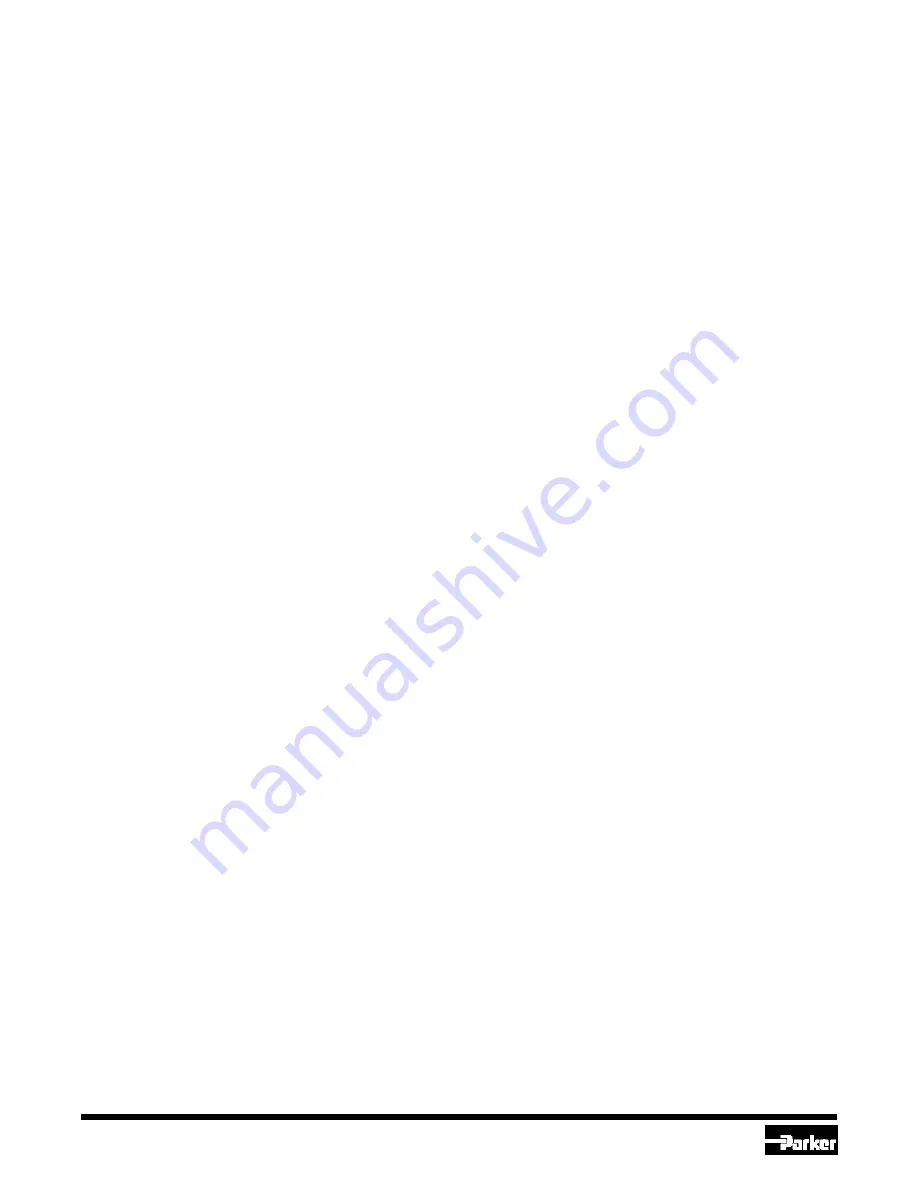
Refrigerating Specialties Division
4
ideal tightening torque is 11 ft. lbs. (1.5 kg-m).
Valve is now ready to be adjusted for normal
operation.
If close coupled strainer is used, it may be
cleaned before putting the valve back in opera-
tion. The regulator must be tested for leaks with
refrigerant gas or other appropriate gas before
the system is put into operation.
After the General Procedure for disassembly,
inspect the Pilot Seat (18) top seating surface
for dirt, wear or damage. Remove seat from
valve body and clean, lap on a flat plate or
replace as necessary. Examine the diaphragm
region which contacts the seat surface, look for
dirt, heavy scratches or corrosion. If the dia-
phragm cannot be easily wiped clean, it should
be replaced. Reassemble the regulator follow-
ing the General Procedure.
Maintenance and Service
General Procedure:
Dirt in the system is the greatest single cause of
regulator malfunction. All screens or filters must
be cleaned or replaced when they become
dirty. At start up it is especially important that
these items are cleaned or changed frequently.
When the RSF close-coupled companion strain-
ers are used, maintain according to instruction
in Bulletin 00-10. Moisture in halocarbon sys-
tems in particular can cause corrosion or form
ice, causing the piston to freeze in position.
Filter-driers should be used and maintained for
halocarbon systems.
Before deciding to disassemble a regulator for
servicing, the following investigations should
be made:
Check the manual opening stem; it should be
turned in for automatic operation.
Check the regulator setting to make sure it is
properly adjusted. Turn adjusting screw slowly
to see if regulator responds. Check regulator
pressure range; if wrong, range spring must be
replaced.
Check other system components for proper op-
eration. Check hand valves in the system to
make sure they are open or closed as required
and the system is receiving liquid or gas as the
case may be.
Before disassembly of regulator, make certain
that all refrigerant has been removed (pumped
out) from the regulator and it companion strainer
where one is used. Read Safety Bulletin
RSBCV.
Safe Operation (See also Bulletin RSBCV)
People doing any work on a refrigeration
system must be qualified and completely
familiar with the system and the Refrigerat-
ing Specialties Division valves involved, or
all other precautions will be meaningless.
This includes reading and understanding
pertinent Refrigerating Specialties Division
product Bulletins and Safety Bulletin RSBCV
prior to installation or servicing work.
Where cold refrigerant liquid lines are used, it is
necessary that certain precautions be taken to
avoid damage which could result from liquid expan-
sion. Temperature increase in a piping section full of
solid liquid will cause high pressure due to the
expanding liquid which can possibly rupture a gas-
ket, pipe or valve. All hand valves isolating such
sections should be marked, warning against acci-
dental closing, and must not be closed until the liquid
is removed. Check valves must never be installed
upstream of solenoid valves, or regulators with
electric shut-off, nor should hand valve upstream of
solenoid valves or downstream of check valves be
close until the liquid has been removed. It is advis-
able to properly install relief devices in any section
where liquid expansion could take place.
Avoid all piping or control arrangements which might
produce thermal or pressure shock. For the protec-
tion of people and products, all refrigerant must be
removed from the section to be worked on before a
valve, strainer, or other device is opened or re-
moved. Flanges with ODS connections are not
suitable for ammonia service.