatures so
the maximum coil temperature is not exceeded. Conversely, low fluid
temperatures permit higher ambient temperatures.
The supply circuits must be properly sized to give adequate voltage at
the coil leads even when other electrical equipment is operating. The
coil is designed to operate with line voltage from 85% to 110% of rated
coil voltage. Operating with a line voltage above or below these limits
may result in coil burnout. Also, operating with line voltage below the
limit will definitely result in lowering the valve opening pressure differential.
Power consumption during normal operation will be 33 watts or less.
Inrush and running current is listed below:
Encapsulated
Inrush
Running
Fuse
Standard Coil
Current
Current
Size
Volts/Hertz
(Amps)
(Amps)
(Amps)
120/60 (Blue leads)
1.18
0.46
1
208/60 (Blue & Red leads)
0.63
0.26
1
240/60 (Red leads)
0.60
0.23
1
440/60 (Yellow & Red leads)
0.39
0.13
1
115/50 (Yellow & Blue leads)
1.22
0.21
1
230/50 (Yellow leads)
0.65
0.26
1
Other
Contact Factory
On transformer coil the 6 volt leads are always black.
Fig. 12
S6A
MODULAR SOLENOID PILOT
A2D
MODULAR PRESSURE PILOT
MODUPLATE
Safe Operation (See also Bulletin RSBCV)
People doing any work on a refrigeration system must be qualified and
completely familiar with the system and the Refrigerating Specialties
Division valves involved, or all other precautions will be meaningless.
This includes reading and understanding pertinent Refrigerating
Specialties Division product Bulletins, and Safety Bulletin RSB prior to
installation or servicing work.
Where cold refrigerant liquid lines are used, it is necessary that certain
precautions be taken to avoid damage which could result from liquid
expansion. Temperature increase in a piping section full of solid liquid
will cause high pressure due to the expanding liquid which can possibly
rupture a gasket, pipe or valve. All hand valves isolating such sections
should be marked, warning against accidental closing, and must not be
closed until the liquid is removed. Check valves must never be installed
upstream of solenoid valves, or regulators with electric shutoff, nor
should hand valves upstream of solenoid valves or downstream of
check valves be closed until the liquid has been removed. It is advisable
to properly install relief devices in any section where liquid expansion
could take place.
Avoid all piping or control arrangements which might produce thermal or
pressure shock.
For the protection of people and products, all refrigerant must be removed
from the section to be worked on before a valve, strainer, or other
device is opened or removed.
Flanges with ODS connections are not suitable for ammonia service.
Warranty
All Refrigerating Specialties Products are warranted against defect in
workmanship and materials for a period of one year from date of shipment
from factory. This warranty is in force only when products are properly
installed, field assembled, maintained and operated in use and service
as specifically stated in Refrigerating Specialties Catalogs or Bulletins
for normal refrigeration applications, unless otherwise approved in writing
by Refrigerating Specialties Division. Defective products, or parts thereof,
returned to the factory with transportation charges prepaid and found to
be defective by factory inspection will be replaced or repaired at
Refrigerating Specialties’ option, free of charge, F.O.B. factory. Warranty
does not cover products which have been altered or repaired in the
field; damaged in transit, or have suffered accidents, misuse, or abuse.
Products disabled by dirt, or other foreign substances will not be
considered defective.
THE EXPRESS WARRANTY SET FORTH ABOVE CONSTITUTES THE
ONLY WARRANTY APPLICABLE TO REFRIGERATING SPECIALTIES
PRODUCTS, AND IS IN LIEU OF ALL OTHER WARRANTIES,
EXPRESSED OR IMPLIED, WRITTEN OR ORAL, INCLUDING ANY
WARRANTY OR MERCHANTABILITY, OR FITNESS FOR A PARTICULAR
PURPOSE. No employee, agent, dealer or other person is authorized to
give any warranties on behalf of Refrigerating Specialties, nor to assume,
for Refrigerating Specialties, any other liability in connection with any of
its products.