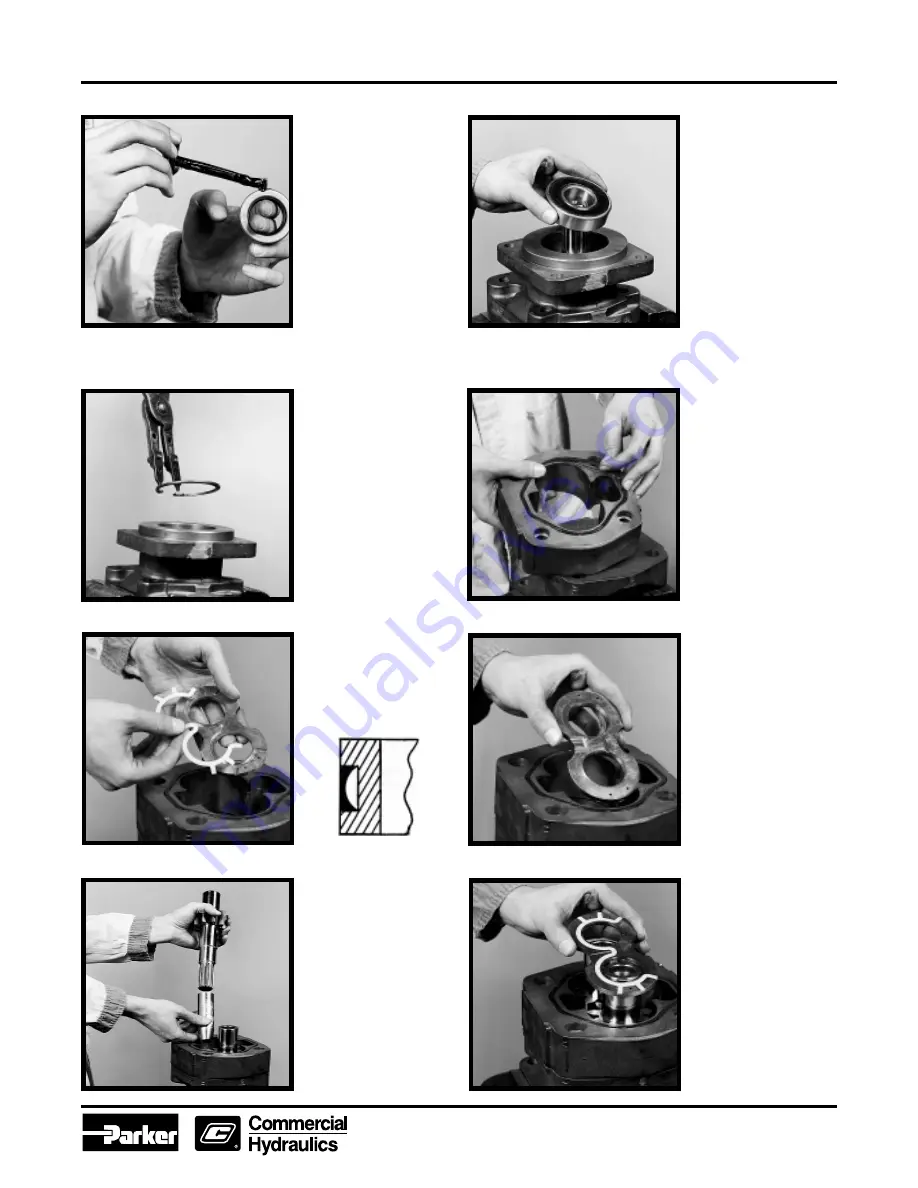
PGP/PGM 300 Series
Service Manual HY09-SM300/US
8
Parker Hannifin Corporation
Gear Pump Division
Youngstown, OH
9) Before inserting a new lip
seal in the shaft end cover,
coat the outer edge of the
lip seal and its recess with
Permatex Aviation
Form-A-Gasket™ No. 3
non-hardening sealant or
equivalent. With the metal
side of the lip seal up, press
it into the mounting flange
side of the shaft end cover
with an arbor press and bar
(see Tool List on page 4).
Be careful not to damage
the lip of the seal. Press in
until flush with the recess.
Wipe off excess sealant.
10) If the unit is equipped
with an outboard bearing,
guide the bearing into its
recess in the shaft end
cover. This is a light
press fit. It may be
necessary to lightly tap
the bearing into the
bore.
11) Install the snap ring in
the groove to retain the
outboard bearing.
12) Grease the new gasket
seals and insert them into
the grooves in both sides of
all gear housings. Position
the first gear housing over
the shaft end cover and
dowels. Tap it with a soft
hammer until it rests tightly
against the shaft end cover.
Be careful not to pinch the
gasket seal. Also be sure
that the large rounded core
is on the inlet side.
16) Slip the thrust plate
with the seal over the gear
journals and into the
housing bore. The flat side
of the seal should face up
with the relief groove
facing the outlet side. (For
single pump assemblies
go directly to Step #21).
15) Slide the driven gear
through the housing and into
the bushing in the shaft end
cover. Coat the steel sleeve
tool with grease. Place the
lightly-greased drive shaft
inside the sleeve and slide
both through the shaft end
cover with a twisting motion,
until the integral gear rests
against the thrust plate.
Avoid damaging the double
lip seal. Remove the steel
sleeve. Squirt clean oil over
the gears.
14) Gently slip the thrust
plate through the gear
housing and into place on
the shaft end cover. The
channel seal from Step
#13 should face the shaft
end cover. The relief
groove in the plate should
face the outlet side of the
pump.
13) Assemble the channel
seals into the grooves in
the thrust plates with the
flat side of the seal facing
away from the thrust plate
as shown below.
Flat Side
of Seal
Thrust
Plate