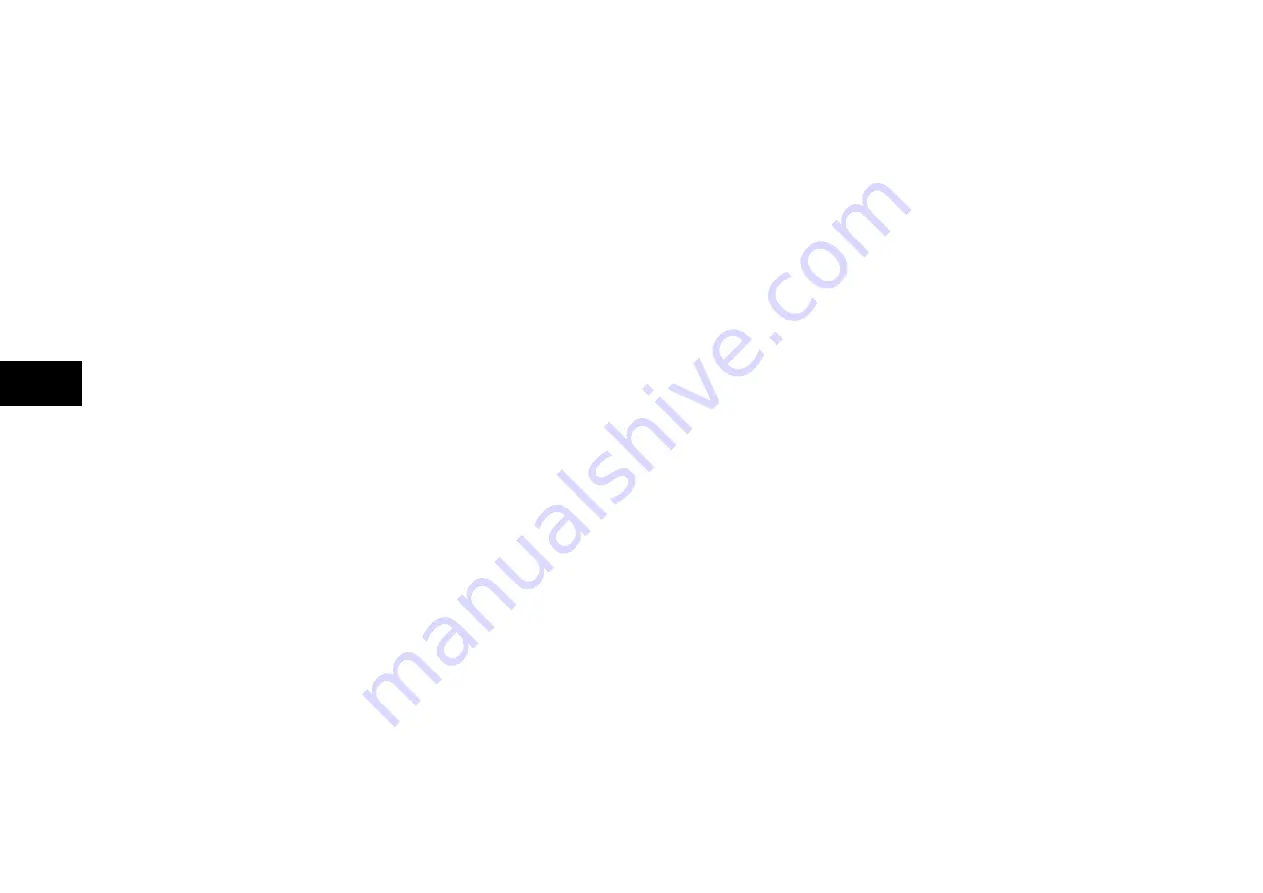
Operating the Drive
Page
7-18
890CS Common Bus Supply - Frames B & D; 890CD Common Bus Drive and 890SD Standalone Drive - Frames B, C & D
8
9
10
11
A
B
C
D
1
2
3
4
5
6
7
E
Application Advice
Application advice is available through our Technical Support Department, who can also arrange for on-site
assistance if required. Refer to the back cover of this manual for the address of your local Parker SSD
Drives company.
♦
Always use gold flash relays, or others designed for low current operation (5mA), on all control wiring.
♦
Remove all power factor correction equipment from the motor side of the drive before use.
♦
Avoid using motors with low efficiency and small cos ø (power factor) as they require a larger kVA
rated drive to produce the correct shaft kW.
Brake Motors
Brake motors are used in applications requiring a mechanical brake for safety or other operational reasons.
The motor can be a standard induction motor fitted with an electro-mechanical brake, or it could be a
special conical rotor machine. In the case of a conical rotor machine the spring-loaded brake is controlled
by the motor terminal voltage as follows:
♦
At rest the motor is braked.
♦
When the motor is energised an axial component of the magnetic field due to the conical air-gap
overcomes the force of the brake spring and draws the rotor into the stator. This axial displacement
releases the brake and allows the motor to accelerate like a normal induction motor.
♦
When the motor is de-energised the magnetic field collapses and the brake spring displaces the rotor,
pushing the brake disc against the braking surface.
Drives can be used to control the speed of conical rotor brake motors since the linear V/F characteristic
maintains the motor magnetic field constant over the speed range. It will be necessary to set the FIXED
BOOST parameter to overcome motor losses at low speed (see the FLUXING menu on the Keypad).